HEIDENHAIN TNC 640 (34059x-01) ISO programming User Manual
Page 507
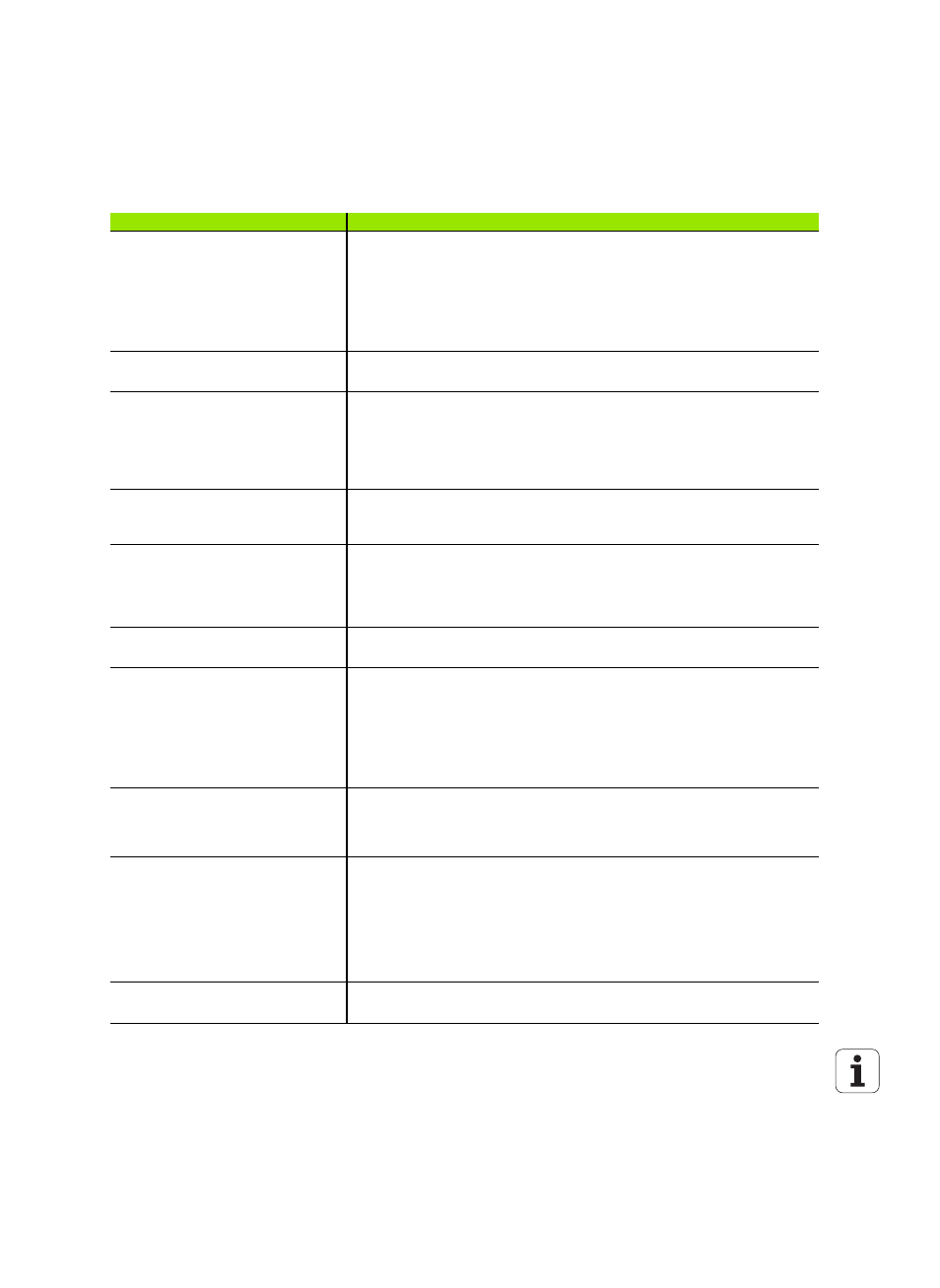
HEIDENHAIN TNC 640
507
Automatic cancelation of tool radius
compensation
Block with R0
DEP
block
END PGM
Block with R0
DEP
block
PGM CALL
Programming of Cycle 10 ROTATION
Program selection
NC blocks with M91
No consideration of tool radius
compensation
Consideration of tool radius
compensation
Tool shape compensation
Tool shape compensation is not
supported, because this type of
programming is considered to be axis-
value programming, and the basic
assumption is that axes do not form a
Cartesian coordinate system
Tool shape compensation is supported
Mid-program startup in a point table
The tool is positioned above the next
position to be machined
The tool is positioned above the last
position that has been completely
machined
Empty CC block (pole of last tool position
is used) in NC program
Last positioning block in the working
plane must contain both coordinates of
the working plane
Last positioning block in the working
plane does not necessarily need to
contain both coordinates of the working
plane. Can cause problems with RND or
CHF
blocks
Axis-specific scaling of RND block
RND
block is scaled, the result is an
ellipse
Error message is issued
Reaction if a contour element with
length 0 is defined before or after a RND
or CHF block
Error message is issued
Error message is issued if a contour
element with length 0 is located before
the RND or CHF block
Contour element with length 0 is
ignored if the contour element with
length 0 is located after the RND or CHF
block
Circle programming with polar
coordinates
The incremental rotation angle IPA and
the direction of rotation DR must have
the same sign. Otherwise, an error
message will be issued
The algebraic sign of the direction of
rotation is used if the sign defined for DR
differs from the one defined for IPA
Tool radius compensation on circular arc
or helix with angular length = 0
The transition between the adjacent
elements of the arc/helix is generated.
Also, the tool axis motion is executed
right before this transition. If the
element is the first or last element to be
corrected, the next or previous element
is dealt with in the same way as the first
or last element to be corrected
The equidistant line of the arc/helix is
used for generating the tool path
Checking the algebraic sign of the depth
parameter in fixed cycles
Must be deactivated if Cycle 209 is used No restrictions
Function
TNC 640
iTNC 530