Reznor MAPSII Series REDA Users Manual User Manual
Page 15
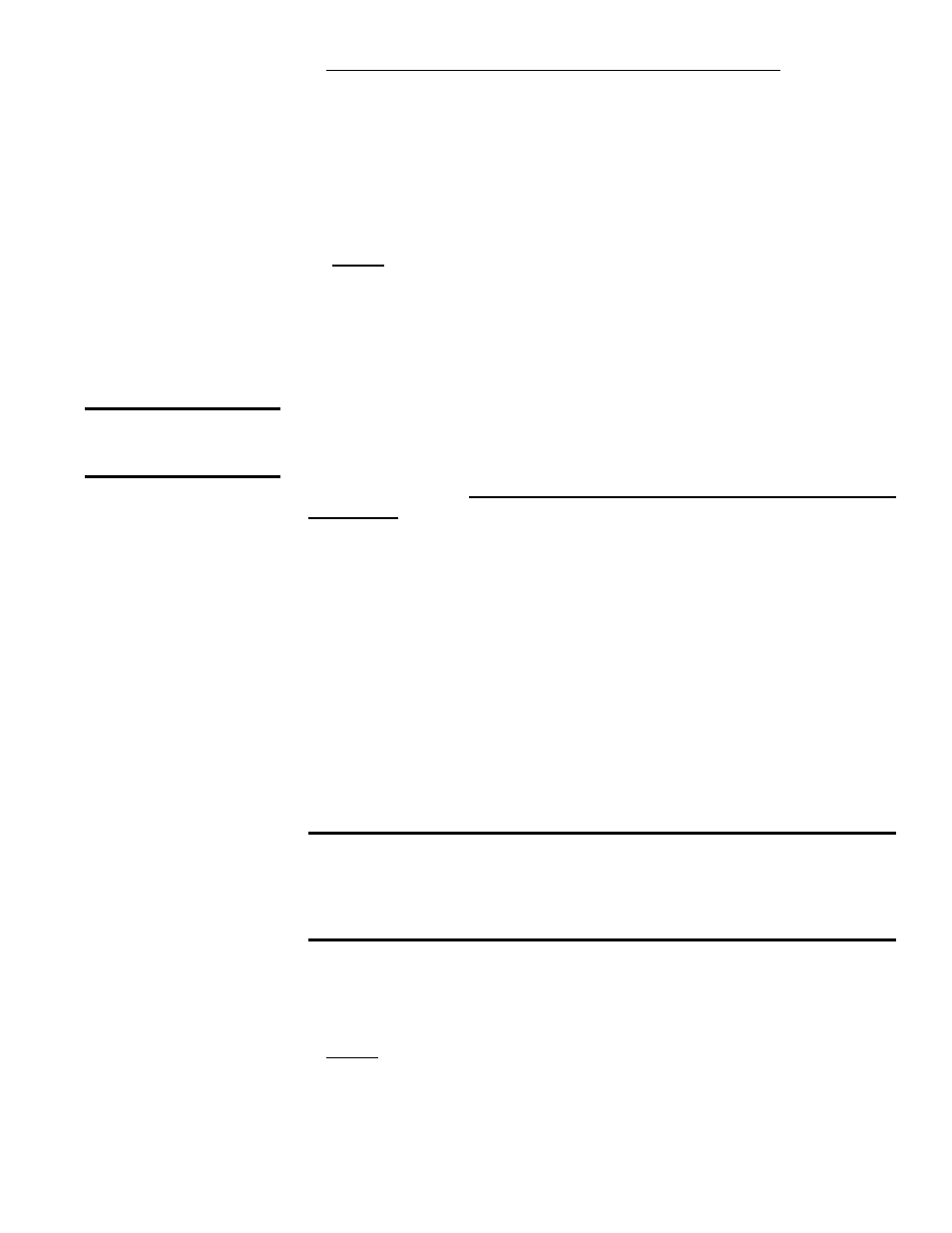
Form RZ-NA O-MAPS II, P/N 209179 R7, Page 15
Step 5. Braze on Suction and Discharge Lines
Flow an inert gas, such as nitrogen (N2)
, through the system at approxi-
mately 2 psig. This will reduce the possibility of oxidation inside the tubing.
Braze on the suction and discharge lines and braze the process tube shut
following the recommendations listed below. NOTE: If the process tube
is to be used for charging the system, it should be brazed shut after
the system has been charged.
If the test for acid in
Step 2 did indicate compressor burnout, do the
following:
a) Install an acid-removing liquid line filter drier. Size he acid-removing filter
drier at least one capacity size larger than normally required for the circuit.
b) Install a temporary filter drier in the suction line. The temporary suction
line drier should be sized properly for the circuit and have a service access
fitting to monitor pressure drop across the drier.
Step 12 includes the remaining procedures required for cleanup of a com-
pressor burnout. Continue to
Step 5.
WARNING: Wearing
eye protection is
recommended.
Brazing Recommendations and Procedures
COPPER TUBING: If additional copper tubing is required, use only clean,
dehydrated refrigeration grade tubing with sealed ends.
BRAZING ALLOYS: CAUTION: Do not use 95/5, 50/50 or 40/60 soft solder
for brazing. Use Sil-Fos or Phos Copper, or similar brazing alloys with high
tensile strength on copper welds only. Weld steel to copper only with silver
brazing alloys.
BRAZING PROCEDURE: Comply with applicable code requirements and fol-
low safe brazing procedures. The manufacturer recommends the following
steps:
a) Exercise extreme care when cutting and forming tubes to keep dirt,
filings, and other contaminants out of the system.
b) Do not use excessive amounts of brazing alloy as some of the
excess may penetrate the joint and enter the system.
c) If flux must be used, take necessary precautions to ensure that the
flux does not enter the system.
d) Use damp cloths or other heat absorbent material to ensure that
the factory brazed joints on the compressor do not become dam-
aged. If
damp cloths are used, take care not to allow moisture to
enter the system.
CAUTION: Do not leave system open to the atmosphere any
longer than minimum required. This applies to all refriger-
ants but is more critical with R407C which uses POE oil. POE
oil is extremely susceptible to moisture absorption.
e) Do not overheat brazed joints as excess heat will cause formation
of copper oxide on the inside wall of the tubing. To aid in avoiding
the formation of copper oxide, flow an inert gas through the sys-
tem, as explained above.
Step 6. Check System for Leaks
After installation is complete, pressurize the system to approximately 75
psig using nitrogen and a few ounces of refrigerant. Check for leaks using
a halide torch, soap bubbles, or an electronic halogen leak detector. When
all connections test satisfactorily, release pressure using proper recovery
procedures, then proceed to the next step.