Input and output parameters – Watlow ANASOFT User Manual
Page 41
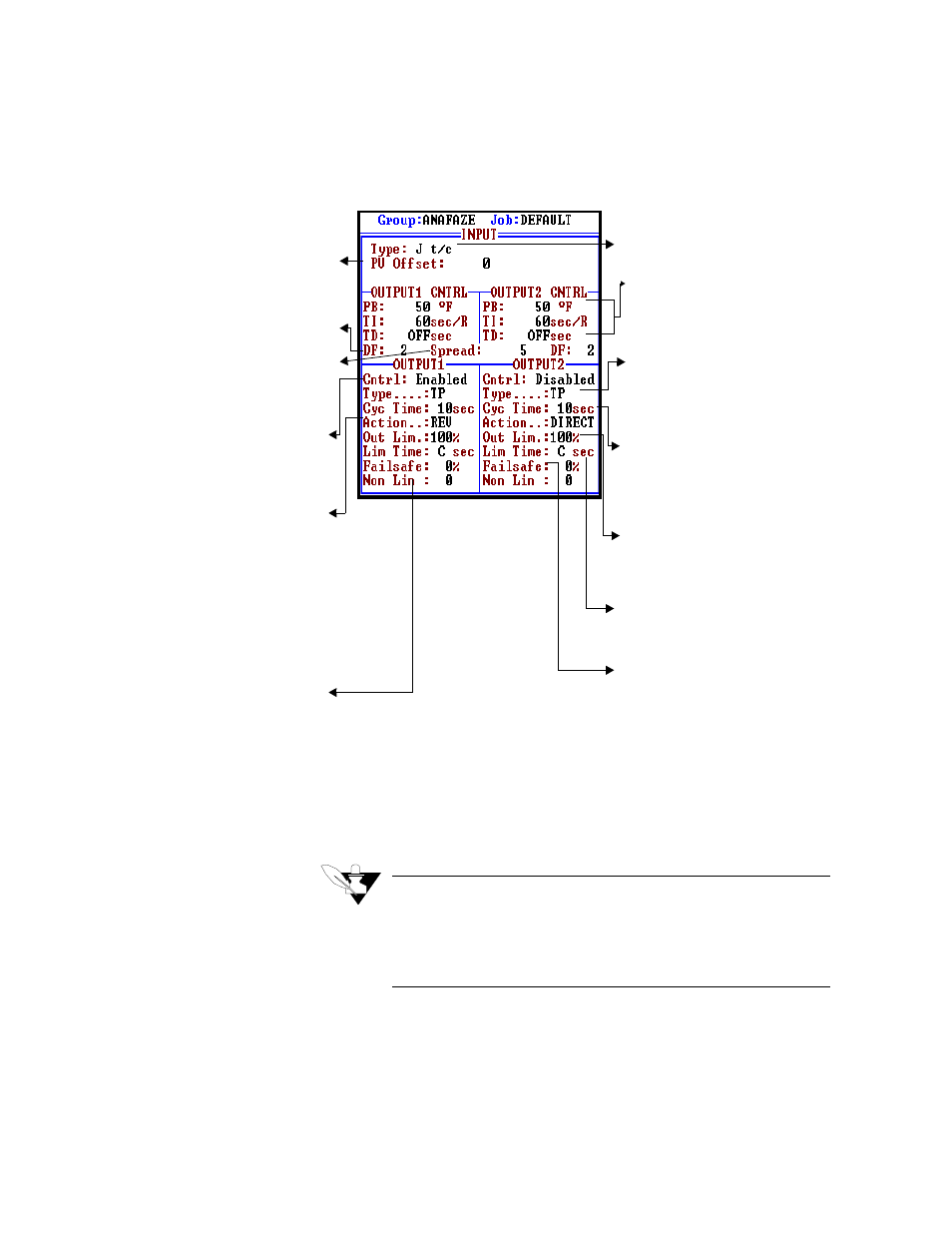
Loop Setup
ANASOFT User’s Guide 31
Input and Output parameters
NOTE
Set input type first. All Loop pertinent parameters are
in reference to the input type and engineering unit.
The input must be correct before setting SP, PB,
alarms SP etc.
Input type. See table on the next
Proportional Band, Reset,
Rate. See PID Tuning.
Process offset. Use it to make
up for input signal’s inaccu-
Digital filter. The average PV
over number of scans selected.
The spread between the heat
output and the cool output.
Enable or disable the output.
When controlling a process, at
least one loop should be
TP--Time Proportioning
DZC--Distributed Zero Crossing
On/Off Control
ANA--Analog control (8LS)
Cycle time. Set in seconds the
time a controller takes to com-
plete one on/off cycle. Use only
with TP output type.
Set to Direct or Reverse.
Reverse action causes the out-
put to increase while PV
decreases. Normally used in
heating control. Direct action
causes the output to increase
while PV increases. Normally
Limits the PID control output for
heating and cooling.
Sets a time limit for the output
limit. Set between 1 and 999 sec-
onds.
The output percentage when the
controller failed back to manual
mode.
Nonlinear outputs. Use it to
match control outputs to spe-
cial situations.The output
curves provide a gentle onset
of control action near the set-
point. Set to 0 for linear out-
puts, and to 1 or 2 according to