Leds, Car2912te series front-end, Preliminary data sheet – GE Industrial Solutions CAR2912TE series User Manual
Page 20: Failure predictions, Remote programming
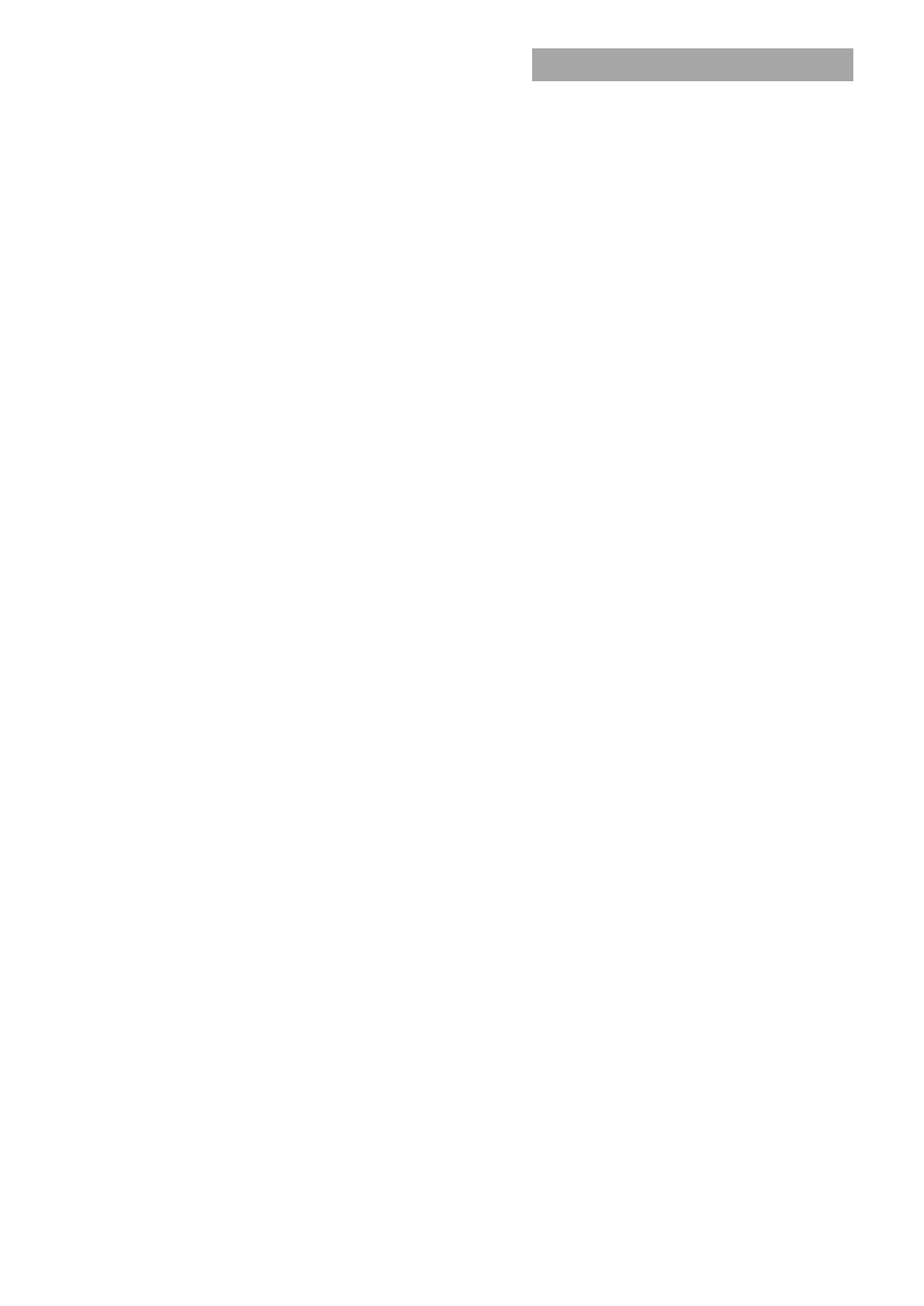
GE
Preliminary Data Sheet
CAR2912TE series front-end
Input: 90Vac to 264Vac; Output: 12Vdc @ 2900W; 3.3 or 5Vdc @ 4A Standby
October 21, 2013
©2013 General Electric Company. All rights reserved.
