0 troubleshooting, General refrigeration circuit – Reznor MAPSII Series REDA Users Manual User Manual
Page 25
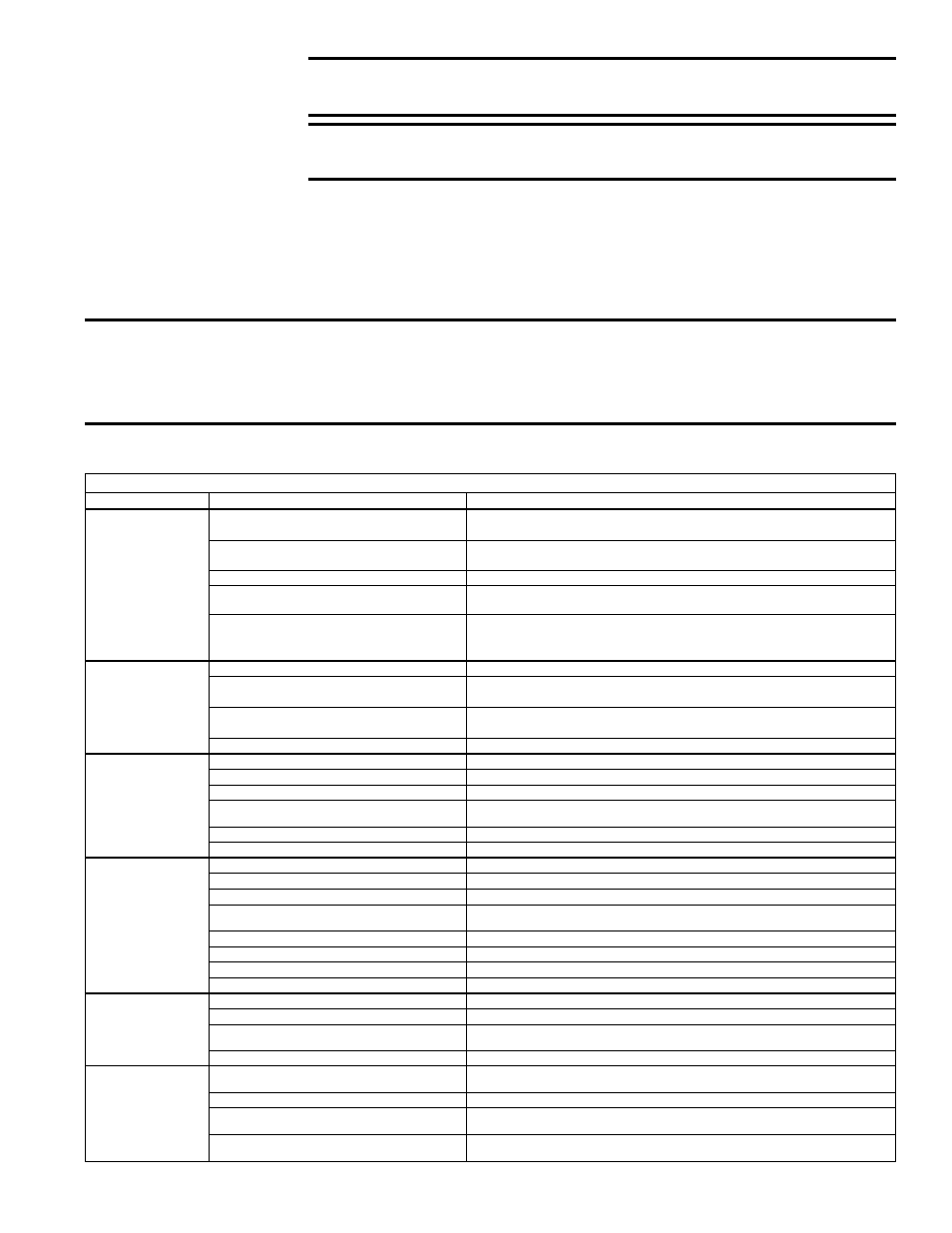
Form RZ-NA O-MAPS II, P/N 209179 R7, Page 25
(continued)
10.0 Electric Heat
Section
Maintenance
- Models
REDA and
RECA
DANGER: Turn off the power locking the disconnect switch.
Allow the heating elements to cool.
