EFCO 8800 Series Assembly Instructions Vol.1 User Manual
Page 6
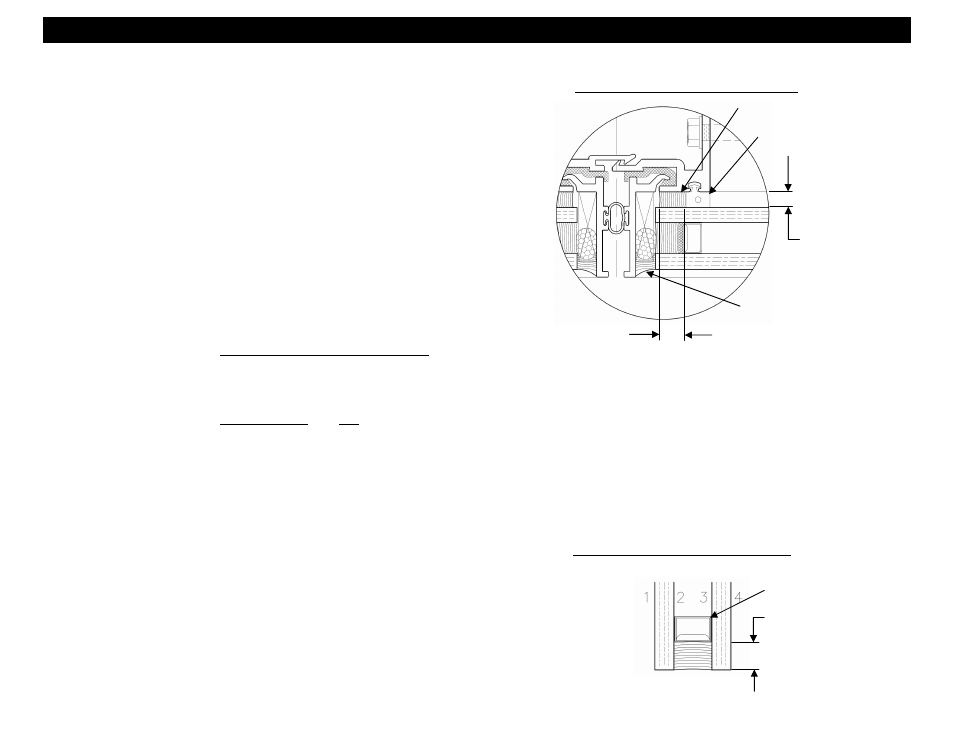
EFCO 2009
Page 6
Series 8700 / 8800 Unitized Curtain Wall Assembly Instructions - Volume 1
Section 1 - General Notes And Guidelines
recommendations for primers and substrate preparation required to obtain
adhesion. The chemical compatibility of all glazing materials and framing
sealants with each other and with like materials used in glass fabrication
must be established. Maintain caulk joints as shown in the approved shop
drawings. A 1” minimum joint is required at the head and jamb condition to
accommodate installation, building movements, and thermal expansion and
contraction.
H. STRUCTURAL SEALANT JOINTS - The maximum allowable size of the
glass lite is controlled by the width and depth of the structural silicone joint
combined with the specified design wind load (PSF or Pa). The stress on
the structural silicone must not exceed 20 PSI (137 KPa) for a 6:1 safety
factor.
In order to determine the structural silicone sealant contact width or bite
which adheres the glass to the frame, a calculation must be performed on a
job by job basis. The formula which determines the sealant width is based
on using a trapezoidal load distribution rule. This formula is expressed as
follows:
Structural Sealant =
0.5 x Short Span (ft) x Wind load (lb/ft²)
Bite or Contact Width (in) Sealant Design Strength (=20 lb/in²) x 12 in/ft
Example: Lite size is 48” x 60” and wind load for the project is 60 psf.
Structural Sealant =
0.5 x 4’ x 60 psf or 120 or .500”
Bite or Contact Width (in)
20 x 12 240
Sealant manufacturers, as a general rule, specify the structural sealant
depth (glue line) to be one half of the contact width for a 2:1 width to height
ratio. The glue line should not exceed 3/8” thick nor be less than 1/4” thick.
The standard joint size for Series 8800 is 1/2” x 1/4”. Note: Weather seals
must be applied a minimum of four hours after the application of the SSG
sealant joint to allow for proper cure time.
I APPROVED SOLVENT OR CLEANER - Degreasing solvents, such as
methyl ethyl ketone (MEK), toluene, xylene, acetone and mineral spirits
can been used to remove oils or other surface contaminants, but may leave
a residue film on the cleaned surfaces, which must be removed.
A solution
of fifty percent
Isopropyl alcohol and fifty percent water is recommended for
the final cleaning and preparation of substrates for sealant application.
Refer to the sealant manufacturer’s application instructions, ASTM C 1193 -
09, project specifications, and local environmental regulations for
requirements.
J. SECONDARY SEALANT JOINT DESIGN - The design of the secondary
sealant joint is based on the 50:50 load sharing principal where the I.G. unit
is comprised of two symmetrical lites of glass. The secondary sealant joint
that adheres the two lites of glass together only carries half the wind load
applied to the I.G. unit. Since the load is halved, the secondary sealant
contact width is half that of the SSG joint. Using the example earlier for the
1/2” x 1/4” SSG joint, the secondary sealant contact width for the I.G. unit in
the example is 1/4”.
Edge deletion is required on the coated surface (#2 or #3) for hard or soft
coated glazing products.
SECONDARY SEALANT JOINT DETAIL
STANDARD TUBULAR
SPACER RECOMMENDED
SECONDARY SEALANT
CONTACT WIDTH
STRUCTURAL SEALANT JOINT DETAIL
SEALANT DEPTH
(GLUE LINE)
STRUCTURAL SEALANT
CONTACT WIDTH
SPACER GASKET
SSG SEALANT JOINT
WEATHER SEAL
(Do not apply until the
SSG sealant joint has
cured for at least 4 hours.)