Shut-off valves, Crankcase heater, Liquid line strainer-drier – Carrier 07D User Manual
Page 23: Flare connections, Soldering and brazing piping to valves, Water regulating valves (water-cooled units only), Liquid line solenoid valve (field supplied), Liquid line sight glass, Condenser water connections, 06d,07d
Attention! The text in this document has been recognized automatically. To view the original document, you can use the "Original mode".
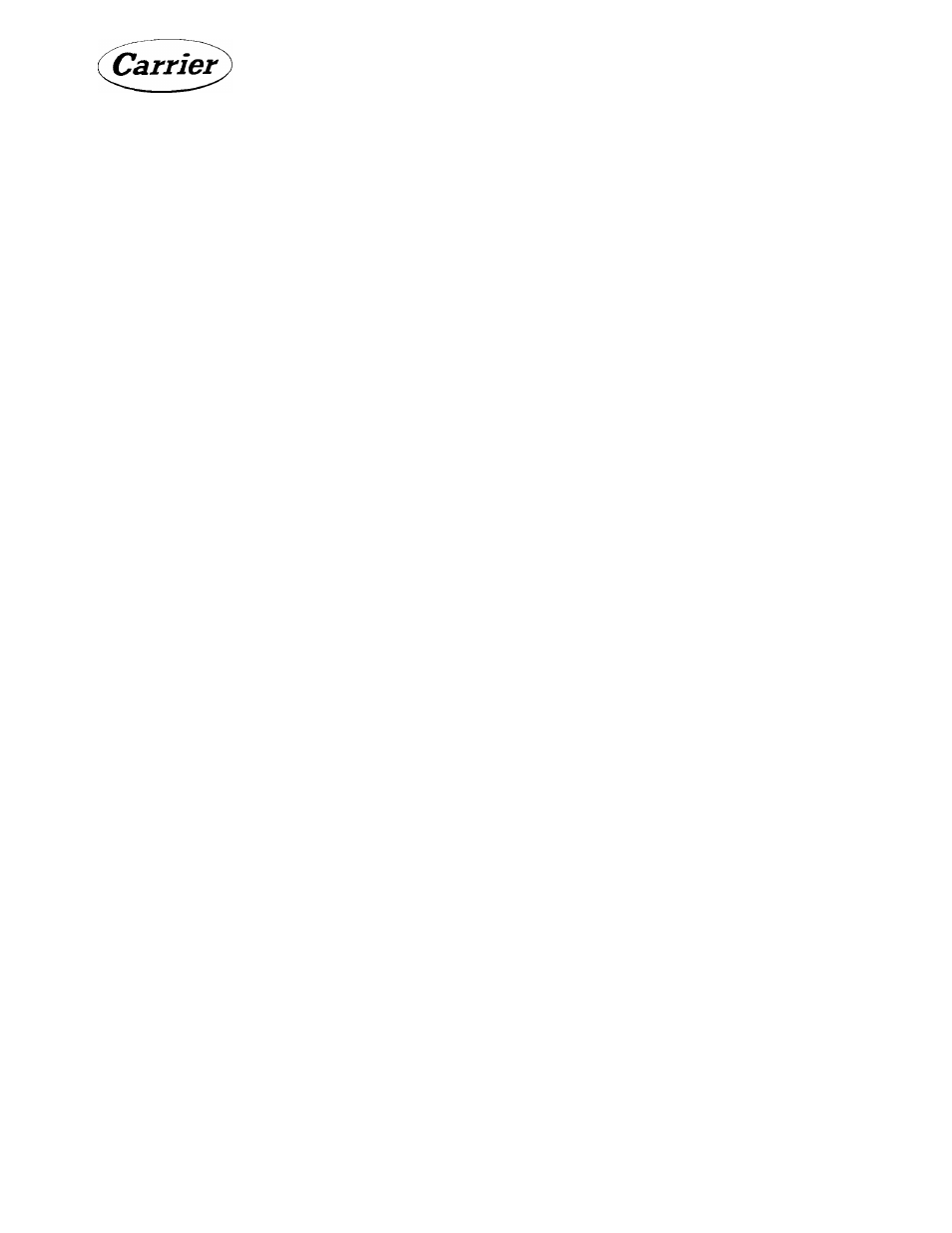
INSTALLATION
06D,07D
#
Shut-Off Valves
The suction and discharge shut-off valves are
of the backseating type and have gage ports.
Frontseating the valve closes the refrigerant
line and opens the gage port to the pressure in
the compressor.
Backseating the valve shuts off pressure to the
gage port. To attach a gage or charging line to
the gage port, backseat the valve to prevent es
cape of refrigerant.
U se a square ratchet or box-end wrench to open or
close a valve. Do not use pliers or an adjustable
wrench. They are likely to round the valve stem.
Do not use excessive force to turn the stem. If
it turns hard, loosen the packing gland nut. If
the valve sticks on its seat, a sharp rap on the
wrench will usually break it loose.
Crankcase Heater
The crankcase heater is an internal cartridge-
type heater that is inserted in a blind hole in
the compressor bottom cover. It does not come
in direct contact with the oil. The heater draws
75 watts and is held in the hole by a clip. In
sure that the crankcase is held tightly in place
by the clip.
The heater is approved for wet locations.
The crankcase heater should be energized at
least 12 hours before start-up to insure that
the refrigerant is out of the oil.
Liquid Line Strainer-Drier
Install the liquid line strainer-drier in the liquid
refrigerant line. The drier should be installed
between the sight glass and the solenoid valve.
Flare Connections
Using too much force in tightening flare nuts
will damage the copper flare. Repeated tighten
ing will harden the copper. To soften copper
tubing, heat it to a dull red and allow it to cool.
Soldering and Brazing Piping to Valves
Disassemble the valve or wrap it in wet cloth
to prevent damage by heat.
Water Regulating Valves (Water-Cooled Units
Only)
Install the water regulating valve with the cap
illary down and the arrow on the valve body in
the direction of water flow.
1. Backseat the liquid line shut-off valve.
2. Connect the capillary of the water regulating
valve to the 1 /4 inch flare connection on the
liquid line shut-off valve.
3. Open the shut-off valve one turn from the
backseated position. This allows refrigerant
pressure to reach the water regulating valve
and still leave the refrigerant line open.
NOTE: The water regulating valves for
R-12 and R-22 are not interchangeable.
Liquid Line Solenoid Valve (Field Supplied)
The puipose of this valve is to prevent dam
age to the compressor which would result from
flooding of the crankcase with refrigerant during
shutdown and to provide the pumpdown control
feature. Install this valve in the liquid refrig
erant line directly ahead of the expansion valve.
It must be installed in the vertical position and
wired as shown in the wiring diagrams.
Liquid Line Sight Glass
Install the liquid line sight glass between the
liquid line solenoid and expansion valve. Locate
the sight glass so that it is convenient to place
a light behind the glass when observing the liq
uid for proper charge.
Condenser Water Connections
When city water is used for condensing, the
condenser circuits are normally connected in
series.
When cooling tower water is used for condens
ing, the condenser circuits are normally con
nected in parallel. (See Fig. 18 for correct
connections.)
IMPORTANT: In the case of the 07DA210,
112, 215 WC Condensers, a plug in the upper
header must be removed to provide parallel
circuiting for cooling tower application. This
plug is accessible by removing the upper
header cap and unscrewing the Allen pipe
plug. (See Fig. 18 for proper wrench sizes.)
23