IAI America PDR-101-MW User Manual
Page 55
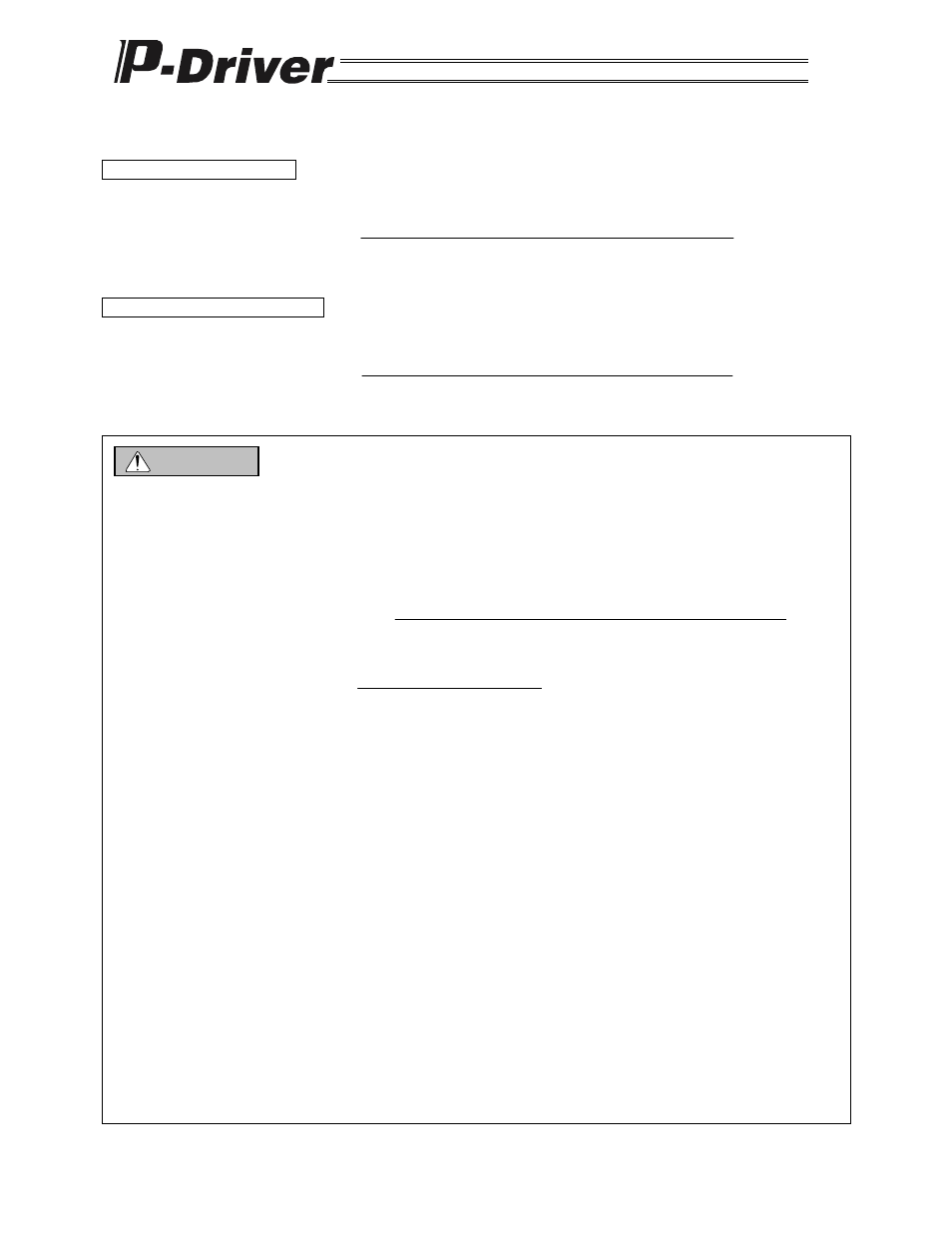
45
Calculation formula for stroke pulse value
In the case of linear axis:
(mm/rev)
length
lead
screw
Ball
)
(pulse/rev
pulses
encoder
of
Number
x
(mm)
value
Stroke
(pulse)
value
Setting
=
In the case of rotational axis:
rate
reduction
gear
axis
Rotational
x
(deg/rev)
360
)
(pulse/rev
pulses
encoder
of
Number
x
(deg)
value
Stroke
(pulse)
value
Setting
=
z
The software stroke limit is set differently according to the setting of homing pattern code (motor
revolution direction at homing), a position control information parameter. For example, in the case of
an actuator with a stroke of 100 (mm), a lead of 10 (mm) and a number of encoder pulses of 16384
(pulse), the stroke pulse value is calculated as follows:
(pulses)
163840
(mm/rev)
10
)
(pulse/rev
16384
x
(mm)
100
(mm/rev)
length
lead
screw
Ball
)
(pulse/rev
pulses
encoder
of
Number
x
(mm)
value
Stroke
(pulse)
value
pulse
Stroke
=
=
=
The limits are set as follows:
a. If the setting of homing pattern code is “1” (the motor revolution direction is forward at homing), LIMM
is set to 0 (pulse) and LIML is set to -163840 (pulse).
b. If the setting of homing pattern code is “0” (the motor revolution direction is reverse at homing), LIMM
is set to 163840 (pulse) and LIML is set to 0 (pulse).
For this reason, it is necessary to change these parameters as well if the homing pattern code parameter is
to be changed.
Note, however, that the values of LIML and LIMM are automatically rewritten when the homing pattern code
is changed if the display unit is set to “Millimeter (mm)” and the coordinate plus process display is set to
“Display” in the environment setting of the PC software.
Caution