Carrier 16DF013-050 User Manual
Page 32
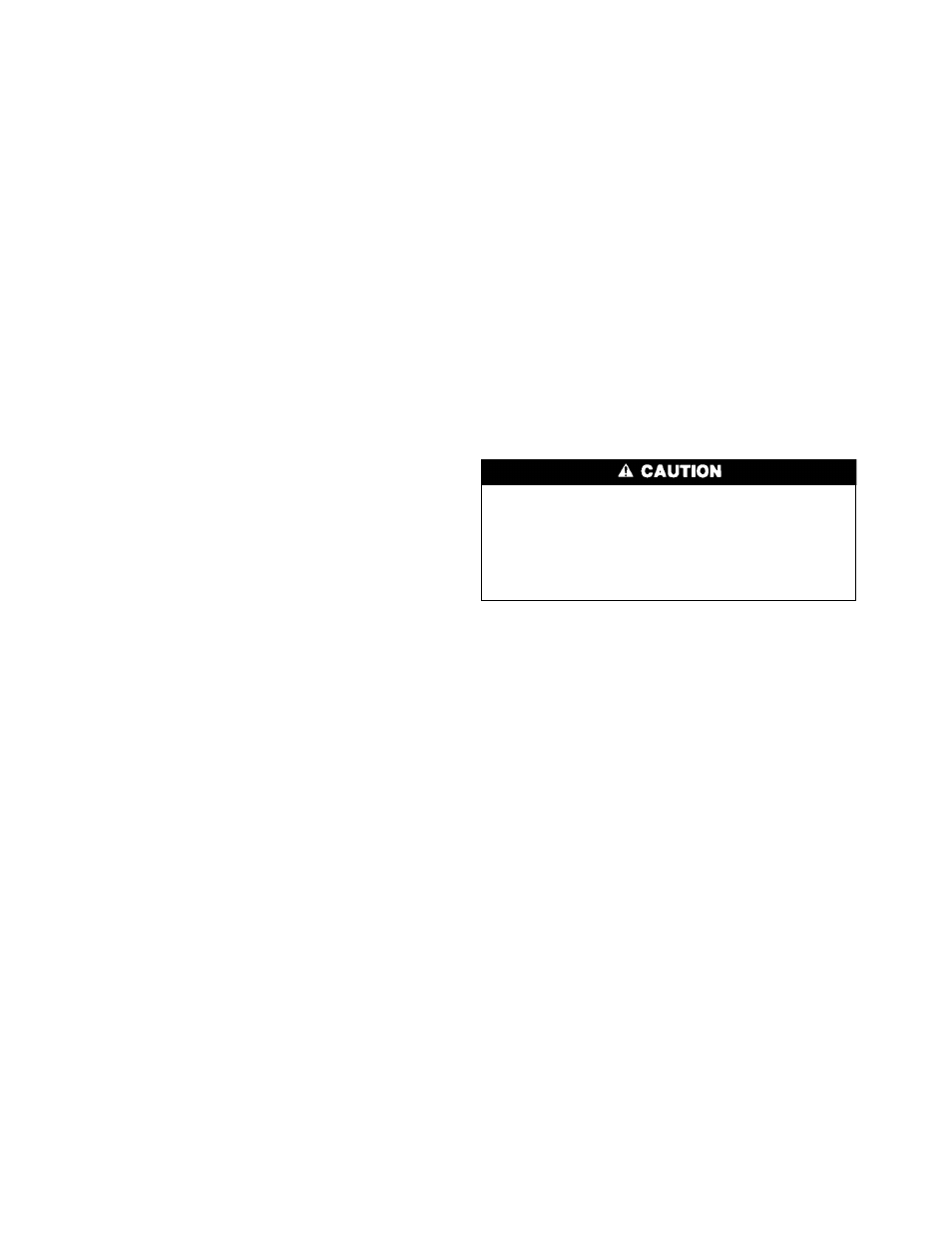
Burner Control —
The burner system has its own con-
trol panel and circuits for sequence control and combustion
supervision, but it operates under direction of the chiller/
heater control center for start/stop, firing rate, and low load
on/off instructions. The burner controls will vary some with
different sizes, fuels (single or dual fuel), and special codes.
See the separate burner manual for detailed control
information.
