Rockwell Automation FactoryTalk Scheduler Users Guide User Manual
Page 106
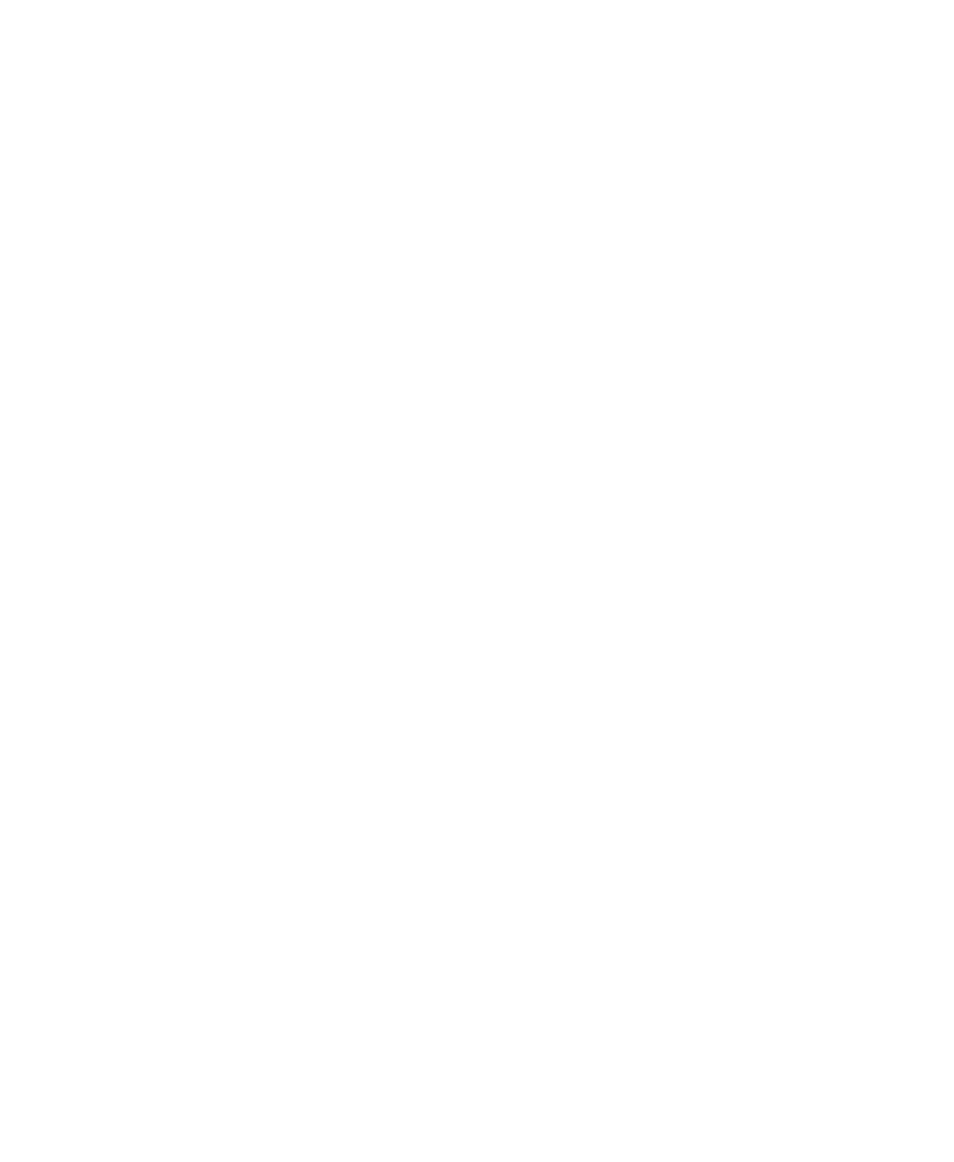
F
ACTORY
T
ALK
S
CHEDULER
U
SER
’
S
G
UIDE
100
• •
•
•
•
Operation Constraint—a restriction placed on the duration, start, or end time of an
operation. Operation constraints include Maximum Span, which limits the maximum
operation duration, and Minimum End Offset, which limits the offset time between the
end of the previous operation and the start of this operation.
Operation Parameter—a named value associated with a manufacturing operation.
Operation parameters may be used to determine the phase times of an operation or
referenced by lot selection logic to decide which lot to process next. The operation
parameter values of a production lot may be defined at the order, product, or job
segment data levels.
Operation Phase Times—the times assigned to each phase of an operation. Each phase
time has both a Deterministic Plan Time and a Random Simulation Time. The
Deterministic Plan Time is used by FactoryTalk Scheduler to generate a deterministic
schedule for the facility.
Operation Phases—the individual phases that make up an operation. These phases
include setup, processing, and teardown. Each phase has its own duration and can
have specific resource and material actions.
Operation Planned Station—a parameter of an operation that defines the next station in
the process plan for this order. If parallel operations follow this operation, then this
parameter returns the first of these stations.
Operation Priority—a parameter of a manufacturing order or operation. The priority can
be used in lot selection logic to decide which lot to process next. The value of this
parameter is always defined at the order level, but may also be redefined at the job
data segment level.
Operation Sequence Number—a number assigned to each operation that may be used to
establish the order and sequence of operations. A sequence number is made up of a
base number, with one or more sub-thread numbers appended following a dot (.). For
example, 30.1.5 has a base sequence number of 30, sub-thread of 1, and second level
sub-thread of 5.
Order Due Date—a parameter of a manufacturing order that establishes the date/time
when the order is due. The value of this parameter is defined at the order level.
Order Earliest Start Date—a parameter of a manufacturing order that establishes the
earliest date/time when the order can start its first operation. The value of this
parameter is defined at the order level.
Pegging—the process within MRP of associating with a given item the sources of its
gross requirements and/or allocations. Soft pegging is a temporary association that
may be changed when rescheduling occurs. Hard pegging is a permanent association
that cannot be changed by rescheduling.