Inspect machine controls – Carrier 16DF013-050 User Manual
Page 34
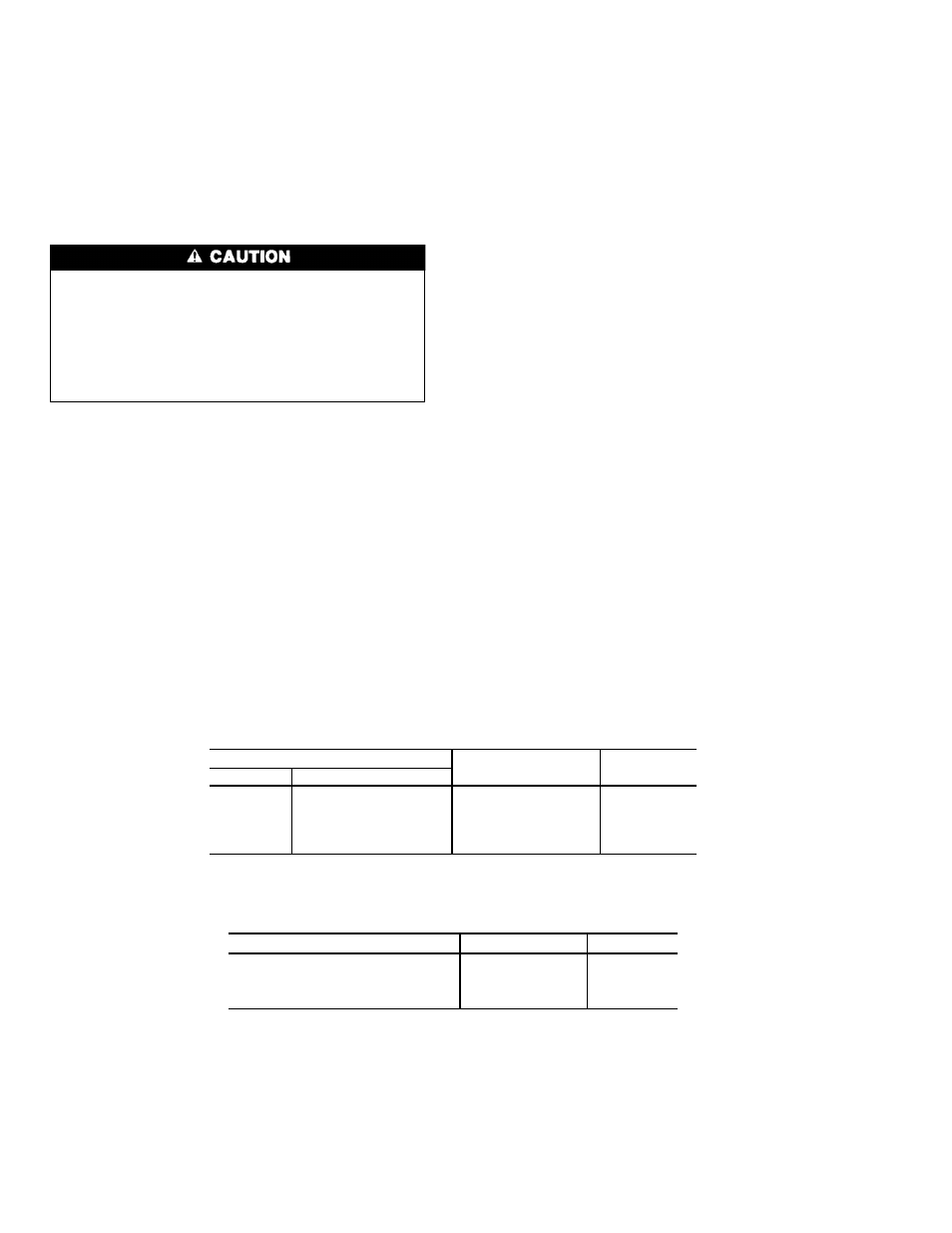
Inspect Machine Controls —
Visually inspect com-
ponents in machine and burner control panels, automatic valves
and positioners, and sensors for physical condition and se-
cure mounting. Also be sure all wiring connections are cor-
rect and tight. See Fig. 2-4 for machine component and sen-
sor locations, and Fig. 10 for control panel component
identification and location. See the manufacturer’s burner
manual for burner component locations.
The purpose of the following checkout procedure is to en-
sure that the controls have not been affected by shipping or
installation damage or altered in the process of making field
wiring connections.
The temperature and pressure limit controls have been
calibrated and precisely adjusted at the factory. Do not
attempt to readjust them unless they are not operating
properly.
Follow the checkout sequence in detail. It will be done
before the machine has been charged with solution and
refrigerant. The pump motors must not be powered at
this time.
Control circuit wiring and switch continuity and compo-
nent on/off status can be checked with a voltmeter while the
control circuit is energized, with the meter set up for
24 v dc.
PREPARATION
1. Open the control panel and place the circuit breakers and
dc power supply switch in the OFF position to deener-
gize the circuits.
2. Disconnect wiring leads for the solution pump motor and
refrigerant motor at the secondary side (motor side) of
the starter terminals. Mark each wire for proper identi-
fication at reinstallation, and wrap the ends of the dis-
connected wires with electrical tape.
3. Close all manual fuel valves, and disconnect oil pump
drive (if used).
4. Place temporary jumper wires at the switch terminals (not
at the control panel terminals) of limit controls which are
normally closed during operation, but would be open dur-
ing this pre-start test:
a. Chilled/hot water flow switch;
b. Cooling water flow switch, if used;
c. High-temperature generator low solution level elec-
trode; and,
d. Fuel gas low-pressure switch.
5. Remove fuses from starters for chilled/hot water pump
motor, condensing water pump motor, and tower fan mo-
tor so these motors will not operate during this check-out
test. Starters for these motors are field supplied and are
not located in the machine control panel.
CHECK COOLING CYCLE START
1. Place the control panel circuit breakers and dc power sup-
ply switches in the On position to energize the control
circuits. The status display on the front of the machine
control should read ‘‘000’’.
2. Place the switches on the inside of the machine control
panel door in the positions described in Table 11.
3. Place the burner control panel switches in the positions
described in Table 12.
4. Depress the Start button momentarily to start the control
circuit. The microprocessor will initiate the timed start-
ing and system checks sequence. As it progresses through
the sequential component start cycle, the control panel
status indicator will display ‘‘CPO’’, then ‘‘CPF’’ or ‘‘CPP’’.
The normal start sequence is explained in Typical Con-
trol Sequence, Machine Controls section, page 25.
If a system problem occurs, the fault category will be dis-
played on the control panel status indicator and the alarm
buzzer will sound. If so, note the fault code and depress
the Stop button momentarily to silence the buzzer and
reset the control system. The fault codes are listed in Ab-
normal Shutdown, Machine Controls section.
Table 11 — Cooling Cycle Start, Machine Control Panel Switch Positions
SWITCH
SELECTIONS
POSITION
Symbol
Name
TS-2
Dilution valve
Auto.-Manual
Auto.
TS-3
Select cool/heat
Cool-Heat
Cool
TS-4
Capacity control valve
Open-Neutral-Close
Neutral
TS-5
Capacity control valve
Auto.-Manual
Auto.
TS-6
Operation control
Local-Remote
Local
Table 12 — Cooling Cycle Start, Burner Control Panel Switches
SWITCH
SELECTIONS
POSITION
Operation control
On-Off
Off
Fuel selection (when appropriate)
Gas-Oil
Gas
Firing rate mode
Auto.-Manual
Auto.
Firing rate control
Open-Stop-Close
Stop
34