Campbell Scientific CPEC200 Closed-Path Eddy-Covariance System User Manual
Page 66
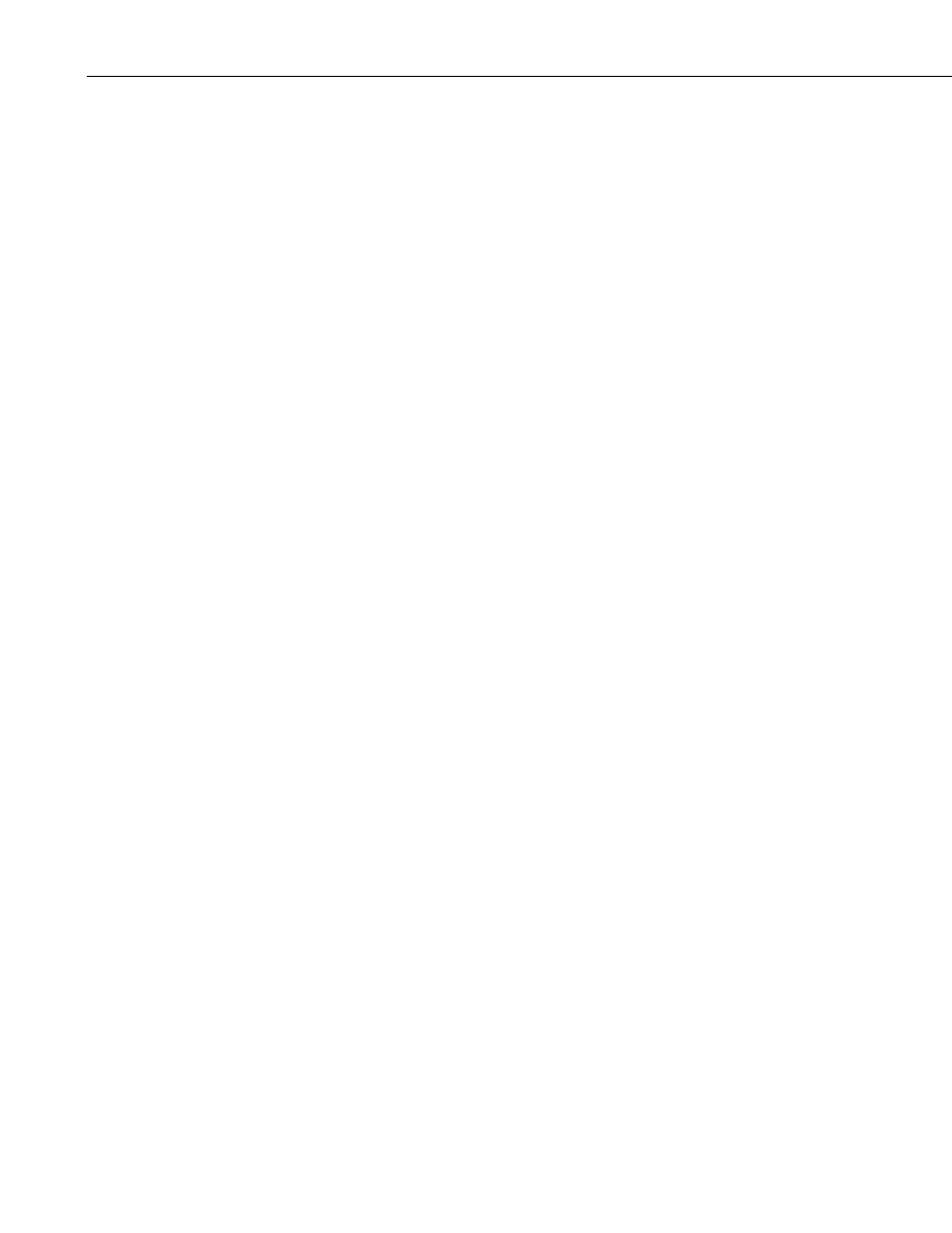
Appendix A. CPEC200 Diagnostics
Conversely, processing tasks that affect real-time control functions may be
adversely affected if there are processing delays. The control algorithms that
adjust the pumping speed and valve flow are processing tasks. If the
datalogger processing is delayed these algorithms will use “old” measurements.
This will cause the pump speed or valve flow to be poorly controlled.
The datalogger reports how far behind the processing task is in the public
variable
buff_depth (this is a copy of the variable BuffDepth from the Status
table; more details can be found in the CR3000 Micrologger Operator’s
Manual). The processing delay is given as the number of datalogger
measurement scans. If the buffer depth exceeds 10 scans (a one second delay
for 100 ms scan interval), the control algorithms are disabled, public variable
buff_depth_OK = False, and diagnostic bit 4 is set. The control algorithms
will be disabled until the processing task can catch up to within 10 scans.
While all of the other diagnostic flags indicate conditions that make the
measurements invalid, this is not necessarily the case with
buff_depth_OK.
For post-processing time-series data, it may be acceptable to use data with
buff_depth_OK = False, as long as the pump flow (or valve flow, if in
Zero/Span mode) is within range. In this case, the
buff_depth_OK diagnostic
can be considered a “warning” rather than an “error”. There are, however, two
other consequences to this flag. First, flagged data will not be included in the
on-line EC calculations, and, second, it will cause an automatic zero or span to
be aborted. Given this, the CPEC200 CRBasic program should be edited with
care and measurement or processing tasks that cause excessive delay should
not be added.
Bit 3: Valve Flow
If the remainder of
diag_cpec (after subtracting the numeric value for higher
bits that are set) is greater than 3, this means that bit 3 of
diag_cpec is set. To
decode other diagnostic bits, subtract 4 from
diag_cpec and compare the
remainder to the bit values below.
Bit 3 of
diag_cpec indicates the valve flow is not at the setpoint. To confirm
the problem, verify that public variable
valve_flow_OK = False. This variable
is set to true if the value of
valve_flow is within an acceptable range. The
criteria used to set this flag depend on several other variables.
If no valve is selected (
valve_number = 0), then the valve flow is not defined.
In this case,
valve_flow is set to zero and valve_flow_OK = True.
If a valve is selected, in most cases the valve flow should match the setpoint
within 10%. There are two exceptions to this rule. First, if the H
2
O span valve
(6) is selected, the flow is controlled by dewpoint generator rather than the
CPEC200 system. The dewpoint generator pushes flow through the valve
module to the IRGA. The CPEC200 fully opens the flow control valve by
setting
valveControl = 1. The acceptable range for valve_flow is between 0.2
and 2.0 LPM.
The second exception is when the flow is controlled by the scrub module and
the
ZeroAir valve (1) is selected. The scrub module has a pump to push the
zero air through the valve module to the IRGA. The CPEC200 fully opens the
flow control valve by setting
valveControl = 1. The acceptable range for
valve_flow is between 0.5 and 3.0 LPM.
A-14