Carrier 16DF013-050 User Manual
Page 54
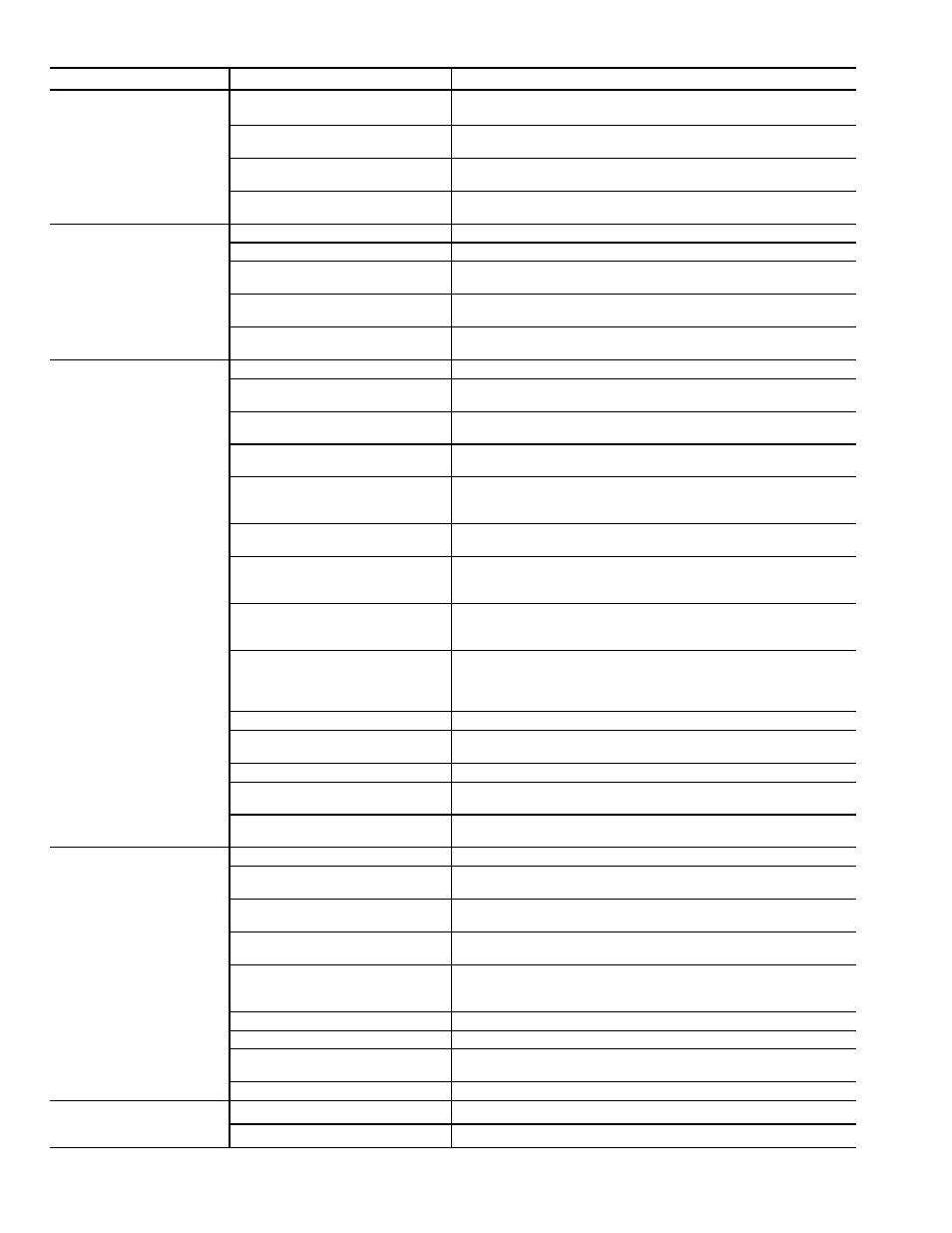
TROUBLESHOOTING GUIDE
PROBLEM/SYMPTOM
PROBABLE CAUSE
REMEDY
Machine will not run
when Start button is
depressed
No power to control panel
(no status display)
Check for building power failure. Check main circuit breaker.
Control circuit power switches
open (no status display)
Close TS1 control circuit switch and main circuit breakers in
control panel.
Control panel fuse blown
(no status display)
Check circuits for ground or short. Replace fuse.
Run interlock or safety switch
open (safety code displayed)
Correct cause of problem (see Causes and Remedies under
Abnormal Stop section). Depress Stop then Start buttons.
Burner misfire on pilot
or main flame ignition
attempt
(‘‘EO8’’ fault code)
Manual fuel valve closed
Open the valve.
Abnormal supply gas pressure
Check fuel supply and pressure regulator.
Loose linkage to air damper
or fuel valve
See burner manual for adjustment instructions.
Insufficient combustion air to
equipment room
Open air supply to equipment room.
Burner malfunction
(various causes)
See burner manual for correction instructions.
Leaving chilled water
temperature too high
(machine running)
Set point too high
Reset on capacity control.
Excessive cooling load
(machine at capacity)
Check for cause of excessive load.
Excessive chilled water flow
(above design)
Take accurate flow check and reset flow.
Low condensing water flow
(below design)
Take accurate flow check and reset flow.
High supply condensing
water temperature
(above design)
Check cooling tower operation and temperature controls.
Fouled water tubes
(poor heat transfer)
Clean tubes. Determine if water treatment is needed.
Fouled generator tubes
(poor heat transfer with high
stack temperature)
Clean tubes. Check air supply. Adjust burner if necessary.
Machine needs octyl
alcohol addition
Check solution sample and add octyl alcohol if necessary (see
Maintenance Procedures, Adding Octyl Alcohol section,
page 49).
Noncondensables in machine
Check absorber loss (see Absorber Loss Determination
section, page 46).
If above 5° F (2.8° C), see Causes and Remedies under
Inadequate Purging.
Capacity control malfunction
Check calibration and operation of capacity controls.
Burner capacity controls
not fully open
Place machine and burner Auto.-Manual switches in AUTO.
position.
Low burner firing rate
Adjust burner controls.
Solution crystallization
(solution flow blockage)
See Causes and Remedies under Solution Crystallization.
Excessive refrigerant overflow
Check refrigerant charge (see Maintenance Procedures,
Refrigerant Charge Adjustment section, page 49).
Leaving hot water
temperature too low
(machine running)
Set point too low
Reset on capacity control.
Excessive heating load
(machine at capacity)
Check for cause of excessive load.
Excessive hot water flow
(above design)
Take accurate flow check and reset flow.
Fouled hot water tubes
(poor heat transfer)
Clean tubes. Determine if water treatment is needed.
Fouled generator tubes
(poor heat transfer with high
stack temperature)
Clean tubes. Check air supply. Adjust burner if necessary.
Noncondensables in machine
See Causes and Remedies under Inadequate Purging.
Capacity control malfunction
Check calibration and operation of capacity controls.
Burner capacity controls
not fully open
Place machine and burner Auto.-Manual switches in AUTO.
position.
Low burner firing rate
Adjust burner controls.
Leaving chilled water
temperature too low
(machine running)
Set point too low
Reset on capacity control.
Capacity control malfunction
Check calibration and operation of capacity controls.
54