3 loop tuning procedure – INFICON SQM-242 Thin Film Deposition Controller Card Operating Manual User Manual
Page 84
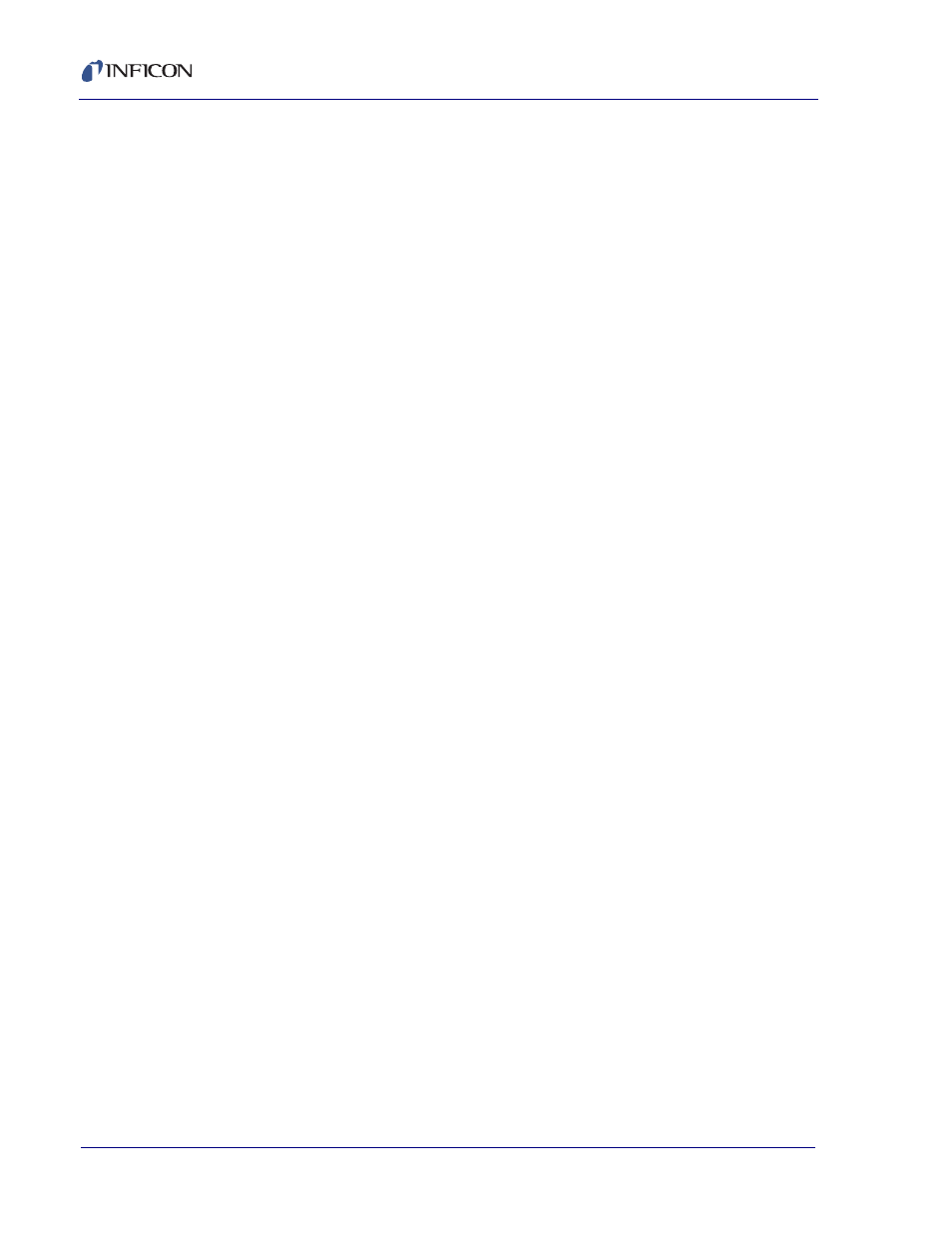
8 - 8
IP
N 07
4-
54
9-
P1
A
SQM-242 Operating Manual
8.5.3 Loop Tuning Procedure
NOTE: Please keep in mind, control loop tuning is a trial and error process and
there is no "best" procedure to accomplish this task.
1
Set System Parameters: In the SQM-242 Co-dep software, set a Period of
0.25 seconds as a good starting point. Set Tooling parameters to 100% for now.
Initially set the Rate Filter to 1.00 (no filter) to see the noise of the system.
Simulate should be OFF. Keep in mind that Simulate mode is a tool for testing
process layers. It is not likely to match the control response of your vacuum
system.
2
Create a One-Layer Test Process: In View >> Input setup, input the Z-Ratio
and density of the material you are depositing. On the main dialog box, set the
desired rate and leave the other parameters at their default values.
3
Test the Setup: Set the power to manual mode, then press Start. Slowly
increase the power to 10%, and verify that your power supply output is about
10% of full scale. Continue to increase power until a rate near your desired rate
is achieved. Again, verify that the power supply output agrees with the
SQM-242 Power (%) reading. If the readings don’t agree, check your wiring and
verify that the Edit>>Output menu, Full Scale voltage agrees with your power
supply’s input specifications. Log the data for a few minutes. Plot the data, if the
system has significant short term noise at a fixed power (maybe >10%), the
control loop will be very difficult to adjust, especially at low rates. It is better to
eliminate the source of the noise before attempting to set the PID values.
4
Select a Filter Alpha: On the View >> Card Setup menu, slowly decrease the
filter Alpha from 1to a lower value until the rate display noise is minimized. If
you set Alpha too low, the display will lag the true system response and may
hide significant problems. A value of 0.5 equally weights the current reading
and the previous filtered readings.
5
Determine Open Loop Gain: Record the Power reading at the desired rate as
PWR
DR
. Slowly lower the power until the Rate (Å/s) reading is just at (or near)
zero. Record the zero rate Power reading as PWR
0R
.
6
Determine Open Loop Response Time: Calculate 1/3 of your desired rate
(RATE
1/3
), and 2/3 of the desired rate (RATE
2/3
) for this layer. Slowly increase
the power until Rate (Å/s) matches RATE
1/3
. Get ready to record the loop’s
response to an input change. Quickly adjust Power (%) to PWR
DR
. Measure the
time for the Rate (Å/s) reading to reach RATE
2/3
. You may want to do this
several times to get an average response time. Twice the measured time is the
step response time, TIME
SR
. TIME
SR
is typically 0.2 to 1 second for E-Beam
evaporation, 5 to 20 seconds for thermal evaporation.
7
Set PID Values: Set the power to zero. In the Edit>>Output menu set P=25,
I= TIME
SR
, D=0. Set Max. Pwr to ~20% higher than PWR
DR
. Exit the output
menu and select Auto to move to Auto (PID control) mode and observe the
Power graph. The power should rise from 0%, and stabilize near PWR
DR
with