Carrier 16DF013-050 User Manual
Page 6
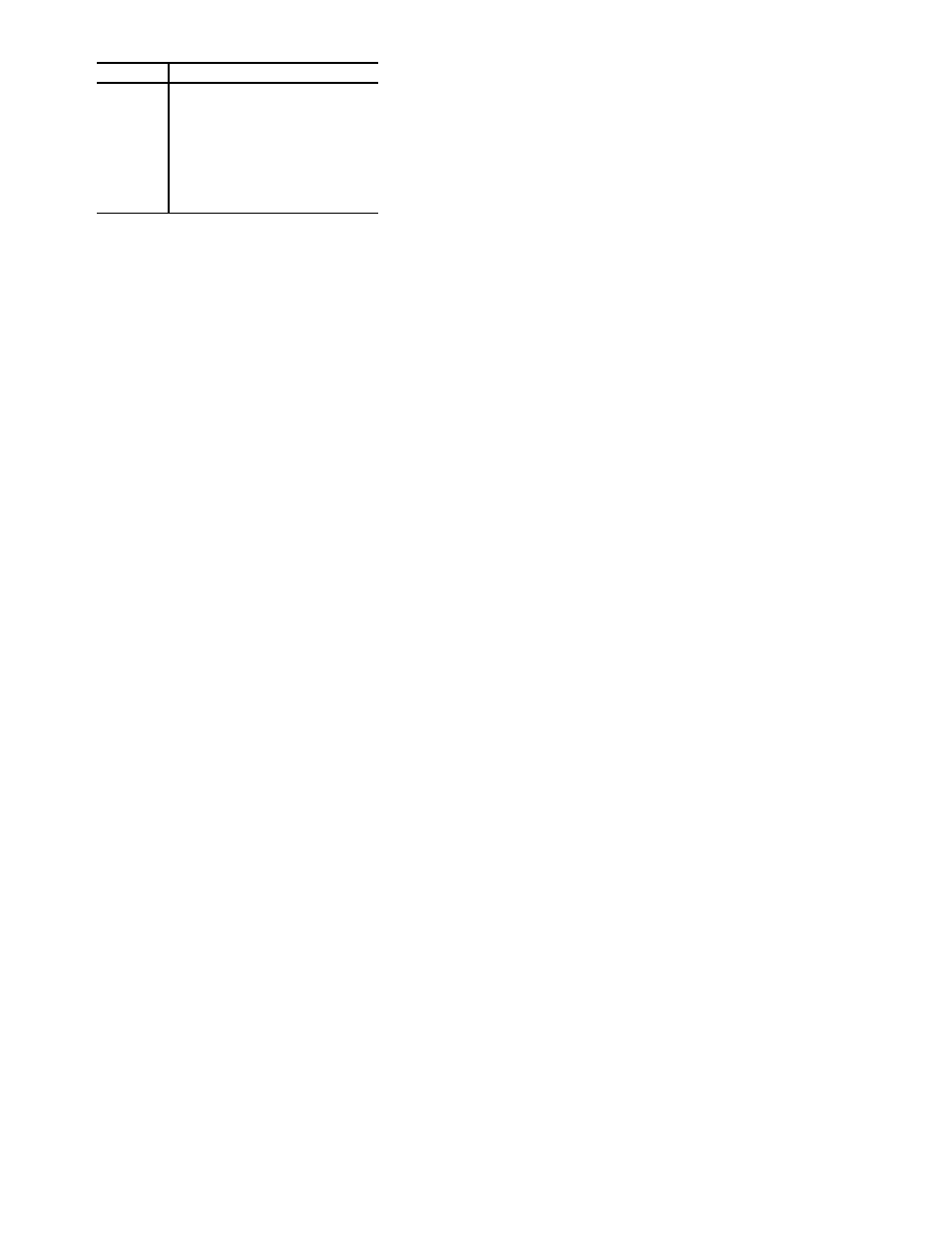
Table 1 — Valve Descriptions
VALVE
USE
A
Heating/Cooling Vapor
B
Heating/Cooling Liquid
C
Heat Exchanger Service
D
Palladium Cell Isolation
E
Purge Storage Tank Evacuation
F
Auxiliary Evacuation
G
Vacuum/Pressure Gage
H
Solution Pump Service
J
Refrigerant Pump Service
K
High-Stage Generator Service
Cooling Cycle Flow Circuits —
Figure 5 illustrates
the basic flow circuits of the 16DF absorption chiller during
the cooling cycle.
