Simulation-based sequencing – Rockwell Automation FactoryTalk Scheduler Users Guide User Manual
Page 50
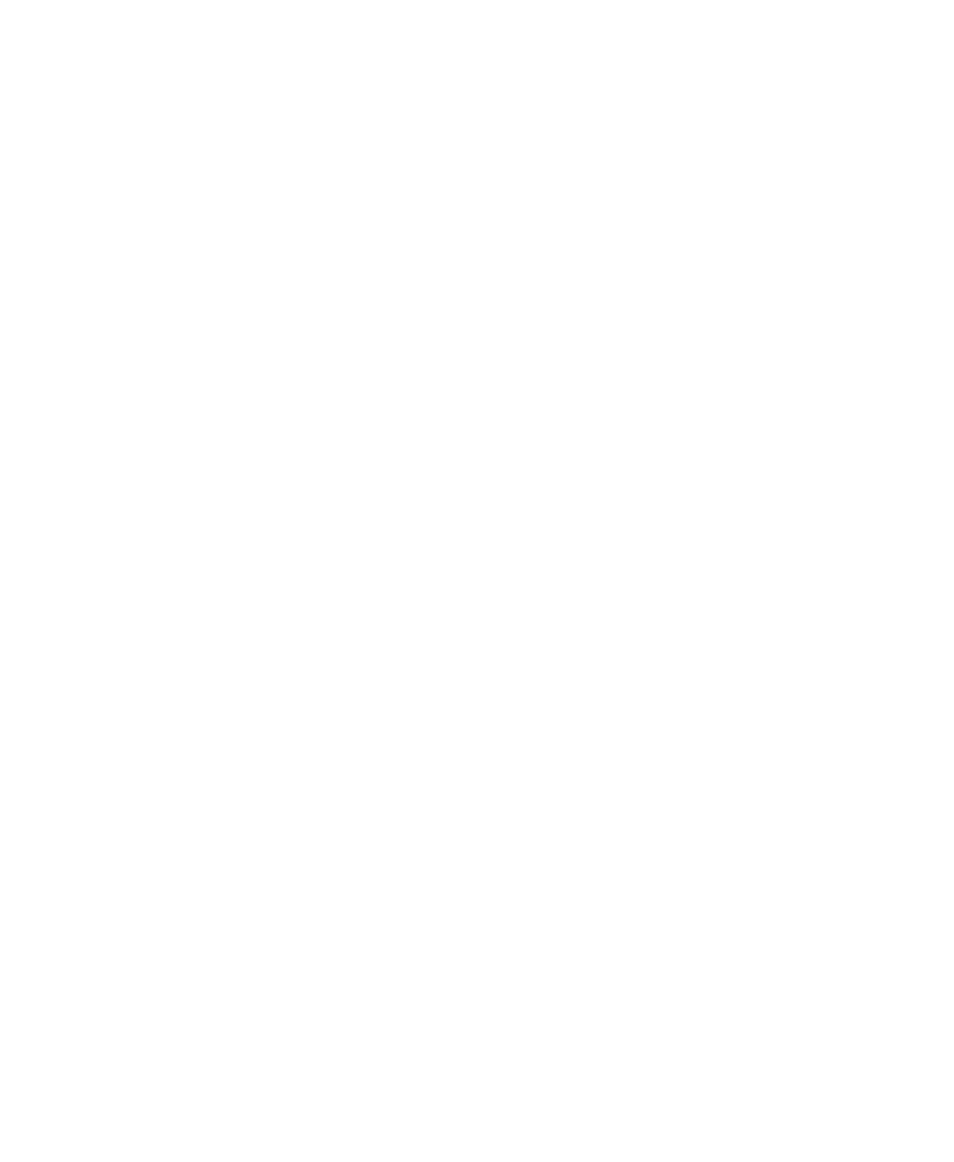
F
ACTORY
T
ALK
S
CHEDULER
U
SER
’
S
G
UIDE
44
• •
•
•
•
as an available ranking order property. FactoryTalk Scheduler will automatically list
all specified order properties.
Priority: Ranking based on the smallest numeric priority. If you use this rule, a
priority field must be included in the order database.
Process Time: Ranking based on the sum of the job’s operation times, the smallest
sum being ranked first.
Release Date: Ranking based on the earliest job release (or early start) date first.
Reverse Priority: Ranking based on the largest numeric priority. If you use this rule, a
priority field must be included in the order database.
Slack Time: Ranking based on the smallest total job slack time.
User Rule: Ranking based on a custom-written user rule. Multiple user rules can be
added with the name of each display on a secondary selection list.
Simulation-based sequencing
Simulation-based sequencing provides an attractive alternative to algorithmic
sequencing by providing a simple, yet very flexible method for constructing a schedule. In
general, any schedule that is produced by an algorithmic sequencer can also be produced
by a simulation-based sequencer. A simulation-based sequencer, however, can also
consider many schedules that cannot be considered by an algorithmic sequencer.
In contrast to the algorithmic sequencer, the simulation-based sequencer selects and loads
an operation-at-a-time. By loading individual operations rather than entire jobs, the
simulation-based sequencer has finer control over the way the operations are loaded onto
the planning board. This operation-at-a-time loading is the key to the added flexibility in
schedule generation using the simulation-based sequencer.
A second fundamental difference between the algorithmic and simulation-based
sequencer is that the simulation-based sequencer constructs the schedule in a single time
pass by moving forward from one event time to the next. The simulation-based sequencer
begins at the current time and loads all operations that can start now. Note that these
operations do not come from a single job as in the case of the job-at-a-time sequencer, but
can be taken from the entire set of jobs. Once all operations are loaded that can start at this
event time, the simulation-based sequencer advances time to the next event—e.g., the first
completion time for any operation on the planning board. In this case, a busy resource has
just changed to idle; hence, the simulation-based sequencer attempts to load additional
operations at this new event time. The simulation-based sequencer continues in this
fashion, advancing time forward to the next event time and loading additional operations
as resources become idle, until all operations have been loaded.