Additional factors of cut quality -16 – Hypertherm HT4001 Plasma Arc Cutting System User Manual
Page 107
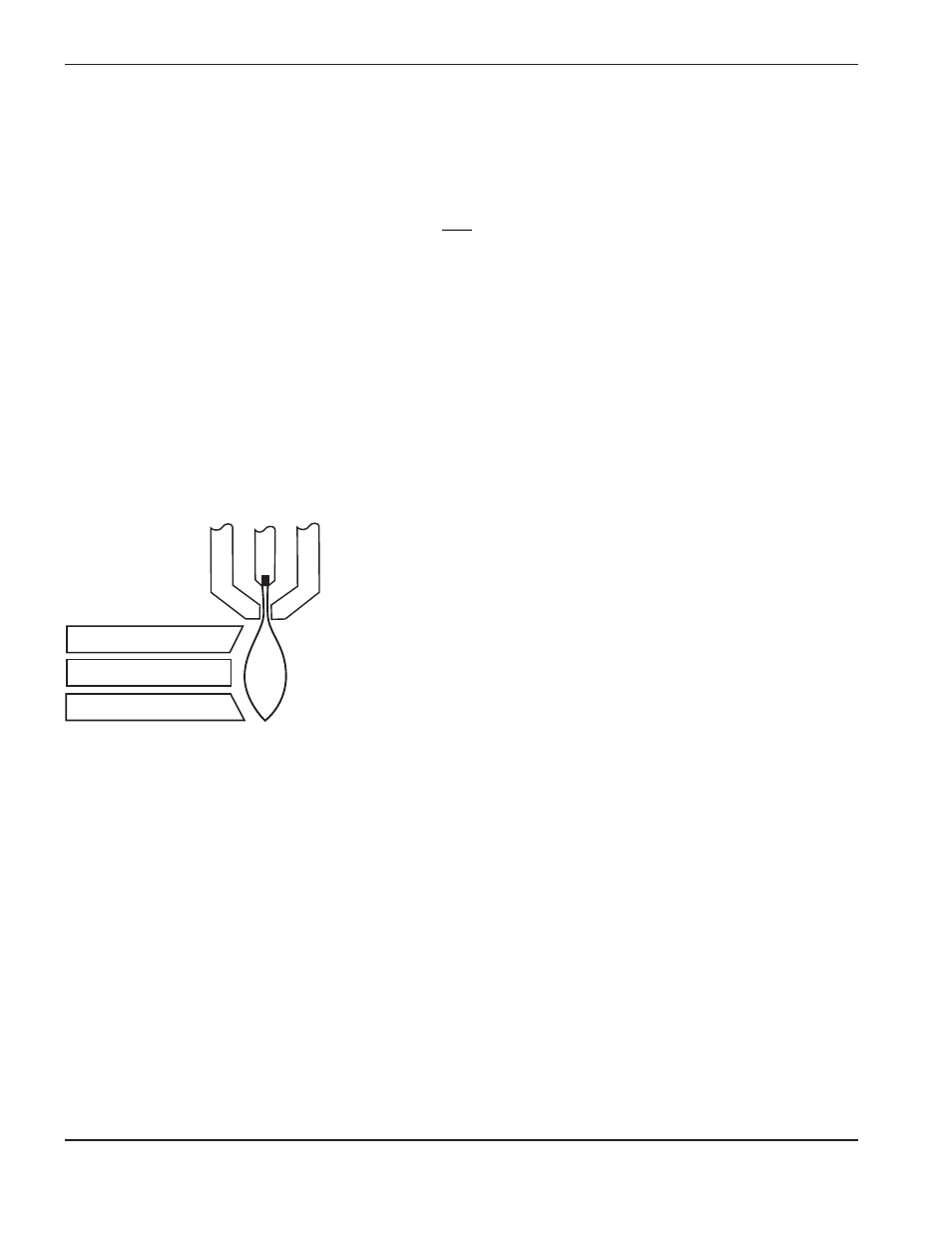
OPERATION
17
5-16
HT4001
Instruction Manual
Additional Factors of Cut Quality
Cut Angle
A cut part whose 4 sides average less than 4° of cut angle is considered acceptable.
Note:
The squarest cut angle will be on the right side with respect to the forward motion of the torch.
Note:
To determine whether a cut-angle problem is being caused by the plasma system or the
drive system, make a test cut and measure the angle of each side. Next, rotate the torch
90° in its holder and repeat the process. If the angles are the same in both tests, the
problem is in the drive system.
If a cut-angle problem persists after “mechanical causes” have been eliminated (See Tips for Table and Torch,
previous page), c
heck the t
orch-to-work distance, especially if cut angles are all positive or all negative.
• A positive cut angle results when more material is removed from the top of the cut than from the bottom.
• A negative cut angle results when more material is removed from the bottom of the cut.
Dross
Low-speed dross forms when the torch’s cutting speed is too slow and the arc shoots ahead. It forms as a heavy,
bubbly deposit at the bottom of the cut and can be removed easily. Increase the speed to reduce the dross.
High-speed dross forms when the cutting speed is too fast and the arc lags behind. It forms as a thin, linear bead of
solid metal attached very close to the cut. It is welded to the bottom of the cut and is difficult to remove. To reduce
high-speed dross:
• Decrease the cutting speed.
• Decrease arc voltage, to decrease the torch-to-work distance.
• Increase O
2
in the shield gas to increase the range of dross-free cutting speeds. (Only HyDefinition and
HT4400 systems can accommodate mixed-gas shield gases.)
Notes:
Dross is more likely to form on warm or hot metal than on cool metal. For example, the
first cut in a series of cuts will likely produce the least dross. As the workpiece heats up,
more dross may form on subsequent cuts.
Dross is more likely to form on mild steel than on stainless steel or aluminum.
Worn or damaged consumables may produce intermittent dross.
Cause
The torch is too low.
The torch is too high.
Square cut
\
Solution
Increase arc voltage to raise the torch.
Decrease arc voltage to lower the torch.
Positive cut angle
Negative cut angle
Problem