Electronics International MVP-50P User Manual
Page 52
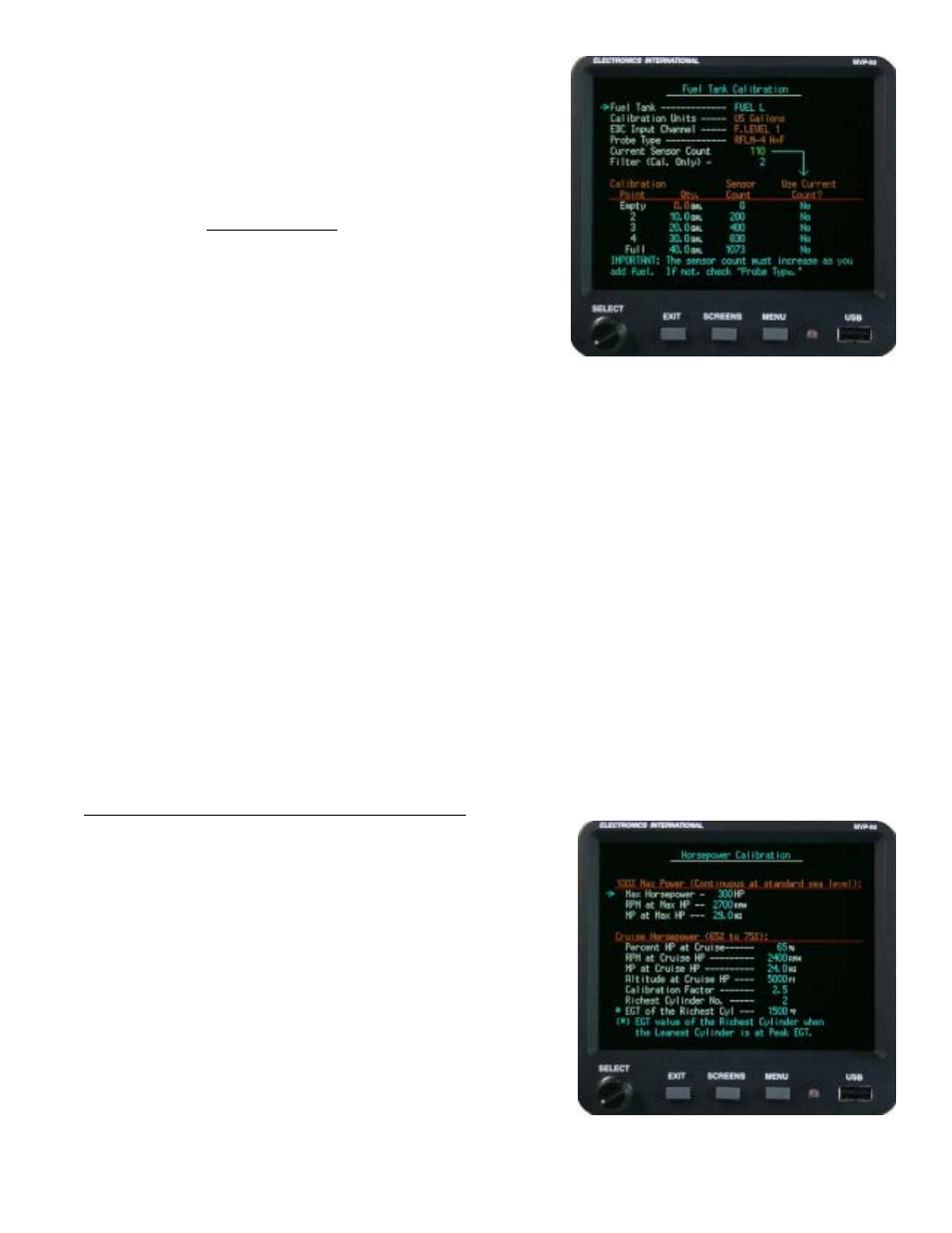
53
The tanks must be calibrated with the wings level and the aircraft
set for level flight pitch. Start with the tanks empty.
“Fuel Tank”: This field selects the fuel tank to be calibrated.
You can switch between tanks any time during the calibration
cycle.
Note: The tanks must be calibrated in US gallons. However, fuel
levels may be displayed in other units by changing the “Display
Units” field in the “3. Redlines, Limits and Color Setup” screen.
“Current Sensor Count”: This is the output count measured on
the fuel level probe. A sensor count represents a fuel level. The
calibration process below associates a sensor count to a fuel level.
“Calibration Filter”: When fuel is added to the tank the sensor count will increase. When you stop adding fuel to
the tank the sensor count will continue to climb for a short period of time and then stop climbing. If the sensor count
does not settle out (continues to jump up and down), increase the “Calibration Filter.” The higher the Calibration
Filter the more stable the counts will be and the longer it will take for the sensor counts to settle out.
“Calibration Points, Qty, Sensor Count, Use Current Count?”: Start with an empty tank. Wait for the
“Current Sensor Count” to settle. Select the Empty “Calibration Point.” Transfer the “Current Sensor Count” to
the “Sensor Count” field by selecting YES in the “Use Current Count?” field.
Use the same process for each Calibration Point. You may want to use ¼, ½ and ¾ tank levels for calibration
points 2, 3 and 4. You may set a Calibration Point at any desired fuel level but each successive Calibration Point
must have a “Qty” and “Sensor Count” the same or higher than the previous one. Ideally, the sensor counts should
increase more than 5 counts for every gallon of fuel added to the tank.
You can use as few as two Calibration Points (Empty and Full). For any Calibration Point you do not use, set the
“Qty” and “Sensor Count” to the same settings as the previous “Calibration Point.”
6.12 “Horsepower Calibration” Screen:
Engine horsepower is calculated from RPM, Manifold Pressure,
Altitude and the Mixture setting. Most of the data is available from
engine performance charts found in your aircraft’s POH or from the
engine manufacturer.
The MVP will acquire Altitude data from one of three sources. If
Pressure Altitude is measured by the EDC and set up as a function
on the MVP, then Pressure Altitude data will be used to calculate
Horsepower. If Pressure Altitude is not a function on the MVP but
the GPS received data contains Altitude, then GPS Altitude data
will be used to calculate Horsepower. If neither Pressure Altitude
nor GPS Altitude is available, then 2500 feet will be used to
calculate Horsepower.