Carrier 16DF013-050 User Manual
Page 39
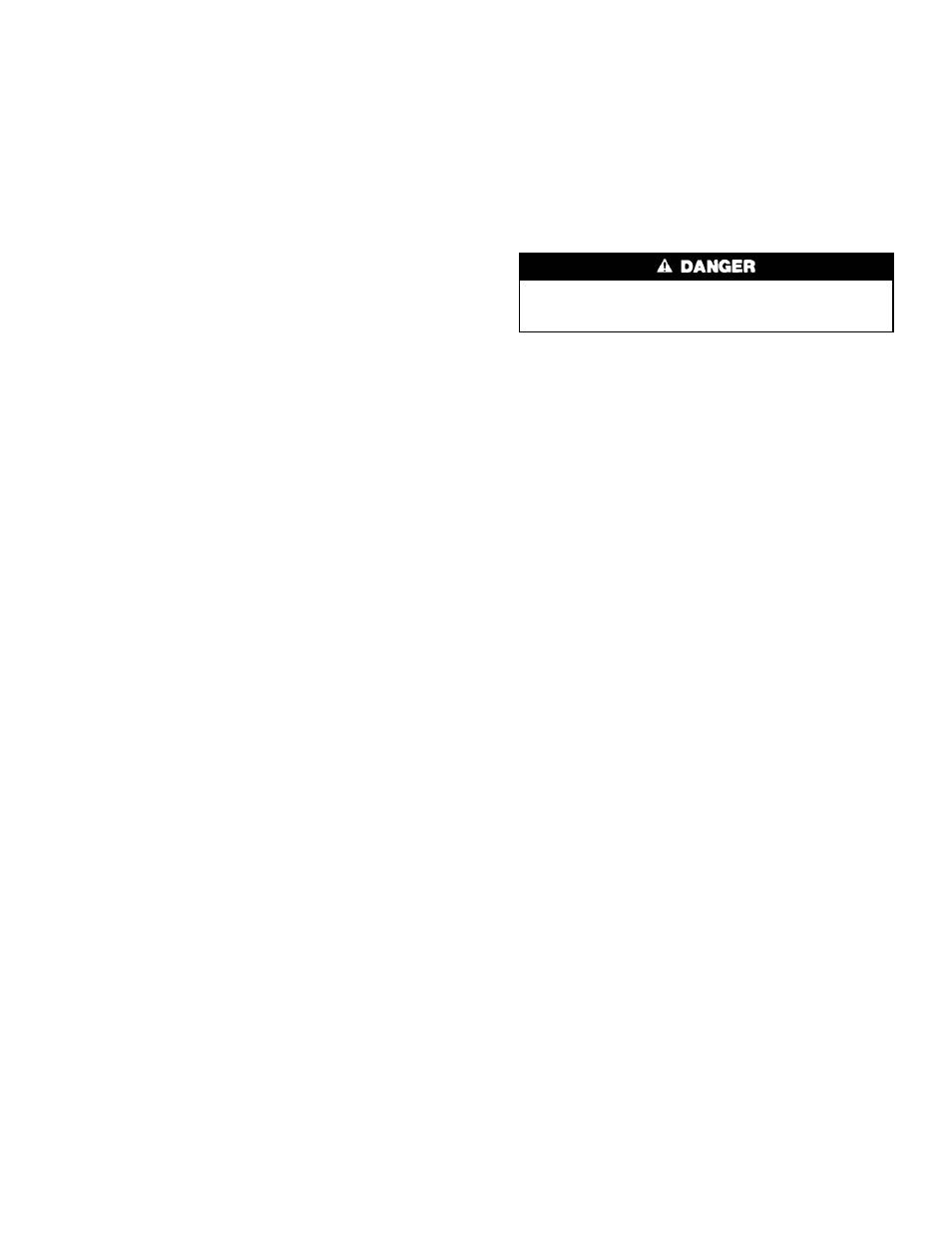
Operational Controls Check and Adjustment —
Functional check and adjustment of the machine controls is
to be done immediately after the solution and refrigerant have
been charged into the machine, and just before the initial
combustion heat-up period. If possible, the controls check
should be done on the cooling operation to verify the op-
eration of all controls and pumps.
PREPARATION
1. Supply control power to the machine control panel. Close
TS-1 control panel circuit switch and the control panel
circuit breakers. The status indicator on the front of the
control panel should display ‘‘000’’.
2. Verify that chilled/heating and cooling water circuits are
filled and operative, and that the pumps are powered. For
manual system operation, start the chilled/heating water
pump. With cooling operation, also start the cooling wa-
ter pump and cooling tower fan.
3. Place the machine control panel switches in the follow-
ing positions:
a. TS2 dilution valve at AUTO.;
b. TS3 select cool/heat switch on either, but preferably
on COOL;
c. TS5 capacity control switch at AUTO.; and,
d. TS6 operation switch at LOCAL.
