Combustion air pressure switch setting, Sensor location, Wiring and service – Reznor HRPD (Outdoor Duct Furnaces) Unit Installation Manual User Manual
Page 21
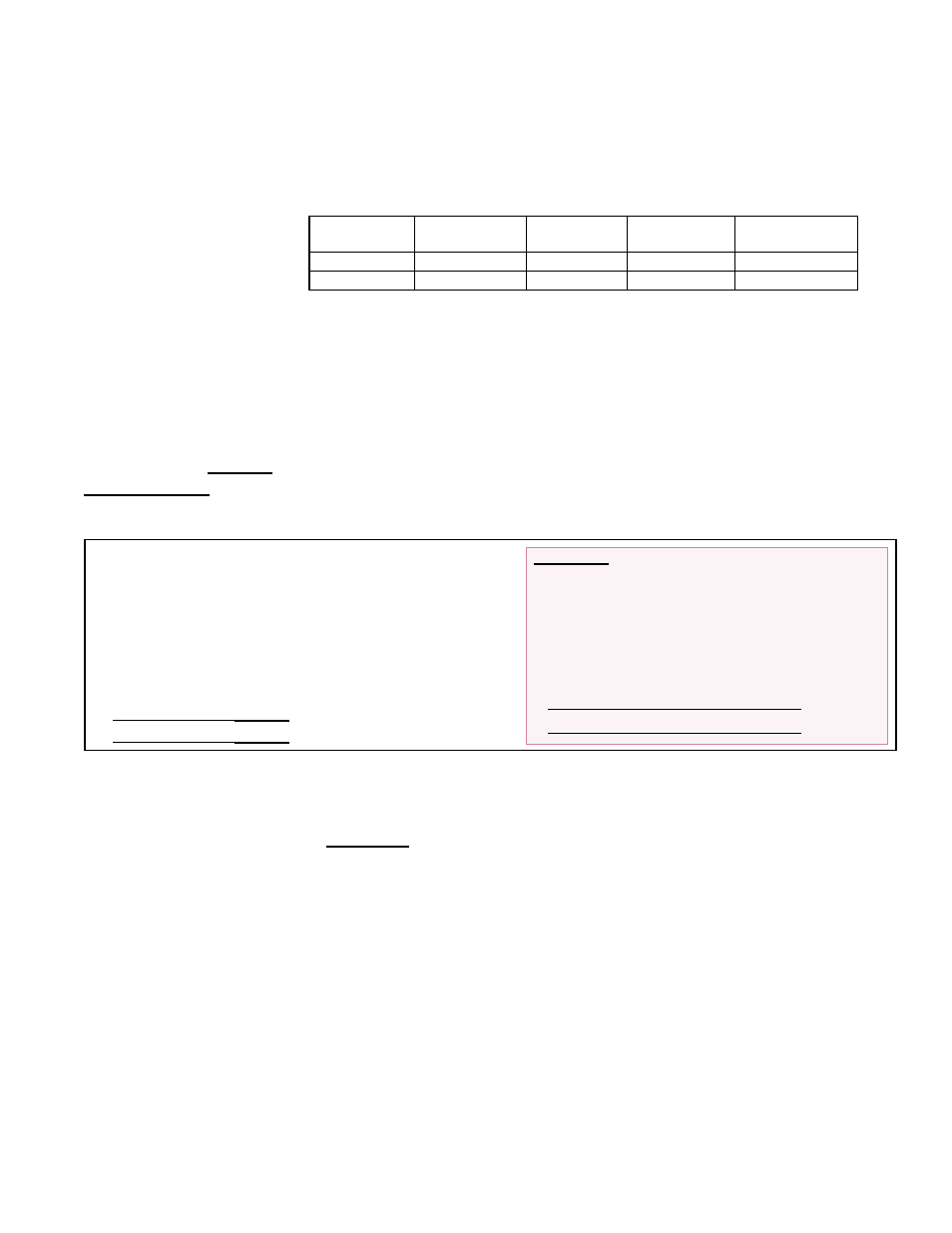
Form I-RP/HRPD, P/N 132210 R14, Page 21
RP with AG39
or AG40
HRPD with
AG41 or AG42
Startup
Cold
Equilibrium at
Full Rate
Factory Setting
Sizes 125-225 Sizes 250 - 400 -1.3" w.c.±0.2 -1.05" w.c.±0.1 -0.58" w.c.±0.05
Sizes 250-400 Sizes 500 - 800 -1.2" w.c.±0.2 -0.95" w.c.±0.1 -0.58" w.c.±0.05
Combustion Air
Pressure Switch
Setting
This uniquely designed modulation system requires combustion air pressure settings
different from the standard system. The approximate settings for the combustion air
proving switch at sea-level operation are:
Calculate the Setpoints with Two Furnace Sections
- Use the following formulas to calculate the controller
settings for Heat Stage 2 and Heat Stage 3 in a system
with two furnace sections.
