Drilling (cycle 200), 2 dr illing cy cles – HEIDENHAIN TNC 310 (286 140) User Manual
Page 110
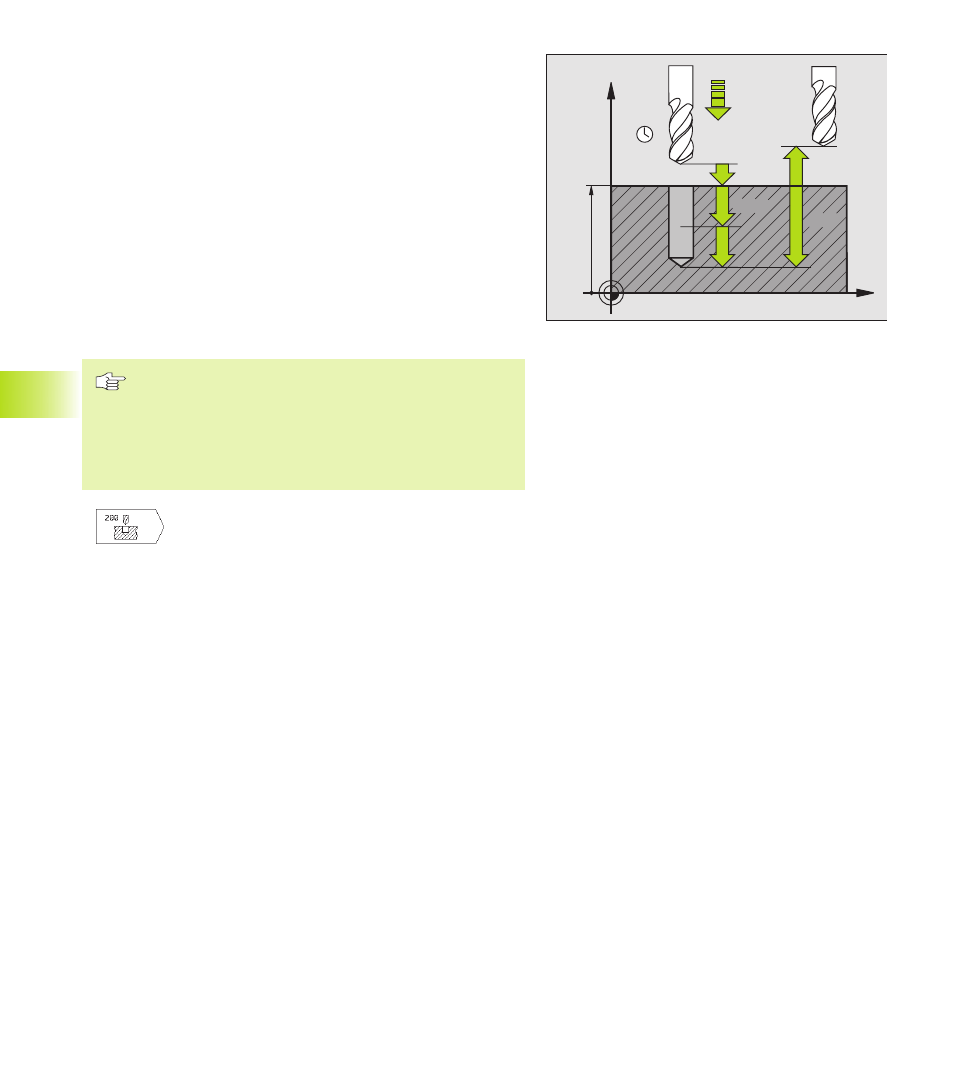
8 Programming: Cycles
98
DRILLING (Cycle 200)
1 The TNC positions the tool in the tool axis at rapid traverse FMAX to
the set-up clearance above the workpiece surface.
2 The tool drills to the first plunging depth at the programmed feed
rate F.
3 The TNC returns the tool at FMAX to the setup clearance, dwells
there (if a dwell time was entered), and then moves at FMAX to
the setup clearance above the first plunging depth.
4 The tool then advances with another infeed at the programmed
feed rate F.
5 The TNC repeats this process (2 to 4) until the programmed total
hole depth is reached.
6 At the hole bottom, the tool is retraced to set-up clearance or —
if programmed — to the 2nd set-up clearance in rapid traverse
FMAX.
Before programming, note the following:
Program a positioning block for the starting point (hole
center) in the working plane with RADIUS
COMPENSATION R0.
The algebraic sign for the depth parameter determines
the working direction.
ú
Set-up clearance Q200 (incremental value):
Distance between tool tip and workpiece surface.
ú
Depth Q201 (incremental value): Distance between
workpiece surface and bottom of hole (tip of drill
taper)
ú
Feed rate for plunging Q206: Traversing speed of
the tool during drilling in mm/min
ú
Plunging depth Q202 (incremental value):
Infeed per cut The TNC will go to depth in one
movement if:
■
the plunging depth is equal to the depth
■
the plunging depth is greater than the depth
The depth does not have to be a multiple of the
plunging depth.
ú
Dwell time at top Q210: Time in seconds that the
tool remains at set-up clearance after having been
retracted from the hole for chip release.
ú
Workpiece surface coordinate Q203 (absolute
value): Coordinate of the workpiece surface
ú
2nd set-up clearance Q204 (incremental value):
Coordinate in the tool axis at which no collision
between tool and workpiece (clamping devices)
can occur.
X
Z
Q200
Q201
Q206
Q202
Q210
Q203
Q204
8.2 Dr
illing Cy
cles