Carrier 16DF013-050 User Manual
Page 36
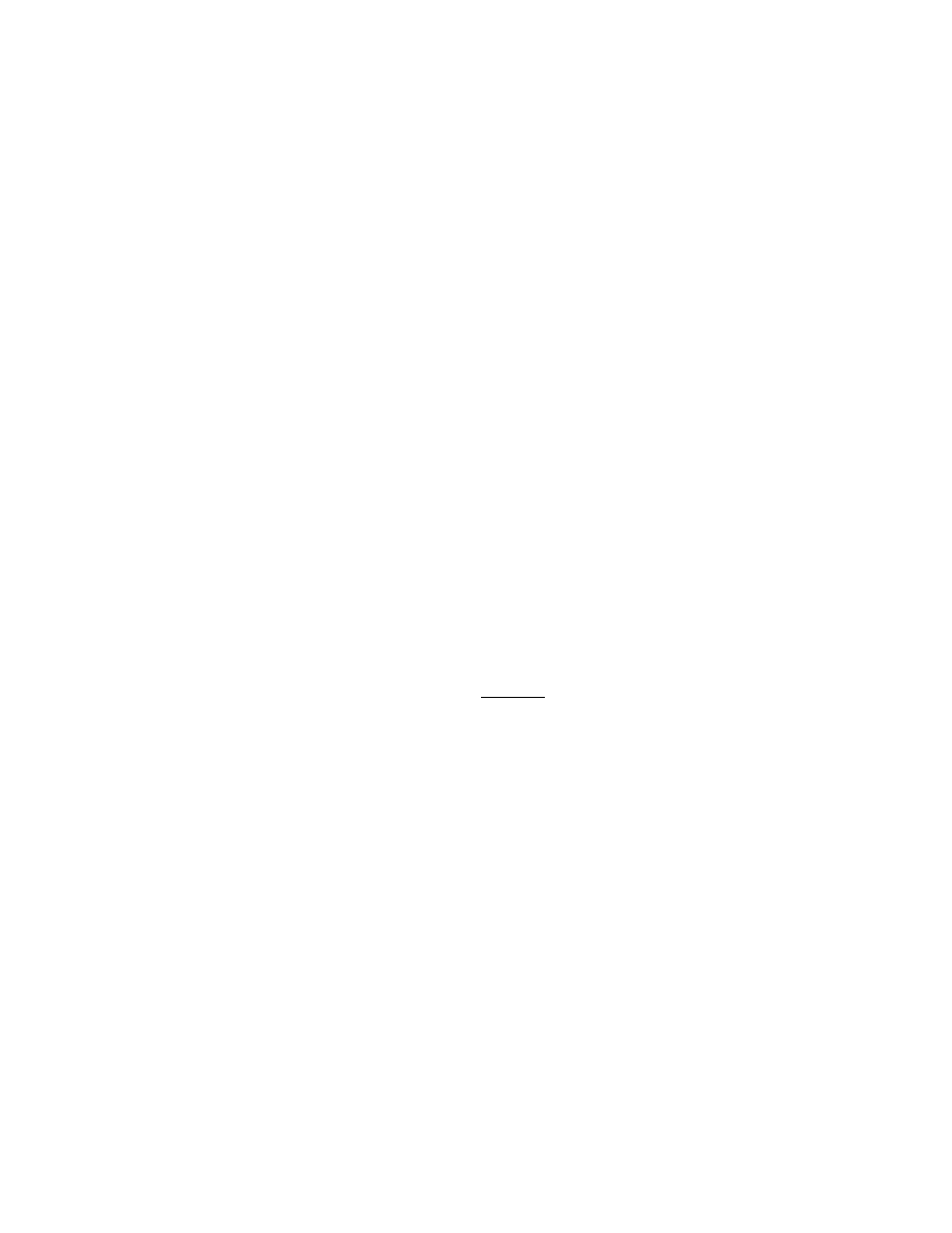
CHECK HIGH-STAGE GENERATOR TEMPERATURE
SWITCH — The switch is factory set to open on a rise in
temperature above 338 F (170 C) and close on a cooling be-
low 325 F (163 C). Verify the approximate scale position
setting (338 F [170 C]) and closed switch contacts. The switch
range is 122 to 608 F (50 to 320 C).
NOTE: The switch operation setting cannot be easily checked
in the field. It requires a precise scale adjustment, so do not
reposition if not necessary.
