Carrier 16DF013-050 User Manual
Page 46
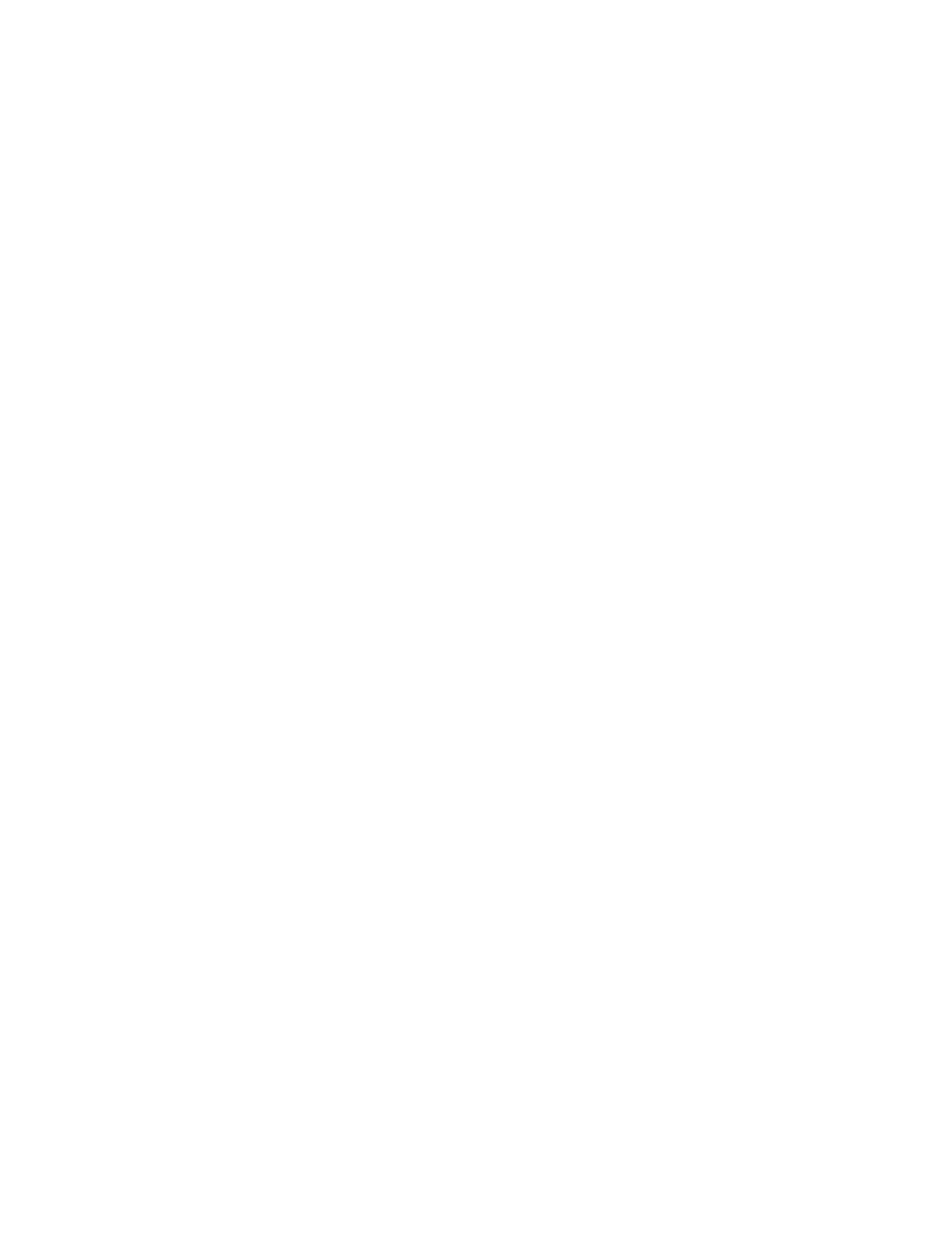
PERIODIC SCHEDULED MAINTENANCE
Normal preventive maintenance for 16DF absorption chiller/
heaters requires periodic, scheduled inspection and service.
Major items in the list below are detailed in the next section,
Maintenance Procedures.
Every Day of Operation
1. Log machine and system readings.
2. Observe burner flame for changes.
3. Check for fuel and water leakage, vibration, abnormal tem-
peratures, and unusual noise.
