Operation – MacDon 873 Combine Adapter User Manual
Page 23
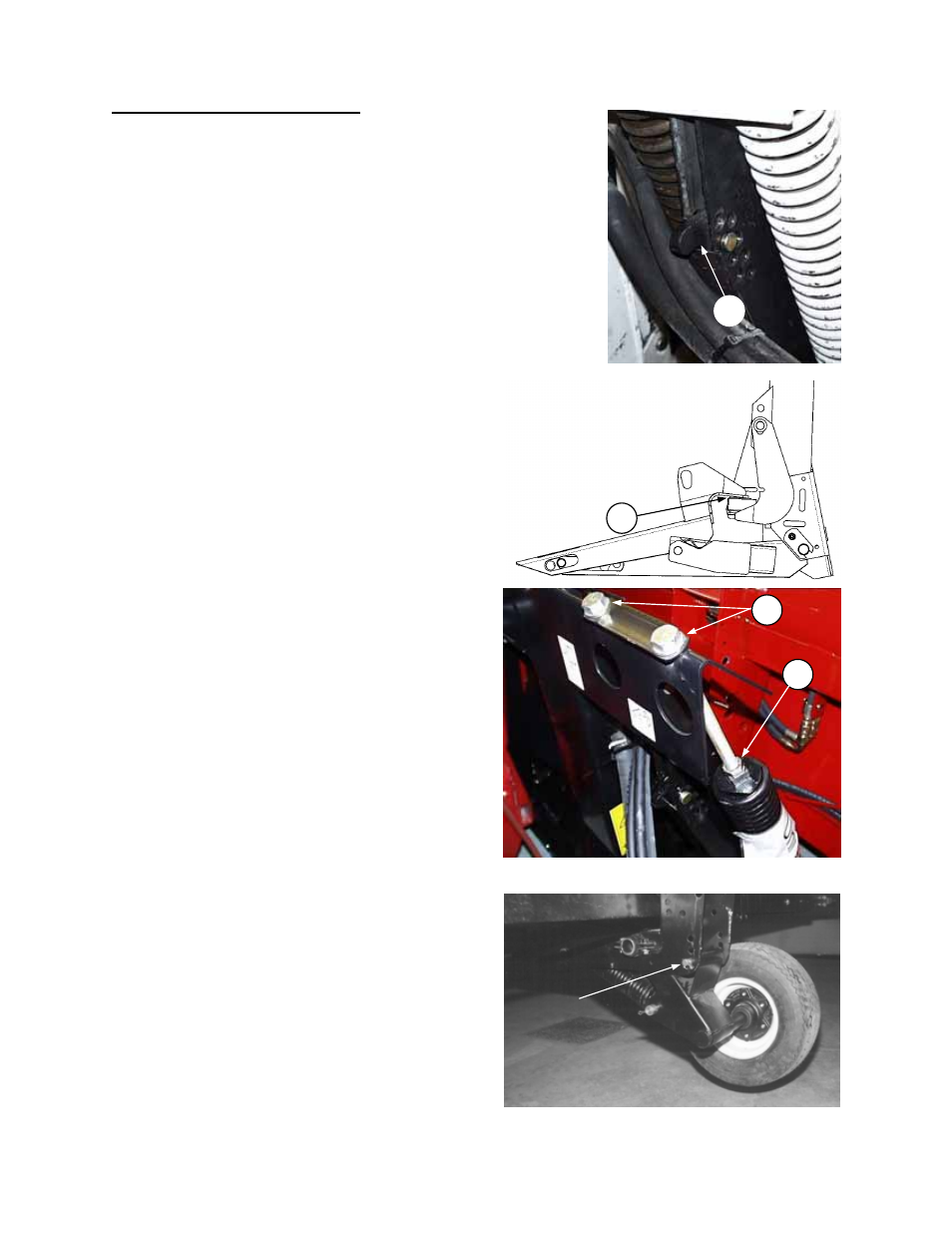
Form # 147069
Issue 09/06
21
OPERATION
963/972/973 HEADER FLOTATION (continued)
Header Floatation for 972/973 Headers with Gauge
Wheel/Transport Wheel:
1. Set guard angle and reel to desired position for cutting conditions
and slide handle (A) down to engage float.
2. Lower header to remove the pins from the gauge wheels
3. Position the header at the desired cutting height (without gauge
wheel pins in).
At this position inspect the gap at (B) to ensure that
the gauge wheel springs are not pushing the header
off the float down-stop pads. If gap at (B) is between
0 to 1/2 inch (0 to 13 mm) proceed to step 4.
If gap at (B) is larger than 1/2 inch, lift up on crop
divider to check the header’s floatation. If float is
lighter than 100 lbs (445 N) continue on with setting
procedure, if not check to see how many coil springs
are installed in the gauge wheels. If two springs are
installed remove one spring from each side and
repeat step 3.
4. Adjust float to desired setting [recommended 80
to 100lbs (355 to 445N) while keeping 0 to 1/2
inch (0 to13 mm) gap at (B). Measure gap with
header at desired cutting height.
Loosen jam nuts (D) and turn adjustment bolts (C)
clockwise to increase float.
Loosen jam nuts (D) and turn adjustment bolts (C)
counterclockwise to decrease float.
5. With header at cutting height, inspect position of
gauge wheel retaining slot. Insert pin into the hole
that is most centered in the slot.
Transport package uses a different bracket however,
there is still a slotted hole to place the pin through.
Utilize the same steps to set the height.
NOTE: If slot is positioned above the top hole, place
the wheels into storage position and lower skid
shoes to cut in the close proximity to the ground.
Refer to Floatation Setting section.
NOTE: Settings may require re-adjustment after an
adjustment to header angle or reel position.
ADAPTER FLOAT ENGAGED
A
B
FLOAT ADJUSTMENT
D
C