CHECK HIGH-STAGE GENERATOR PRESSURE SWITCH
— The switch is factory set to open on a rise in pressure
above -8 in. Hg (-20-mm Hg G) and close with a reduction
in pressure below -8 in. Hg (-205 mm Hg G). Verify the ap-
proximate scale position setting (-0.8 in. Hg [-20 mm Hg
G]) and closed switch contacts. The switch range is -20 in.
Hg (-500 mm Hg G) to 85 psig (6 kg/cm
2
).
NOTE: The switch operation setting cannot be easily checked
in the field without breaking machine vacuum. It requires a
precise scale adjustment so do not reposition if not
necessary.
RESTORATION
1. Place the control panel circuit breakers and dc power sup-
ply switch in the OFF position to deenergize the circuits.
Open and tag power supply disconnects to machine con-
trol panel.
2. Reconnect the wiring leads for the solution pump motor
and refrigerant pump motor according to the identifica-
tion markings applied during the test preparation.
3. Remove jumper wires from flow switch(es), high-
temperature generator low solution level electrode, and
fuel gas low-pressure switch.
4. Replace fuses in starters for chilled/hot water pump
motor, condensing water pump motor, and tower fan
motor.
Burner System —
Check the following combustion sys-
tem items against field piping and wiring drawings and the
burner manual instructions:
GENERAL
1. Burner is installed in accordance with applicable instal-
lation instructions.
2. Three-phase motor(s) have been properly wired and checked
for proper rotation.
3. Control wiring connections to the machine control center
have been completed and are accurate according to the
machine wiring diagrams.
4. All combustion controls and safeties have been properly
wired and are functional.
5. The exhaust stack and the boiler breeching connections
have been completed and they are open and unobstructed.
6. Provisions have been made to supply adequate combus-
tion air.
GAS FIRING
1. All gas train components have been installed and have
been properly selected, sized, and assembled. No Teflon
tape has been used on pipe threads (loose tape can cause
valve leakage and is a safety hazard).
2. Properly sized vent lines have been installed on all gas
train components that require venting. These include such
items as pressure regulators, normally open vent valves,
diaphragm valves, low and high gas pressure switches,
etc.
3. Piping and components have been leak tested and proven
gas tight, and the gas line has been purged.
4. The required gas pressure is available at the inlet to the
gas train.
OIL FIRING
1. The oil tank has been installed and filled with the correct
type of oil, and there is absolutely no water in the tank.
2. The oil supply and return lines have been properly sized
and installed to meet the maximum capacity of the pump,
and the system has been leak tested and purged. No
Teflon tape has been used on connection threads (loose
Teflon tape can cause valve leakage and is a safety
hazard).
Standing Vacuum Test —
Before machine is ener-
gized or placed in operation, check for air leaks with a stand-
ing vacuum test. Examine the test procedures described be-
low and select the one that applies to your job situation.
LONG INTERVAL TEST — Use this test procedure if an
absolute pressure reading has been recorded at least 4 weeks
previously and the reading was not more than 1 in. (25 mm)
of mercury.
1. Connect an absolute pressure gage to the absorber gage
valve and record the pressure reading. (Do not use mer-
cury gage.)
2. If the pressure has increased by more than 0.1 in. (2.5
mm) of mercury since the initial reading, an air leak is
indicated. Leak test the machine as described in the Main-
tenance Procedures section, page 46, then perform the short
interval test which follows.
SHORT INTERVAL TEST — use this test procedure if:
1. No previous absolute pressure readings have been re-
corded, OR
2. Previous absolute pressure reading was made less than 4
weeks ago, or reading indicated a machine pressure of
more than 1 in. (25 mm) of mercury, OR
3. Machine had to be leak tested after long interval test.
Procedure
1. Connect absolute pressure gage to absorber gage valve
and record pressure reading.
2. If the reading is more than 1 in. (25 mm) of mercury ab-
solute, evacuate the machine as described in the Main-
tenance Procedures, Machine Evacuation section, page 48.
3. Record the absolute pressure reading and the ambient tem-
perature.
4. Let machine stand for at least 24 hours.
5. Note the absolute pressure reading when ambient tem-
perature is within 15° F (8° C) of the ambient tempera-
ture recorded in Step 3.
6. If there is any noticeable increase in pressure, an air leak
is indicated. Leak test the machine as described in Main-
tenance Procedures section, page 46, then repeat short in-
terval vacuum test to ensure results.
Machine Evacuation —
When machine absolute pres-
sure is greater than 1 in. (25 mm) of mercury absolute, ma-
chine must be evacuated as described in Maintenance Pro-
cedures, Machine Evacuation section, page 48.
36