The liquid to be chilled is passed through the evaporator
tube bundle and is cooled by the evaporation of refrigerant
water sprayed over the outer surface of the tubes by the re-
circulating refrigerant pump. The refrigerant vapors are drawn
into the absorber section and are absorbed by the lithium
bromide-water solution sprayed over the absorber tubes. The
heat picked up from the chilled liquid is transferred from the
absorbed vapor to cooling water flowing through the ab-
sorber tubes.
The solution in the absorber becomes diluted as it absorbs
water, and loses its ability to continue the absorption. It is
then transferred by the solution pump to the generator sec-
tions to be reconcentrated. Approximately half of the weak
(diluted) solution goes to the high-stage generator where it
is heated directly by the combustion of gas or oil to boil out
the absorbed water. The mixture of reconcentrated solution
and vapor rises to the separator, where the vapor is released
and is then passed to the low-stage generator tubes. In the
low-stage generator, the rest of the weak solution is heated
by the high-temperature vapor from the high-stage separa-
tor, to boil out the remaining absorbed water.
The resulting water vapor from the low-stage generator
solution passes into the condenser section and condenses on
tubes containing cooling water. This is the same cooling wa-
ter which had just flowed through the absorber tubes. The
condensed high-temperature water from the low-stage gen-
erator tubes is also passed over the condenser tubes where it
is cooled to the condenser temperature. The combined con-
densed refrigerant liquid, from the 2 generators, now flows
back to the evaporator to begin a new refrigerant cycle.
The strong (reconcentrated) solution flows from the 2 gen-
erators back to the absorber spray headers to begin a new
solution cycle. On the way, it passes through solution heat
exchangers where heat is transferred from the hot, strong so-
lution to the cooler, weak solution being pumped to the gen-
erators. Solution to and from the high-stage generator passes
through both a high-temperature heat exchanger and a low-
temperature heat exchanger. Solution to and from the low-
stage generator passes through only the low-temperature heat
exchanger, mixed with the high-stage generator solution. This
heat transfer improves solution cycle efficiency by preheat-
ing the relatively cool, weak solution before it enters the gen-
erators, and precooling the hotter, strong solution before it
enters the absorber.
During high-load cooling operation, some abnormal con-
ditions can cause the lithium bromide concentration to in-
crease above normal. When this happens, a small amount of
refrigerant is transferred by an evaporator overflow pipe into
the absorber solution to limit the concentration. This is nec-
essary to keep the strong solution concentration away from
crystallization (see Solution Cycle and Equilibrium Dia-
gram section, page 9).
The evaporator refrigerant level is directly related to ma-
chine solution concentration. As the concentration increases
(has less water), so does the refrigerant level. As the solution
concentration increases beyond a safe limit, the refrigerant
level rises to the level of the overflow pipe and some spills
over to flow into the absorber. The concentration at which
the refrigerant overflows is determined by the amount of re-
frigerant (water) which is charged into the machine.
If, for some reason, the machine controls and evaporator
overflow do not prevent strong solution crystallization dur-
ing abnormal operating conditions, and flow blockage oc-
curs, the strong solution overflow pipe will reverse or limit
the crystallization until the cause can be corrected. The over-
flow pipe is located between the low-temperature gen-
erator discharge box and the absorber, bypassing the heat
exchangers.
If crystallization occurs, it generally takes place in the shell
side of the low-temperature heat exchanger, blocking the flow
of strong solution from the generators. The strong solution
then backs up in the discharge box and spills over into the
overflow pipe, which returns it directly to the absorber sump.
The solution pump then returns this hot solution through the
heat exchanger tubes, automatically heating and decrystal-
lizing the shell side.
Heating Cycle Flow Circuits —
Figure 6 illustrates
the basic flow circuits of the 16DF absorption chiller during
the heating cycle.
The liquid to be heated is passed through the evaporator
tube bundle and is heated by condensation of hot water va-
por from the high-stage generator. The solution flowing from
the absorber, through the heat exchangers to the generators
via the solution pump, and then back through the heat ex-
changers to the absorber sprays is basically the same as in
the cooling cycle. However, the solution is heated and re-
concentrated only in the high-stage generator. The heating
refrigerant water cycle is quite different from that of the cool-
ing cycle. The cooling water flow is turned off, as is the re-
frigerant recirculating pump. The high-temperature water vapor
from the high-stage generator is diverted to the evaporator,
and the condensed vapor in the evaporator is drained di-
rectly to the absorber solution.
6