COMBUSTION CONTROL — Normal operation occurs with
the manual control switch ON, the firing rate selector switch
in AUTO., the fuel selector switch in the desired position,
and the appropriate manual fuel valves open.
The ignition sequence begins when the machine control
center closes the run relay contacts in the burner control cir-
cuit. The burner panel ‘‘Call For Heat’’ light illuminates and
the blower motor starts. The firing rate motor will drive to
the low fire position, and an interlock switch must close to
prove it is at the low fire position before the sequence will
continue.
When the airflow switch closes to prove combustion air
and the flame safeguard control in the burner control panel
has checked itself and the burner safety conditions, the safe-
guard control will begin a timed pre-purge period to be sure
any combustible gases are removed from the combustion
chamber.
At the end of pre-purge, the pilot gas valve and ignition
transformer are energized to establish the pilot ignition flame.
The ‘‘Ignition On’’ light will illuminate. If the pilot flame is
proven by the flame sensor, at the end of the pilot trial pe-
riod the ignition spark will be deenergized and the main fuel
valve(s) will be energized. The ‘‘Fuel On’’ lamp will light.
After a short trial for main flame, the pilot gas valve will be
deenergized to discontinue the pilot flame, and the ‘‘Ignition
On’’ lamp will be off. The firing rate positioning motor will
now be released from the low fire position for normal
operation.
If the flame sensor does not prove the continued presence
of flame at any time during the trials for pilot and main flame
or during normal operation, safety shutdown and lockout will
occur and the ‘‘Alarm’’ light will illuminate. Then, the safety
switch on the flame safeguard control must be manually pressed
for restart after the cause of failure has been corrected.
With a normal shutdown, the machine control center will
first send a control signal to drive the firing rate motor to the
low fire position before the flame is extinguished, but with
some safety shutdown conditions, the burner will be stopped
immediately. The burner will stop when the machine control
center opens the burner run relay contacts. The main fuel
valve(s) will be deenergized immediately. On smaller sizes
the blower is also stopped immediately, but on larger sizes,
it will remain in operation through a timed post-purge pe-
riod. The flame safeguard control will then remain in a standby
mode, waiting for a signal to restart.
FIRING RATE CONTROL — The burner firing rate is au-
tomatically adjusted to match the heat input with that re-
quired for the chilling or heating load. The burner will be at
or near the maximum firing rate at full load conditions, and
will be modulated to a reduced firing rate as the load de-
creases. The burner will be cycled off and on when the heat
required for the load is below the minimum firing rate.
The machine automatic capacity control provides signals
directly to the burner for firing rate positioning and low load
off/on cycling. The machine control center will override these
signals for start, stop, and special limit conditions, and the
burner itself will override for low fire ignition.
Manual rate positioning can be done with selector switches
in both the machine control center and the burner control
panel. However, automatic temperature limits will override
the chiller manual control if the selected heat input rate is
greater than that required for the load.
The modulated firing rate is provided by an air damper
and fuel valve which are positioned simultaneously through
adjustable control linkage with the firing rate positioning mo-
tor. The linkage connections for the damper and valve(s) are
adjusted to provide good fuel-to-air ratios for controlled, clean
combustion throughout the complete firing range.
BEFORE INITIAL START-UP
Do NOT charge the lithium bromide solution and re-
frigerant water into the machine during these prelimi-
nary checkout activities. The liquids MUST remain OUT
of the machine until just before it is initially started, when
the burner can be operated for a while at the full com-
bustion rate. This is essential to develop a corrosion-
resistant film on the internal steel surfaces.
Job Data and Tools Required
• job specifications and job sheets, including list of appli-
cable design temperatures and pressures
• machine assembly and field layout drawings
• controls and wiring drawings
• 16DF Installation Instructions and burner manual
• mechanic’s hand tools
• absolute pressure gage or water-filled wet-bulb vacuum in-
dicator graduated with 0.1-in. (2-mm) of mercury incre-
ments. Do not use manometer or gage containing mercury.
• auxiliary evacuation pump, 5 cfm (2.5 L/s) or greater, with
oil trap, flexible connecting hose, and connection fittings
• compound pressure gage, 30-in. vacuum to 30 psig
(75-cm vacuum to 200 kPa)
• digital volt-ohmmeter and clamp-on ammeter
• leak detector
32