Carrier 16DF013-050 User Manual
Page 55
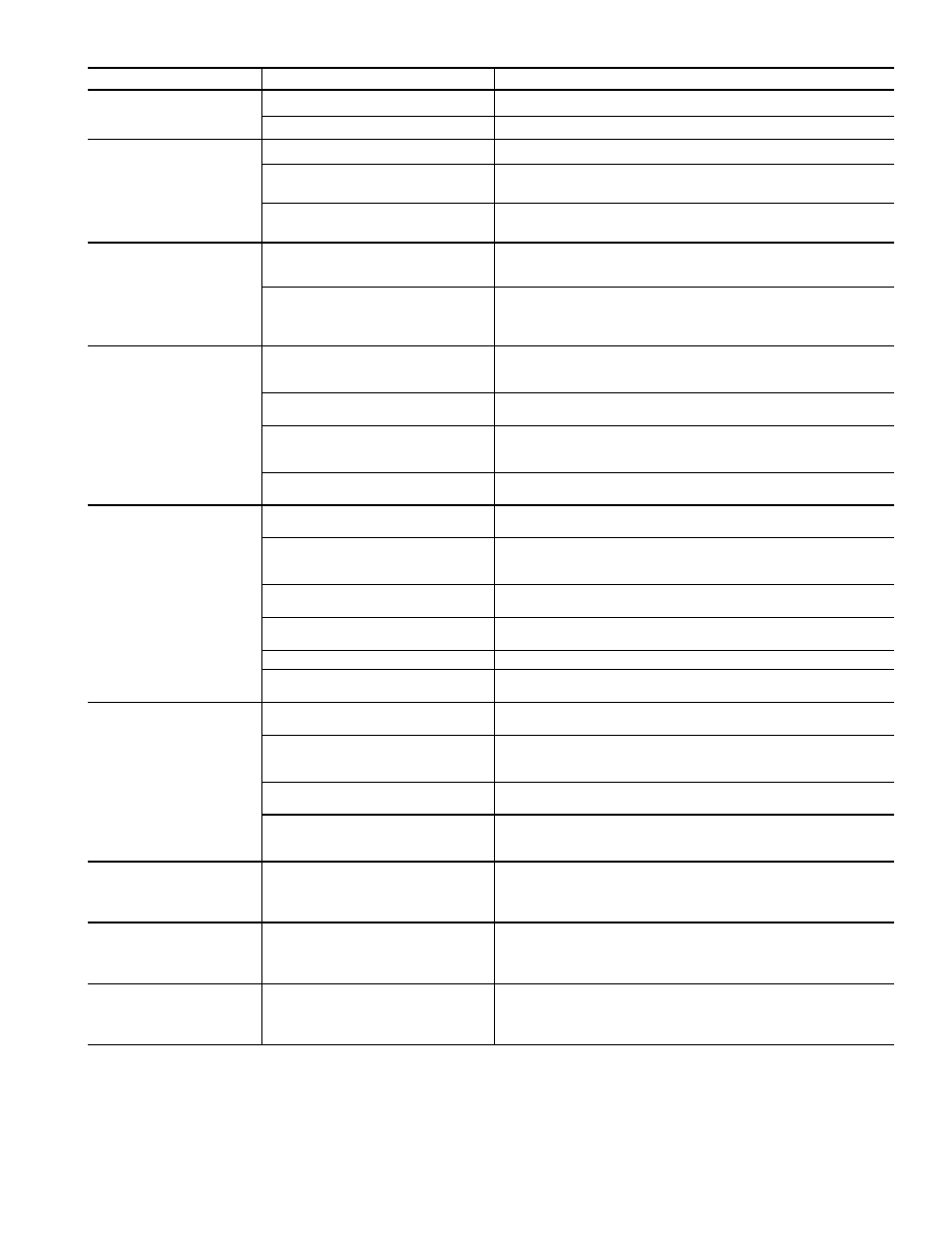
TROUBLESHOOTING GUIDE (cont)
PROBLEM/SYMPTOM
PROBABLE CAUSE
REMEDY
Leaving hot water
temperature too high
(machine running)
Set point too high
Reset on capacity control.
