Siemens MICROMASTER 440 User Manual
Page 31
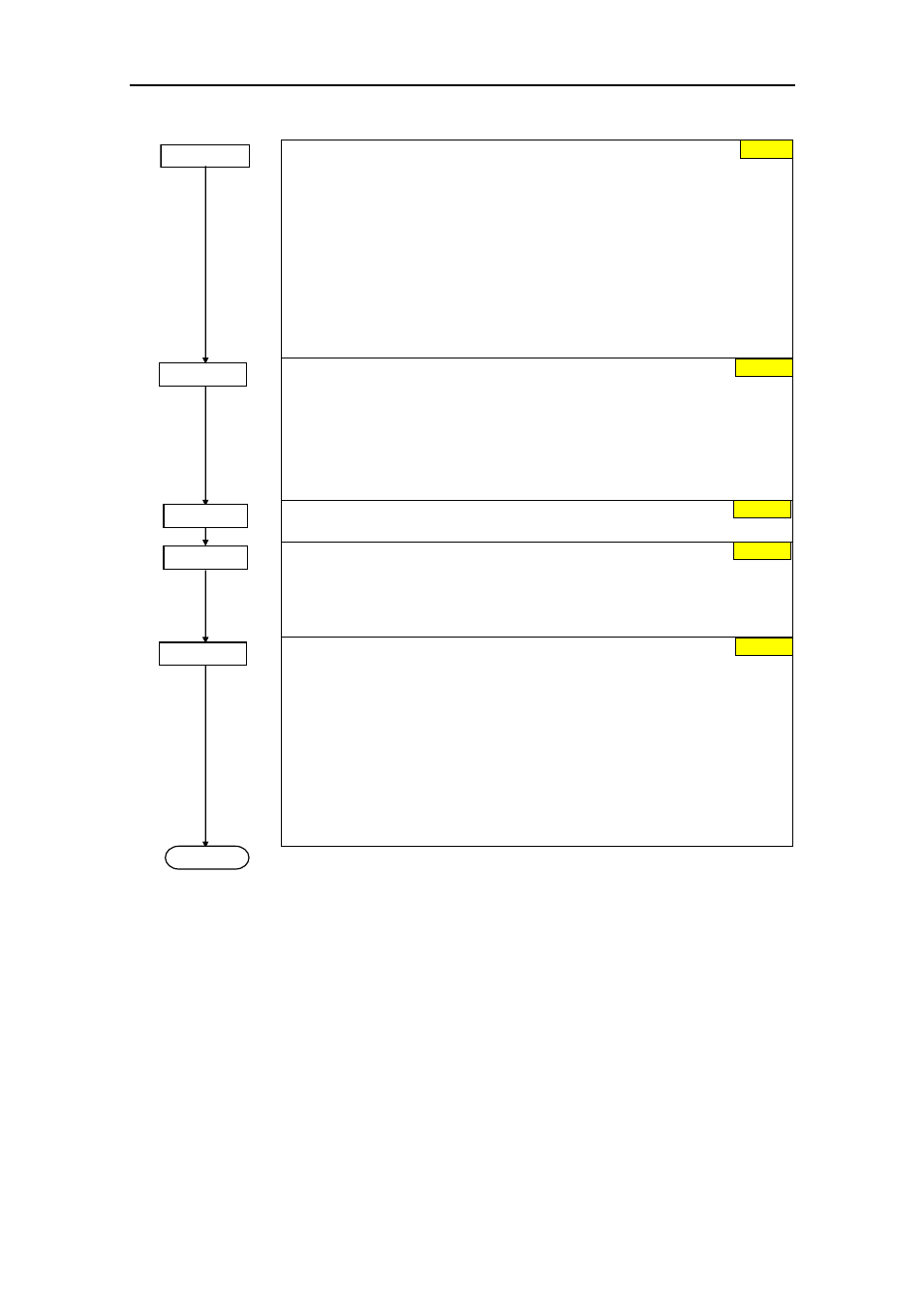
Issue 10/06
6 Commissioning
MICROMASTER 440
Operating Instructions (Compact)
31
P1300 =...
Control mode
(enters the required control mode)
0 V/f with linear characteristic
1 V/f with FCC
2 V/f with parabolic characteristic
3 V/f with programmable characteristic
5 V/f for textile applications
6 V/f with FCC for textile applications
19 V/f control with independent voltage setpoint
20 Sensorless Vector control
21 Vector control with sensor
22 Sensorless Vector torque-control
23 Vector torque-control with sensor
Selection of torque setpoint *
(enters the source for the torque setpoint)
0 No main setpoint
2
Analog setpoint
4 USS on BOP link
5 USS on COM link (control terminals 29 and 30)
6 CB on COM link (CB = communications module)
7 Analog setpoint 2
Select motor data identification *
0 Disabled
Speed controller optimization *
0 Inhibited
In order to optimize the speed controller, the closed-loop vector control (P1300 =
20 or 21) must be activated. After the optimization has been selected
(P1960 = 1), Alarm A0542 is displayed.
End of quick commissioning
(start of the motor calculation)
0 No quick commissioning (no motor calculations)
1 Motor calculation and reset of all of the other parameters, which are not
included in the quick commissioning (attribute "QC" = no), to the factory
setting
2 Motor calculation and reset of the I/O settings to the factory setting
3 Only motor calculation. The other parameters are not reset.
NOTE
For P3900 = 1,2,3
→ P0340 is internally set to 1 and the appropriate data
calculated.
End of the quick commissioning/drive setting
If additional functions must be implemented at the drive inverter, please use the
Section "Commissioning the application" (refer to Section 6.4). We recommend
this procedure for drives with a high dynamic response.
0
P1500 =...
0
P3900 = 1
P1910 = ...
P1960 = ...
0
0
0
END