Installation, Step 1: basic installation guidelines, Electromagnetic compatibility (emc) – Emerson 400518-01 User Manual
Page 15: Achieving low impedance connections
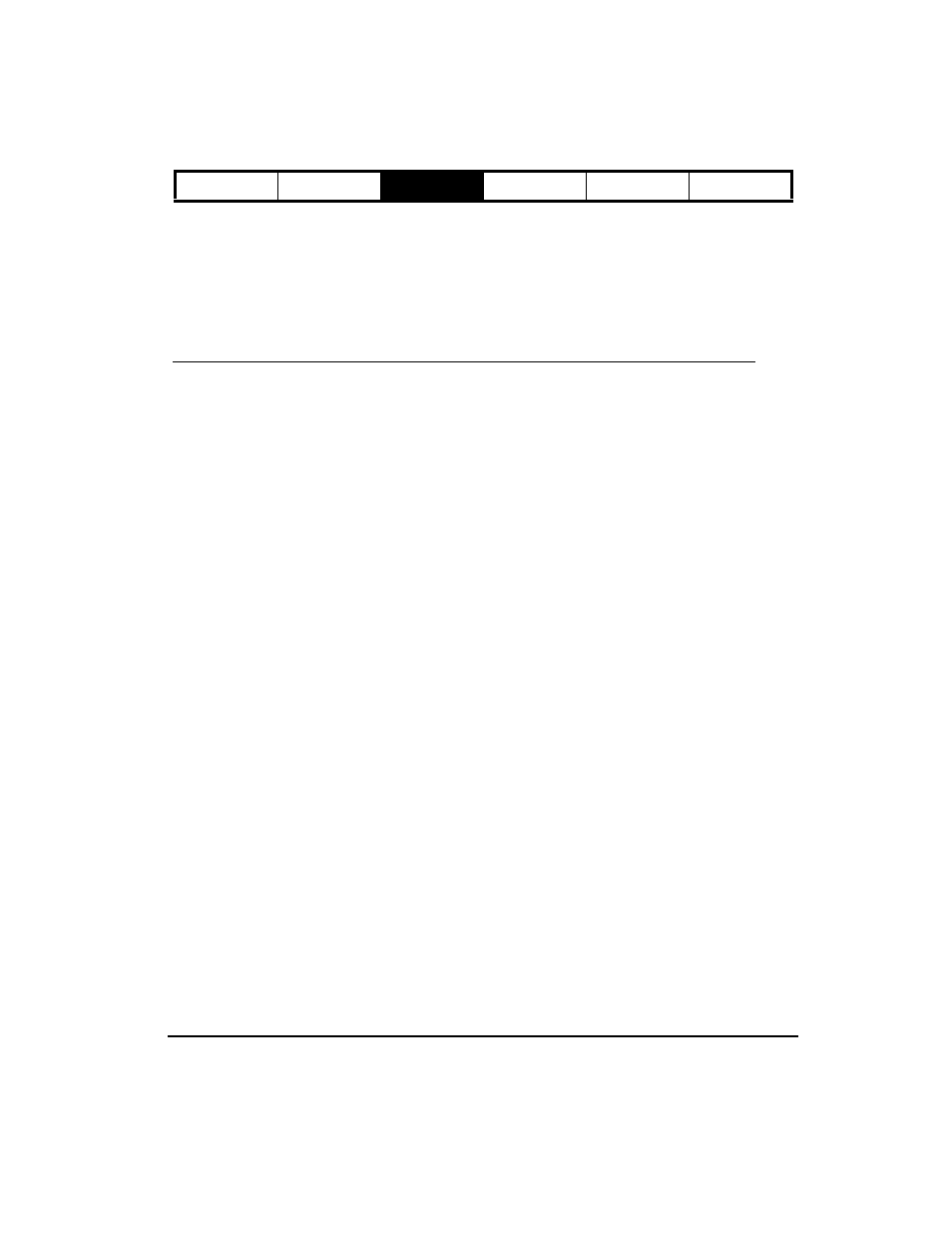
Installation
3
Safety Information
Product Overview
Installation
Diagnostics
Options and
Accessories
Specification
Installation
Installation of the Epsilon EP drive is completed by following a simple step-by-step process. The Epsilon EP
installation begins by mounting the drive to a metal mounting panel. Next, the high power connections are made to
the drive, then the low power connections are made.
Step 1:
Basic Installation and Panel Layout, page 3
Step 2:
Mechanical Installation, page 7
Step 3:
High Power Connections, page 10
Step 4:
Low Power Connections, page 22
Step 1: Basic Installation Guidelines
You are required to follow all safety precautions during start-up such as providing proper equipment grounding,
correctly fused power and an effective Emergency Stop circuit which can immediately remove power in the case of
a malfunction. See the "Safety Considerations" section for more information.
Electromagnetic Compatibility (EMC)
Drives are designed to meet the requirements of EMC. Under extreme conditions a drive might cause or suffer from
disturbances due to electromagnetic interaction with other equipment. It is the responsibility of the installer to ensure
that the equipment or system into which the drive is incorporated complies with the relevant EMC legislation in the
country of use.
The following instructions provide you with installation guidance designed to help you meet the requirements of the
EMC Directive 89/336/EEC.
Adhering to the following guidelines will greatly improve the electromagnetic compatibility of your system, however,
final responsibility for EMC compliance rests with the machine builder, and Control Techniques Americas LLC cannot
guarantee your system will meet tested emission or immunity requirements.
If you need to meet EMC compliance requirements, EMI/RFI line filters must be used to control conducted and
radiated emissions as well as improve conducted immunity.
Physical location of these filters is very important in achieving these benefits. The filter output wires should be kept
as short as practical and routed away from the filter input wires. In addition:
• Choose an enclosure made of a conductive material such as steel, aluminum or stainless steel.
• Devices mounted to the enclosure mounting plate, which depend on their mounting surfaces for grounding,
must have the paint removed from their mounting surfaces and the mating area on the mounting plate to ensure
a good ground. See “Achieving Low Impedance Connections” on page 3 for more information.
• If grounding is required for cable grommets, connectors and/or conduit fittings at locations where cables are
mounted through the enclosure wall, paint must be removed from the enclosure surface at the contact points.
• Cables should be shielded, and all shields must be grounded to the enclosure.
To meet radiated emissions requirements, the enclosure door must be closed and have electrical conduction at
hinges and closure hardware or be fitted with a conductive gasket. Route cables away from the door where possible
to minimize coupling emissions to door where they can re-radiate. The door generally must be bonded to the
enclosure for electrical safety, but this is not sufficient to meet EMC.
Achieving Low Impedance Connections
Noise immunity can be improved and emissions reduced by making sure that all the components have a low
impedance connection to the same ground point. A low impedance connection is one that conducts high frequency
current with very little resistance. Impedance cannot be accurately measured with a standard ohmmeter, because
an ohmmeter measures DC resistance. For example, a 12 inch long 8 gauge round wire has a significantly higher
impedance than a 12 inch long 12 gauge flat braided conductor. A short wire has less impedance than a long one.
Low impedance connections can be achieved by bringing large areas of conductive surfaces into direct contact with
each other. In most cases this requires paint removal because a ground connection through bolt threads is not
sufficient. However, component materials should be conductive, compatible and exhibit good atmospheric corrosion
resistance to prevent loss through corrosion that will hinder the low impedance connection. Enclosure manufacturers
offer corrosion resistant, unpainted mounting plates to help.