Calibration gas feed and backflushing – M&C TechGroup SP2020-H_C_I_BB_F Operator's manual User Manual
Page 19
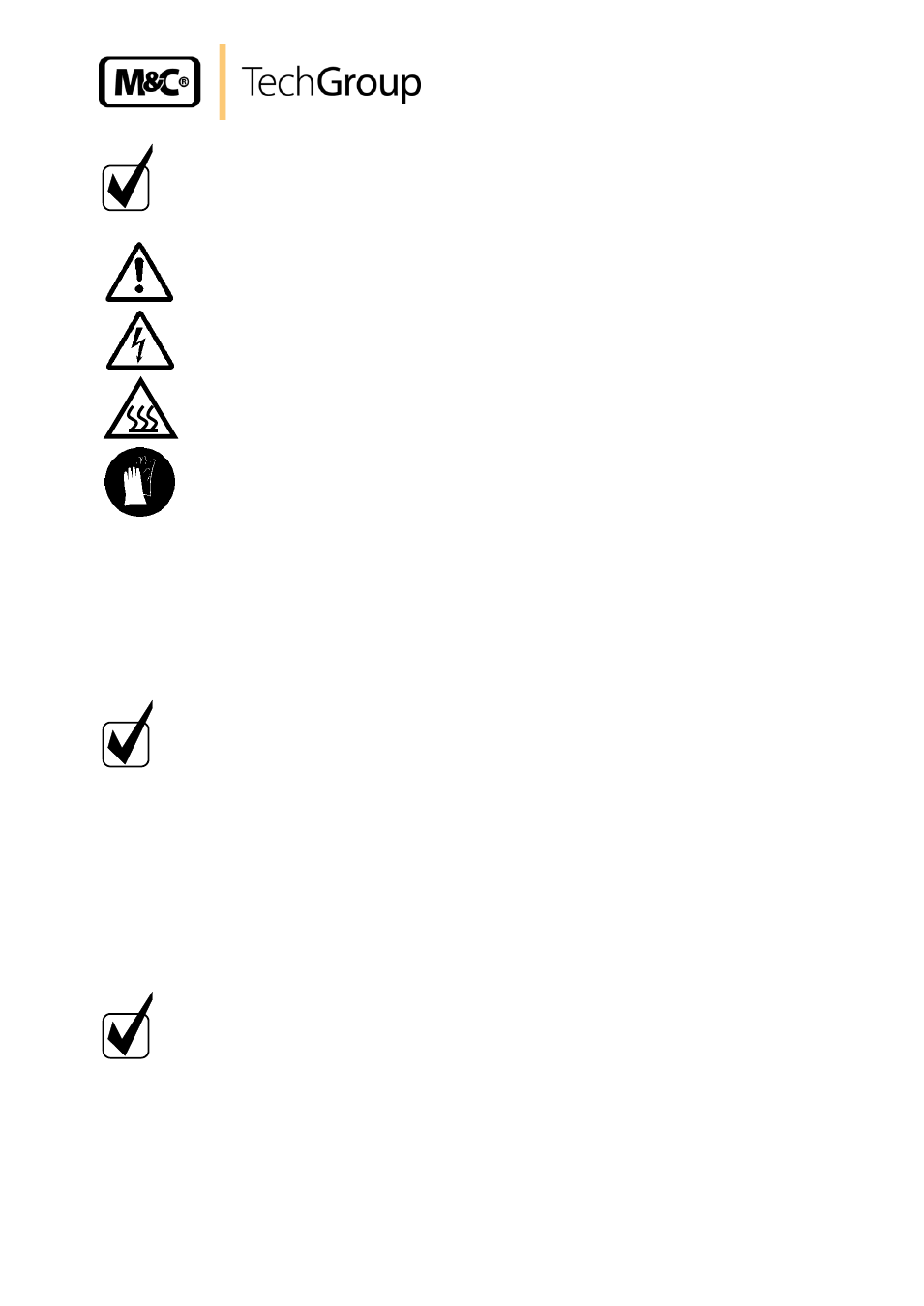
19
Gas sampling and gas conditioning technology
2-1.1.6.1-ME
N O T E !
If the rated value temperature needs to be lowered more than 30°C
in one step during operation, the thermostat's excess temperature
switch-off is triggered!
W A R N I N G !
Be care
ful when you get in contact with the probe’s surface during
operation. The high surface temperatures may cause burnings.
Protective gloves are to be born and any unauthorized access to
the probe must be made impossible !
14.1
CALIBRATION GAS FEED AND BACKFLUSHING
In order to backflush the probe tube or the prefilter, flush gas is fed via the backflush valve. The
downstream system has to be disconnected with the isolation valve from the probe before back flush-
ing in order to avoid pressure shocks on the system. The check valve's opening pressure is 0,7bar. To
drive the isolation valve a pressure of 3-10 bar is necessary.
N O T E !
In order to prevent the probe's interior from cooling down, back-
flushing should as far as possible only be carried out for a short
time (<1s).
The analysis system remains closed while calibration gas is being fed in. The amount of calibration
gas should be at least 25% greater than the amount of sample gas drawn into the analysis system in
order to avoid mixing with the sample gas. This type of calibration gas feeding is not to be used in the
case of processes with over pressure. A built-in ball valve in the probe entrance is recommended
here.
Basically, a smaller amount of calibration gas is needed in probes with a built-in ball valve as the
probe is separated from the system on activating the ball valve and thus there is no danger of mixing
with the process gas. In order to close the probe the control grip is to be turned by hand to the right
until it reaches the stop.
N O T E !
In the case of low pressure care should be taken that no infiltrated
air is drawn in via the unclosed check valve from 300 mbar up-
wards.