4. Place the burner on/off switch in OFF until the machine
controls have been checked out.
5. Depress the Start button. For cooling, the status indicator
will display ‘‘CPO’’ and then ‘‘CPF’’ and all pumps should
start. For heating it will display ‘‘HPO’’ and only the so-
lution and heating water pumps will operate. The burner
should remain off at this time.
WATER PUMP STARTERS AND OVERLOADS
1. Starters for chilled/heating water and cooling water pump
motors should be checked individually according to the
manufacturer’s instructions. When the pump motor trips
out, the machine will shut down on the dilution cycle, the
alarm buzzer will sound, and the status indicator will dis-
play the ‘‘E02’’ fault code for the chilled/hot water pump
and ‘‘E03’’ for the condensing water pump (cooling only).
2. Depress the Stop button to silence the buzzer and reset
the machine control. Reset the overloads. Depress the Start
button to restart the machine.
HERMETIC PUMP ROTATION
1. Confirm that the solution and refrigerant pump starters
are energized and the pump motors are running.
2. Install a compound pressure gage on the refrigerant pump
service valve.
3. Open the valve and record the refrigerant pump dis-
charge pressure. Close the valve. Also notice any pump
sound. Depress the Stop button.
NOTE: The solution pump starter trip bar can be de-
pressed to bypass the shutdown dilution cycle.
4. Open the main disconnect switch (MCB1) and reverse
any 2 motor power leads on the secondary side of the
refrigerant pump starter.
5. Close the main disconnect switch and depress the Start
button to restart the machine and pumps.
6. Repeat Step 3. Compare the 2 discharge pressures. Use
the power lead arrangement that produced the higher dis-
charge pressure and least noise.
7. Repeat Steps 2 through 6 for the solution pump.
Initial Combustion —
Combustion must be started within
one day after the solution and refrigerant have been charged
into the machine. To establish the internal protective film,
the burner must be operated for several days at the maxi-
mum firing rate, as soon as the machine controls have been
checked out. It may be necessary to induce an artificial load
for the chilling/heating water, or to carefully raise the leav-
ing cooling water temperature if on cooling operation.
Start the burner while the machine is in operation, accord-
ing to start-up instructions in the separate burner manual.
The burner and fuel system should have been checked pre-
viously according to the Before Initial Start-Up instructions,
page 32. The firing rate control should be on MANUAL to
hold at the low fire position during the initial check. Use the
burner manual positioning switches instead of the chiller/
heater manual positioning switches for the initial burner tests.
Do not operate the burner if there is any fuel leakage, or
any known problems with the burner operating or safety
controls, or if the flame is unstable.
Generally, the initial burner start should include the
following:
1. Open only the pilot gas valve and place the burner switch
at ON to initiate the pilot flame. Using the flame safe-
guard control run/test switch, hold the sequence at ig-
nition trial to adjust the pilot, if necessary, and to verify
the flame signal.
NOTE: This switch also can be used to hold the se-
quence on pre-purge to make preliminary air damper link-
age adjustments.
2. With the manual main fuel valve closed, release the flame
safeguard to RUN. Safety shutdown and lockout will
occur and the Alarm light will illuminate because of main
flame failure. The machine control panel indicator will
display the ‘‘E08’’ fault. Depress the machine Stop but-
ton to silence the alarm.
3. Depress the safety reset switch on the flame safeguard
and the machine Start button to restart the chiller and
burner. Open the main fuel valve during the ignition pe-
riod. If the fuel line has not been completely purged of
air, it may take repeated attempts to establish the main
flame at low fire.
4. With the main flame held at low fire, measure the fuel
rate, verify the flame signal, and take flue gas samples
to check the fuel-to-air ratio.
5. Close the manual main fuel valve to verify flame failure
sensing response. Safety shutdown and lockout will oc-
cur and the Alarm light will illuminate. The machine
control panel indicator will display the ‘‘E09’’ fault. De-
press the machine Stop button to silence the alarm.
6. Depress the safety reset switch on the flame safeguard
and the machine Start button to restart the chiller and
burner. Open the manual main fuel valve.
7. Manually increase the firing rate in increments and re-
peat Step 4 at each increase until the high firing rate is
reached. Periodically check chilled/hot water tempera-
ture to be sure the burner heat input does not exceed the
chiller/heater load.
8. If adjustments to the modulating air damper of fuel valve
linkage or to the fuel pressure regulator(s) are neces-
sary, make gradual changes and repeat Steps 4 and 7
after each change.
9. Switch the firing rate to AUTO. on the burner control
panel, and use the machine control panel TS4 and TS5
capacity control switches to manually open and close
the burner fuel valve and damper in order to verify chiller/
heater control of the burner firing rate.
39