Page 20
within the power supply) until the power supply configures its
address.
The recommended procedure for hot plug is the following:
The system controller should poll the module_present signal
to verify when a power supply is inserted into the system.
When a new module is detected the system controller should
cease any communications with the power system for 15
seconds. At the end of the time out all communications can
resume. Note that although hot-plug should not affect
ongoing communications, if a discrepancy should arise the
error should get picked up by the PEC calculation. Ofcourse
the system controller could always use the module_present
signal as an indicator to ignore communications that are
currently taking place.
Failure Predictions
Alarm warnings that do not cause a shutdown are indicators
of potential future failures of the power supply. For example,
if a thermal sensor failed, a warning is issued but an
immediate shutdown of the power supply is not warranted.
Another example of potential predictive failure mechanisms
can be derived from information such as fan speed when
multiple fans are used in the same power supply. If the speed
of the fans varies by more than 20% from each other, this is
an indication of an impending fan wear out.
The goal is to identify problems early before a protective
shutdown would occur that would take the power supply out
of service.
Information only alarms:
The following alarms are for
information only, they do not cause a shutdown
•
Over temperature warning
•
V
out
out-of-limits
•
Output voltage lower than bus
•
Unit in Power Limit
•
Thermal sensor failed
•
Or’ing (Isolation) test failure
•
Power delivery
•
Stby out of limits
•
Communication errors
LEDs
Two LEDs are located on the front faceplate. The AC_OK LED
provides visual indication of the INPUT signal function. When
the LED is ON GREEN the power supply input is within normal
design limits.
The second LED DC/FLT is a dual-state LED. When GREEN
there are no faults and DC output is present. When ‘blinking’
a fault condition exists but the power supply may still provide
some output power. When RED , a fault condition exists and
the power supply has been shut down, it does not provide
any output power.
Remote programming
This section describes at a high-level the re-programming
process for the three internal micro controllers inside the
power supply.
The process has been implemented in visual basic by GE
Critical Power for controller based systems positioned
primarily for the telecommunications industry. GE Critical
Power will share its development with customers who are
interested to deploy the re-programming capability into their
own controllers.
For some customers internal system re-programming is
either not feasible or not desired. These customers could
obtain a re-programming kit from GE Critical Power. This kit
would enable the modules to be reprogrammed outside of
the system.
Initialization:
If the re-programming/upgrade is going to be
executed in the system, the module to be re-programmed
must be taken OFF line prior to initiating re-programming. If
the module is not taken OFF line by the system controller, the
boot loader will turn OFF the output prior to continuing with
the re-programming operation.
Make sure that sufficient power is provided by the remaining
modules on-line so that system functionality is not
jeopardized.
Execution:
•
Verify that the upgrade firmware is compatible with
the module that is about to be upgraded.
•
Read the present state of Application Status to
determine that the Boot loader is available
•
Read Memory Capability device specific data
•
Instruct the boot loader to enter ‘boot block’. (i.e.
start the reprogram process). During this process if
the output of the module was not turned OFF the
boot loader will turn OFF the output.
•
Instruct the Boot loader to erase the application
program of the device to be reprogrammed
•
Read back Application Status confirming erase
completion
•
Download the upgraded program into the device
•
Periodically read back Application Status to verify
that no errors are flagged by the Boot loader
•
Instruct the Boot loader when the download is done.
The Boot loader will calculate the downloaded
program’s checksum and compare it to the
checksum attached at the end of the downloaded
program.
•
Read back Application Status to confirm that no
errors occurred.
•
Send ‘exit’ to Boot loader thus instructing the Boot
loader to start the application and reconnect the
output of the module.