Capacity control malfunction
Check calibration and operation of capacity controls.
Leaving chilled water
temperature fluctuates
(machine running,
capacity control
hunting). Burner and
temperature cycling at
low load is normal.
Chilled water flow or load cycling
Check load stability and system controls.
Capacity control malfunction
Check calibration and operation of capacity controls and
position of sensor in well.
Condensing water flow or
temperature cycling
Check condensing water temperature control and cooling tower
operation.
Leaving hot water
temperature fluctuates
(machine running,
capacity control
hunting). Burner and
temperature cycling at
low load is normal.
Hot water flow or load cycling
Check load stability and system controls.
Capacity control malfunction
Check calibration and operation of capacity controls, and
position of sensor in well.
Excessive refrigerant
overflow to absorber
during cooling cycle
Noncondensables in absorber
Check absorber loss (see Maintenance Procedures, Ab-
sorber Loss Determination section, page 46). See Causes and
Remedies under Inadequate Purging.
Fouled water tubes
(poor heat transfer)
Clean tubes.
Machine needs octyl alcohol
Check solution sample and add octyl alcohol if necessary (see
Maintenance Procedures, Adding Octyl Alcohol section,
page 49).
Excessive refrigerant
charge in machine
Adjust refrigerant charge (see Maintenance Procedures,
Refrigerant Charge Adjustment section, page 49).
Inadequate purging
(low machine capacity
and high absorber loss
on cooling)
Air leakage in vacuum
side of machine
Leak test and repair if necessary (see Maintenance Proce-
dures, Machine Leak Test section, page 46).
Inhibitor depleted
Have solution analyzed. Add inhibitor and adjust alkalinity if
necessary (see Maintenance Procedures, Solution Analysis
and Inhibitor sections, page 49).
Purge valves not positioned
correctly
Check valve positions (see Maintenance Procedures, Ma-
chine Description, Purge section, page 13).
Palladium cell not heated
or functioning
Check line voltage power supply to cell and cell operation.
Purge storage chamber full
Use vacuum pump to evacuate storage chamber.
Purge solution supply lines
crystallized
Heat solution supply lines (see Maintenance Procedures,
Solution Decrystallization section, page 53).
Strong solution crys-
tallization during
operation (strong
solution overflow
pipe hot)
Refrigerant not overflowing
to limit solution concentration
Check refrigerant charge (see Maintenance Procedures,
Refrigerant Charge Adjustment section, page 49).
Noncondensables in absorber
Check absorber loss (see Maintenance Procedures,
Absorber Loss Determination section, page 46). See Causes
and Remedies under Inadequate Purging.
Fouled water tubes
(poor heat transfer)
Clean tubes.
Machine needs octyl alcohol
Check solution sample and add octyl alcohol if necessary (see
Maintenance Procedures, Adding Octyl Alcohol section,
page 49).
Solution crystallized
during shutdown
(solution crystalliza-
tion symptoms)
Insufficient solution dilution
at shutdown (either power
failure or dilution cycle fault)
Verify that the dilution valve opens and solution pump con-
tinues to operate for at least a 15-minute dilution period.
Abnormal solution
pump noise (some
noise in the solution
piping is normal)
Pump cavitation due to
low solution level
Hold dilution valve Auto.-Manual switch at MANUAL for 3 min-
utes to raise solution level. If it continues, may be caused by
crystallization or low solution charge.
Abnormal refrigerant
pump noise
Pump cavitation due to
low refrigerant level from
cooling water temperature being
too low at low load
Maintain cooling water temperature no lower than 59 F
(15 C). Stop machine for about 20 minutes to recover, then
restart.
55