Every Month of Operation
1. Determine absorber loss (cooling only).
2. Check heating/cooling capacity control adjustment.
3. Check burner controls and linkage.
4. Check flame current and flue gas measurements.
Every 2 Months of Operation
1. Check low temperature cutout (cooling only).
2. Check dilution valve operation.
3. Check other limit and safety devices.
4. Clean flame detector and viewing windows as
necessary.
Every 6 Months of Operation or Cooling/Heating
Changeover
1. Check refrigerant charge (cooling only).
2. Check octyl alcohol (cooling only).
3. Exhaust purge.
4. Burner ignition test.
5. Have solution sample analyzed.
Every Year (At Changeover of Cooling/Heating
Cycle or Shutdown)
1. Check tubes for scale and fouling.
2. Check/adjust temperature sensors.
3. Perform flame failure and pilot turndown tests.
Every 2 Years
1. Replace valve diaphragms.
2. Replace high-temperature generator level electrodes.
3. Check/replace palladium heater.
4. Check/replace flame detector.
5. Check thermostats and pressure switches; replace as
necessary.
Every 5 Years or 20,000 Hours
(Whichever Is Shorter)
1. Inspect hermetic pumps.
2. Filter or regenerate the solution
3. Check control motors, and replace as necessary.
4. Check burner controls, fan, valves, operators, and re-
place as necessary.
5. Check the float valve in the high-temperature generator.
6. Check and repair (as necessary) burner and fire tube return-
end refractory.
7. Conduct nondestructive testing for all tubes, including fire
tubes.
8. Check and clean strainers in solution piping (size 16DF028
and larger).
9. Check cooling/heating changeover valve and replace parts
as necessary.
MAINTENANCE PROCEDURES
Log Sheets —
Readings of machine and system pressure-
temperature conditions should be recorded daily to aid the
operator in recognizing both normal and abnormal machine
conditions. The record also aids in planning a preventive main-
tenance schedule and in diagnosing machine problems. A typi-
cal log sheet is shown in Fig. 33.
Absorber Loss Determination —
Take absorber loss
readings when machine is operating with stable tempera-
tures. This is to be done only during cooling operation.
1. Make sure that there has been no refrigerant overflow for
at least 10 minutes before taking readings.
2. Fill thermometer wells on discharge lines of solution and
refrigerant pumps with oil or heat conductive compound
and insert thermometers.
3. Take refrigerant and solution samples (see Solution or Re-
frigerant Sampling, page 48), and determine the specific
gravity and temperature of each sample.
4. Using Fig. 30A and B, plot the intersection point of the
specific gravity and temperature of the solution sample.
Extend this point horizontally to the right and read the
saturation temperature.
Repeat with refrigerant sample, using Fig. 31A and B,
and reading to the left for saturation temperature. If it is
known that there is no lithium bromide in the refrigerant,
it is not necessary to take a refrigerant sample. In that
case, the refrigerant saturation temperature is the same as
the measured refrigerant pipe temperature.
5. Subtract the solution saturation temperature from the re-
frigerant saturation temperature. The difference is the ab-
sorber loss. Repeat the readings with a second sample to
verify steady state conditions. If the absorber loss is greater
than 5° F (2.8° C), machine evacuation is necessary be-
cause excessive noncondensables may interfere with nor-
mal operation before they can be removed by the purge
(see Machine Evacuation section, page 48).
For probable causes and suggested remedies for high
absorber
loss,
refer
to
the
Troubleshooting
Guide,
pages 54 - 56.
Machine Leak Test —
All joints welded at machine
installation must be leak tested before initial start-up of ma-
chine. Joints must also be leak tested after repair. If there is
any indication of air leakage, leak test the entire machine.
1. Be sure auxiliary evacuation valve, purge exhaust valve,
and all service valves are closed.
2. Break machine vacuum with dry nitrogen. Pressurize ma-
chine to 4 psig (0.3 KgF/cm
2
G) with tracer gas. Charge
the nitrogen and refrigerant through the auxiliary evacu-
ation valve.
3. Use dry nitrogen to raise machine pressure to 11.5 psig
(0.8 KgF/cm
2
G) Do not exceed 11.5 psig (0.8 KgF/
cm
2
G).
4. Leak test all joints with an electronic leak detector.
5. Correct all leaks; retest to ensure repair.
6. Release
machine
pressure,
and
perform
machine
evacuation.
46