Boring (cycle 202), 2 dr illing cy cles – HEIDENHAIN TNC 310 (286 140) User Manual
Page 112
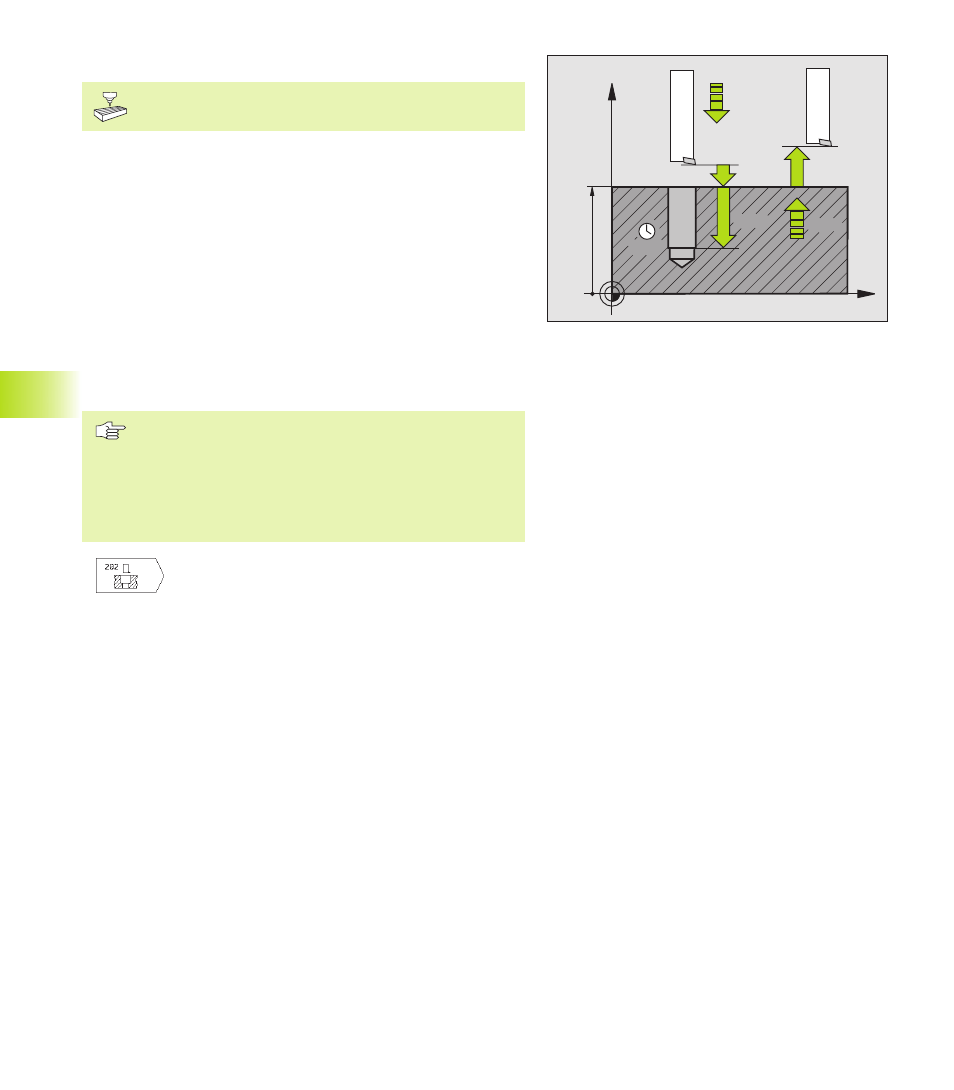
8 Programming: Cycles
100
BORING (Cycle 202)
Machine and control must be specially prepared by the
machine tool builder to enable Cycle 202.
1 The TNC positions the tool in the tool axis at rapid traverse FMAX
to set-up clearance above the workpiece surface.
2 The tool drills to the programmed depth at the feed rate for
plunging.
3 If programmed, the tool remains at the hole bottom for the
entered dwell time with active spindle rotation for cutting free.
4 The TNC then orients the spindle to the 0° position
with an oriented spindle stop.
5 If retraction is selected, the tool retracts in the programmed
direction by 0.2 mm (fixed value).
6 The tool then retracts to set-up clearance at the retraction feed
rate, and from there — if programmed — to the 2nd set-up
clearance in FMAX.
Before programming, note the following:
Program a positioning block for the starting point (hole
center) in the working plane with RADIUS
COMPENSATION R0.
The algebraic sign for the cycle parameter TOTAL HOLE
DEPTH determines the working direction.
ú
Set-up clearance Q200 (incremental value):
Distance between tool tip and workpiece surface.
ú
Depth Q201 (incremental value): Distance between
workpiece surface and bottom of hole
ú
Feed rate for plunging Q206: Traversing speed of
the tool during boring in mm/min
ú
Dwell time at depth Q211: Time in seconds that
the tool remains at the hole bottom
ú
Retraction feed rate Q208: Traversing speed of the
tool in mm/min when retracting from the hole. If
you enter Q208 = 0, the tool retracts at feed rate
for plunging.
ú
Workpiece surface coordinate Q203 (absolute
value): Coordinate of the workpiece surface
ú
2nd set-up clearance Q204 (incremental value):
Coordinate in the tool axis at which no collision
between tool and workpiece (clamping devices)
can occur.
X
Z
Q200
Q201
Q206
Q211
Q203
Q204
Q208
8.2 Dr
illing Cy
cles