CAUTION: Wearing eye protection is recommended when clean-
ing the heating elements and cabinet.
Check the heating elements at the beginning of the heating season. Carefully
clean all dust and dirt from the heating elements using a brush or steel wool.
With a vacuum or air hose, clean the inside of the cabinet especially the bottom
and sides where dirt and dust will accumulate.
11.0 Troubleshooting
IMPORTANT: Do not release refrigerant to the atmosphere! If required service procedures
include the adding or removing of refrigerant, the service technician must comply
with all federal, state and local laws. The procedures discussed in this manual should
only be performed by a qualified HVAC technician.
General Refrigeration
Circuit
NOTE: Unit is equipped with a phase loss/phase reversal control. If
system does not start, check phase of electrical supply.
General Refrigeration Circuit
SYMPTOM
POSSIBLE CAUSE
REMEDY
A. Compressor will
not start.
1. Power off, loose electrical connections or
fuse open.
1. Check disconnect switch, fuses and wiring. Replace parts or repair as
necessary
2. Compressor contactor not closing.
2. Check voltage to contactor coil, transformer, slave relay, system. Replace
parts as necessary.
3. Internal compressor thermal overload open. 3. If compressor is hot, allow 2 hours to cool. See D. below.
4. Compressor defective.
4. Check compressor for electrical failure. Compressor may be seized; check
refrigerant. If necessary, replace compressor.
5. High or low pressure switch open or
defective.
5. If manual reset (high pressure), reset switch. (Switch opens at 400 psi and
will not reset above 250 psi.) If auto reset (low pressure) does not reset and
everything else is OK, replace switch.
B. Compressor
starts but cuts out
on low pressure
(low pressure switch
activates at 8 psig.)
1. Low refrigerant charge.
1. Check refrigerant pressures.
2. Airflow restricted.
2. Check for dirty evaporator coil, dirty filters, dampers closed, iced evaporator
coil, improper belt, check motor amps, check duct design.
3. Restriction in refrigerant line.
3. Check refrigerant pressure, check and adjust thermal expansion valve. If
not functioning properly, check for pressure drop across the filter drier.
4. Defective low pressure switch.
4. Check calibration of switch.
C. Compressor starts
but cuts out on high
pressure switch.
1. Refrigerant overcharge.
1. Check pressures, charge by sub cooling.
2. Condenser fan motor defective.
2. Check fan motor.
3. Condenser coil inlet obstructed or dirty.
3. Check coil and inlet clearances and for possible air recirculation.
4. Air or non-condensables in system.
4. Check high side equalized pressure reading with equivalent outdoor
temperature.
5. Defective high pressure switch.
5. Check calibration of switch.
6. Restriction in discharge or liquid line.
6. Check refrigerant line pressures, check thermal expansion valves.
D. Compressor
cuts out on thermal
overload.
1. Low voltage.
1. Check voltage.
2. Sustained high discharge pressure.
2. Check running amperage and conditions described in I.
3. High suction and discharge pressures.
3. Check thermal expansion valve setting, check for air in system.
4. Defective compressor overload.
4. If compressor is hot, allow compressor to cool for two hours. Recheck for open
circuit.
5. Defective run capacitor.
5. Check run capacitor for compressor and fan motor.
6. Improper refrigerant charge.
6. Check subcooling.
7. Bearings or pistons too tight.
7. Check for low oil level.
8. Allow time for compressor to cool.
8. Check dome temperature of the compressor.
E. Noisy compressor.
1. Refrigerant overcharge.
1. Check pressures and subcooling.
2. Liquid floodback.
2. Check thermal expansion valve setting. Check for refrigerant overcharge.
3. Tubing rattle.
3. Dampen tubing vibration by taping or clamping. Carefully bend tubing away
from contact where possible.
4. Compressor defective.
4. Check internal parts; replace.
F. Noisy unit operation. 1. Blower rotational noise.
1. Check blower, motor and drive for faulty adjustment or noisy bearings, loose
parts, and/or blower out of balance.
2. Air noise.
2. Check ductwork. Air velocity too high.
3. Chattering contactor.
3. Check for adequate control voltage, check for shorts or breaks, check
thermostat, check contact points.
4. Tubing rattle.
4. Dampen by taping or clamping, carefully bend tubing away from contact when
possible.