4 hourmeter, 5 coolant temperature sender, Hourmeter – JLG G5-18A Service Manual User Manual
Page 144: Coolant temperature sender
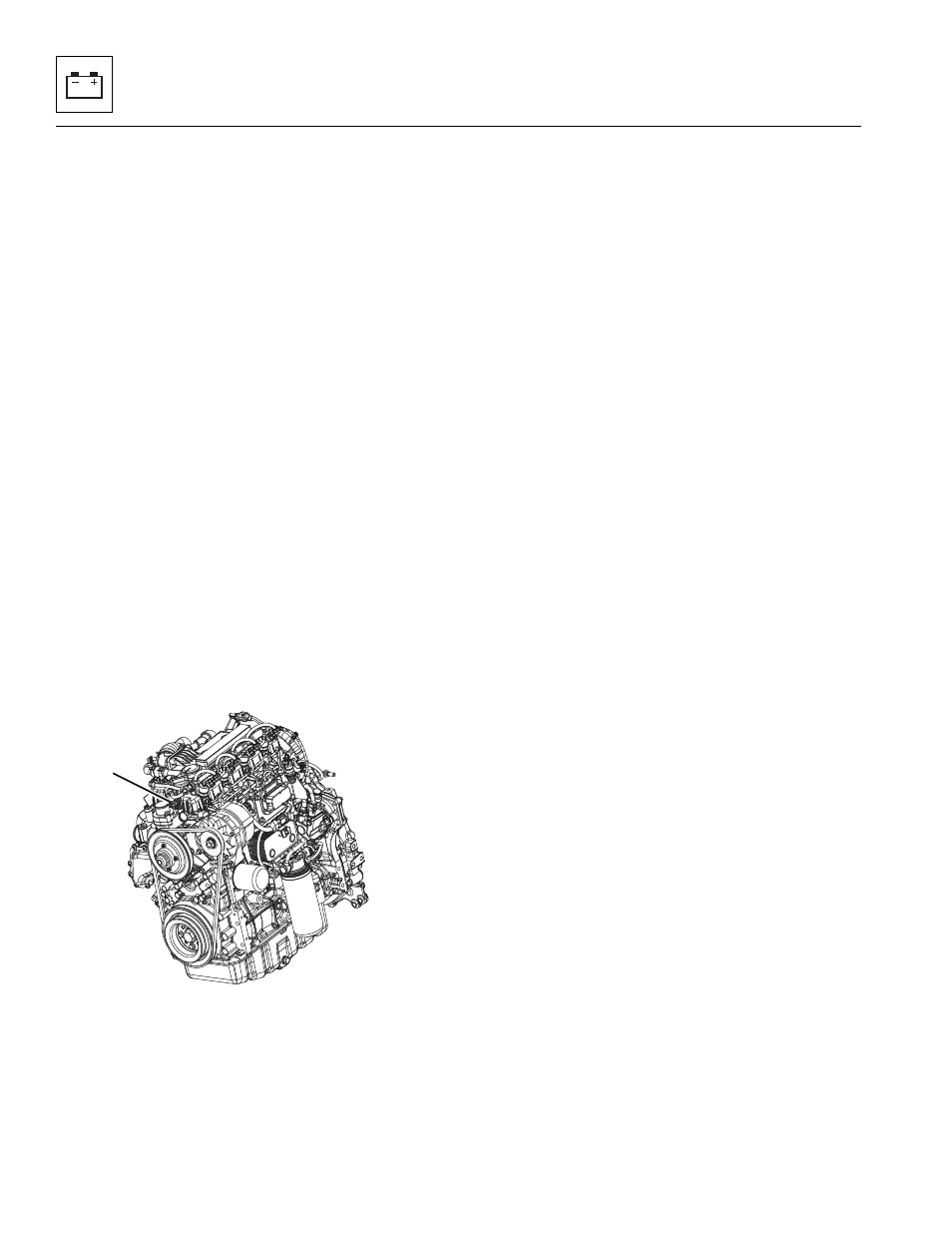
Electrical System
9-24
G5-18A, 2505H, 25.5
5. Check that the ignition terminal has current and that
the fuse in the fuse panel is not blown.
6. Check for broken, shorted, frayed, disconnected or
damaged wiring between the fuel level indicator
wiring at the cab, fuse and relay panel, ignition key
switch and from the fuel level sender on the fuel tank
through the wiring in the cab.
7. Check the fuel level sender. The resistance of the
fuel level sender is 31 ohms for a full tank of fuel,
101 ohms for 1/2 tank and 255 ohms for an empty
tank. A defective fuel level sender in the fuel tank
may also prevent the fuel level indicator from
moving.
9.10.4
Hourmeter
The hourmeter is a non-repairable instrument that
records hours of machine engine operation in tenth of an
hour increments and is located in the instrument cluster.
The hourmeter is an analog device, similar to an
odometer, and will display 99,999.9 hours before
resetting to zero.
If trouble is suspected, time the hourmeter for six minutes
to verify that a tenth of an hour has been recorded.
The hourmeter is built into the instrument cluster and
cannot be repaired. If the hourmeter is suspect, replace
the instrument cluster.
9.10.5
Coolant Temperature Sender
The coolant temperature sender (2) is located on the top
of the engine behind the top radiator hose.
a. Coolant Temperature Sender Removal
1. Park the machine on a firm, level surface, level the
machine, fully retract the boom, lower the boom,
place the transmission control lever in (N)
NEUTRAL, engage the park brake and shut the
engine OFF.
2. Place a Do Not Operate Tag on both the ignition key
switch and the steering wheel, stating that the
machine should not be operated.
3. Open the battery and engine covers. Allow the
engine to cool.
4. Properly disconnect the battery.
5. Disconnect the wiring connector at the coolant
temperature sender lead.
6. The coolant temperature sender is threaded into the
engine block. Remove the sender.
b. Coolant Temperature Sender Inspection and
Replacement
Inspect the sender and the wiring harness connector
terminals for continuity. Replace a defective or faulty
sender with a new part.
c. Coolant Temperature Sender Installation and
Testing
1. Thread the coolant temperature sender into the
engine housing snugly, then connect the sender
connector to the wiring harness connector.
2. Properly connect the battery.
3. Check for proper fluid level.
4. Start the engine, allow it to reach operating
temperature and observe the operator’s instrument
cluster for warning indication. If the sender is not
defective, the problem could be elsewhere; possibly
in a shorted wire, improper-running engine, improper
or low coolant, obstructed or faulty radiator, coolant
pump, loose fan belt, defective instrument display,
etc.
5. Close and secure the battery and engine covers.
6. Remove the Do Not Operate Tags from both the
ignition key and the steering wheel.
MY8820
2