T
SP
= Setpoints of Heat Stage Controllers (T
SP2
and T
SP3
)
T
SA
= Desired Supply Air Temperature
T
D
= Design (minimum) Entering Air Temperature
Formulas for two furnace sections:
Setpoint for Heat
Stage 2: T
SP2
= T
SA
- 0.46 (T
SA
- T
D
)
Setpoint for Heat
Stage 3: T
SP3
= T
SA
- 0.73 (T
SA
- T
D
)
Set Heat Stage
Controllers - applies
to HRPD with Option
AG41 or AG42
Model HRPD units with Option AG41 and AG42 have “heat stage controllers” that
control operation of the "two-stage" furnace based on outside air temperature
setpoints. Proper setpoints are important to ensure the modulating furnace ("Heat
Stage 1") is always in control and avoids cycling
. The proper setpoint for each
controller must be determined from basic design information. Follow the steps and
example to determine appropriate setpoints. Follow the instructions to locate and set
the controllers.
EXAMPLE : 3600 CFM, Power vented, 100%
Outside Air, -10°F Outdoor Winter Design, 75°F
Desired Supply Air
T
SP2
= 75
- [.46 x (75
- (-10))] = 75 - (.46 x 85) =
35.9
T
SP3
= 75
- [.73 x (75
- (-10))] = 75 - (.73 x 85) =
12.9
Set Stage Heat #2 Controller to 36°F
Set Stage Heat #3 Controller to 13°F
Locate and Set the
Heat Stage Controllers
1. In the inlet air section, locate the heat stage controllers. The same type of
controller may also be used as the optional high ambient limit control (Option
BN2) and as the mixed air controller that is part of air control Options AR12, AR13,
AR15, and AR16). Identify the controllers marked Heat #2 and Heat #3.
2 Furnaces (Model HRPD) - Identify controllers marked Heat #2 and Heat #3 .
2. Adjust each controller to the setpoint as determined in the calculation.
Sensor Location
The duct temperature sensor and mixing tube are shipped loose for field installation
in the dicharge duct. See Paragraph 6.3.5 for instructions on locating the sensor in
the ductwork.
The sensor for Opiton AG40 and AG42 is field suppleid. Follow the guidelines in Para-
graph 6.3.5 and the manufacturer's instrucitons.
the gas pressure to 1.1" w.c., the primary gas pressure switch in the manifold activates
the gear motor that controls the bypass damper in the venter/combustion air system.
The bypass damper opens diverting some of the incoming air directly into the flue duct,
reducing airflow through the burner. Safety switches monitor the position of the bypass
damper. When the gas pressure increases above 1.1" w.c., the bypass damper closes.
Wiring and Service
For wiring, consult the wiring diagram attached to the furnace. All wires in the
electrical box connecting the modulation controls must have a temperature rating of
150°C.
This is a unique system which includes custom-built components and custom settings.
If service is required, follow the general troubleshooting guide on page 28 and the
special troubleshooting guide on page 22.
Computer Controlled
Electronic Modulation
between 20-28%,
Options AG40 and
AG42
The heater functions and is equipped in the same way as for Option AG39 except that
with computer control the temperatures are selected through the field-supplied soft-
ware and there is no temperature selector or duct sensor.
With this option the furnace is equipped with a Maxitrol signal conditioner (
FIGURE
14B) which accepts an input signal of either 4-20 milliamps or 0-10 volts from a cus-
tomer-supplied control device such as a computer. With the dip switches on the condi-
tioner in the "on" positions, the conditioner accepts a 4-20 milliamp signal. In the "off"
positions, the conditioner accepts a 0-10V signal. The conditioner converts the signal
to the 0 to 20 volt DC current required to control the modulating valve.