3 adjustment 2 – IAI America PDR-101-MW User Manual
Page 77
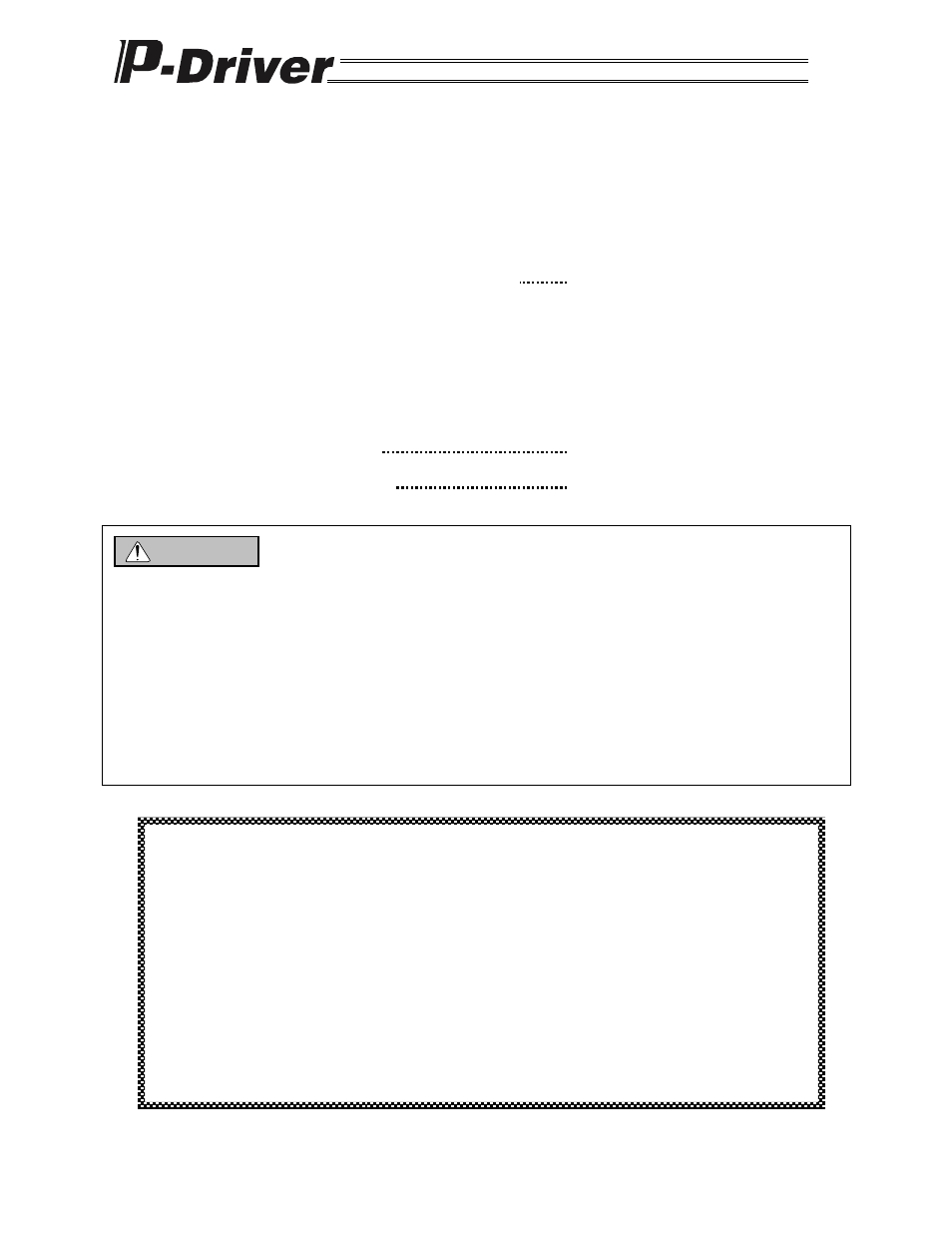
67
6.4.3 Adjustment
2
(1) Shocks at Start/Stop
It is desired to move smoothly without sudden acceleration/deceleration or accelerate/decelerate smoothly
to change the speed to match the command speed (including a speed of 0).
Set the “position command primary filter time constant.”
See (18) in Section 6.3.2.
(2) Abnormal Noise at Low Speed (Stop)
High-pitched abnormal noise occurs, in particular, at low speeds (50 mm/sec or less).
Set the “torque filter time constant.”
See (30) in Section 6.3.2.
Lower the “current control bandwidth.
See (31) in Section 6.3.2.
z
This phenomenon tends to occur when the rigidity of the system’s mechanical parts is not maintained.
The actuator unit itself may generate torsional resonance if its stroke exceeds 600 mm or if it is a
belt-driven type.
Check the following items before making adjustment:
1. The position control loop proportional gain, speed loop gain and speed loop integration time
constant are not set too high.
2. The rigidity of the load is maintained as much as possible, and the load is securely mounted
without looseness and play.
3. There is no distortion on the actuator’s mounting surface.
4. The actuator body is installed securely.
[Points]
1) Torque filter time constant
Resonance between mechanical parts of the system can be suppressed by setting this
value higher (increase the value in steps of 500
µsec). Note, however, that if the value is set
too high, the stability of the control system may be lost (vibration occurs).
2) Current control bandwidth
It is possible to make adjustment by decreasing the setting value of this parameter
(decrease the value in steps of 200 rad/sec as a guideline), but this should only be done if
the problem cannot be adjusted with the torque filter.
If the current control bandwidth is lowered, the torque filter time constant may be lowered as
well in some cases. Place priority on the torque filter time constant when making
adjustment.
Caution