6 thr ead and under c ut cy cles – HEIDENHAIN SW 688945-03 User Manual
Page 275
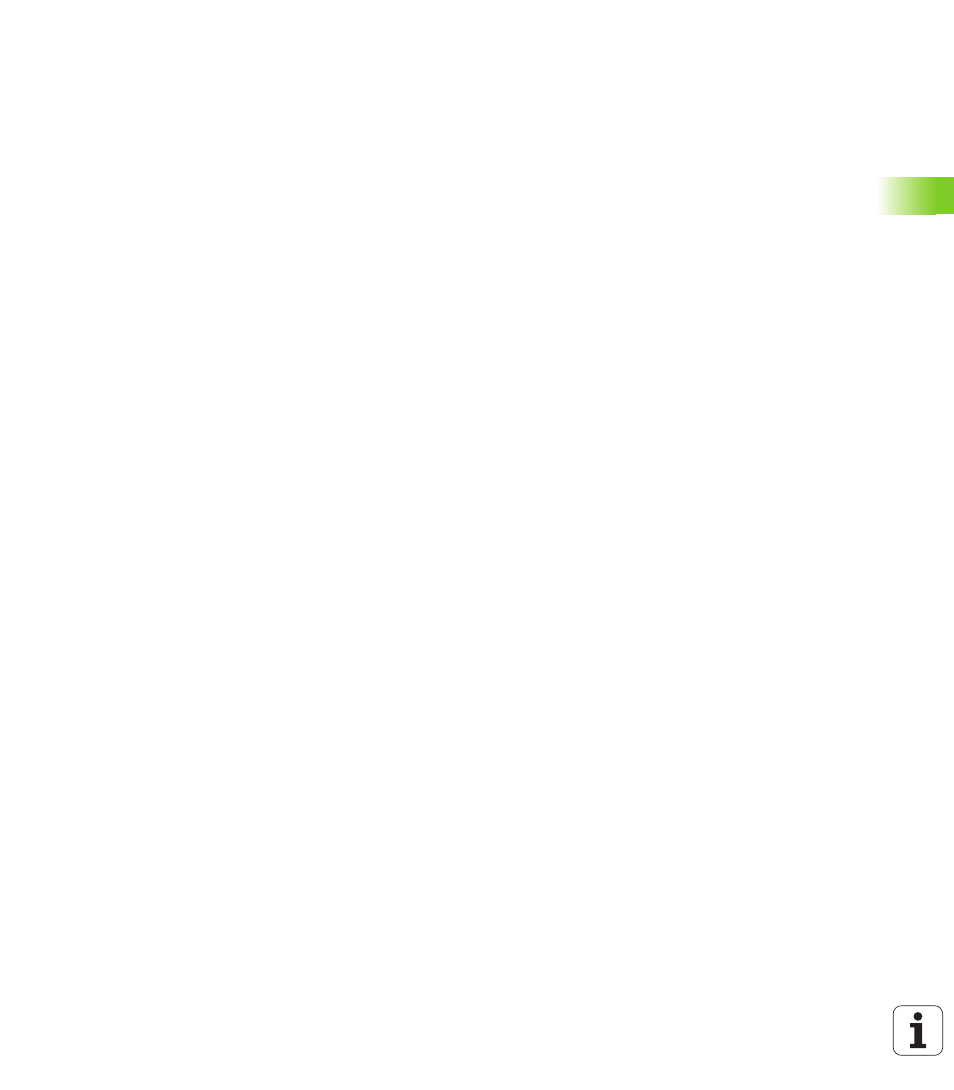
HEIDENHAIN CNC PILOT 620/640
275
4.6 Thr
ead and under
c
ut cy
cles
Type of machining for technology database access: Finishing
All parameters that you enter will be accounted for—even if the
standard table prescribes other values. If the parameters I, K, W and
R are not defined, the CNC PILOT determines these parameters from
"FP" in the standard table (see "DIN 76—undercut parameters" on
page 573).
Cycle run
1
Approach workpiece from starting point
to the cylinder starting point X1, or
for the thread chamfer
2
Machine thread chamfer, if defined
3
Finish cylinder up to beginning of undercut
4
Pre-machine undercut, if defined
5
Machine undercut
6
Finish to end point X2 on plane surface
7
Return
Without return: Tool remains at the end point on plane
surface
With return: Retract and return diagonally to starting point
8
Move to the tool change point according to the G14 setting
B
Cylinder start chamfer (default: no start chamfer)
WB
First-cut angle (default: 45°)
RB
First-cut radius (default: no input = no element): Positive
value: First-cut radius, negative value = chamfer
G47
Safety clearance (see page 124)—evaluated only if "Omit
paths of rapid traverse" is active.
MT
M after T: M function that is executed after the tool call T
MFS
M at beginning: M function that is executed at the
beginning of the machining step
MFE
M at end: M function that is executed at the end of the
machining step
WP
Displays which workpiece spindle is used to process the
cycle (machine-dependent)
Main drive
Opposing spindle for rear-face machining