Potter Releasing Systems User Manual
Page 33
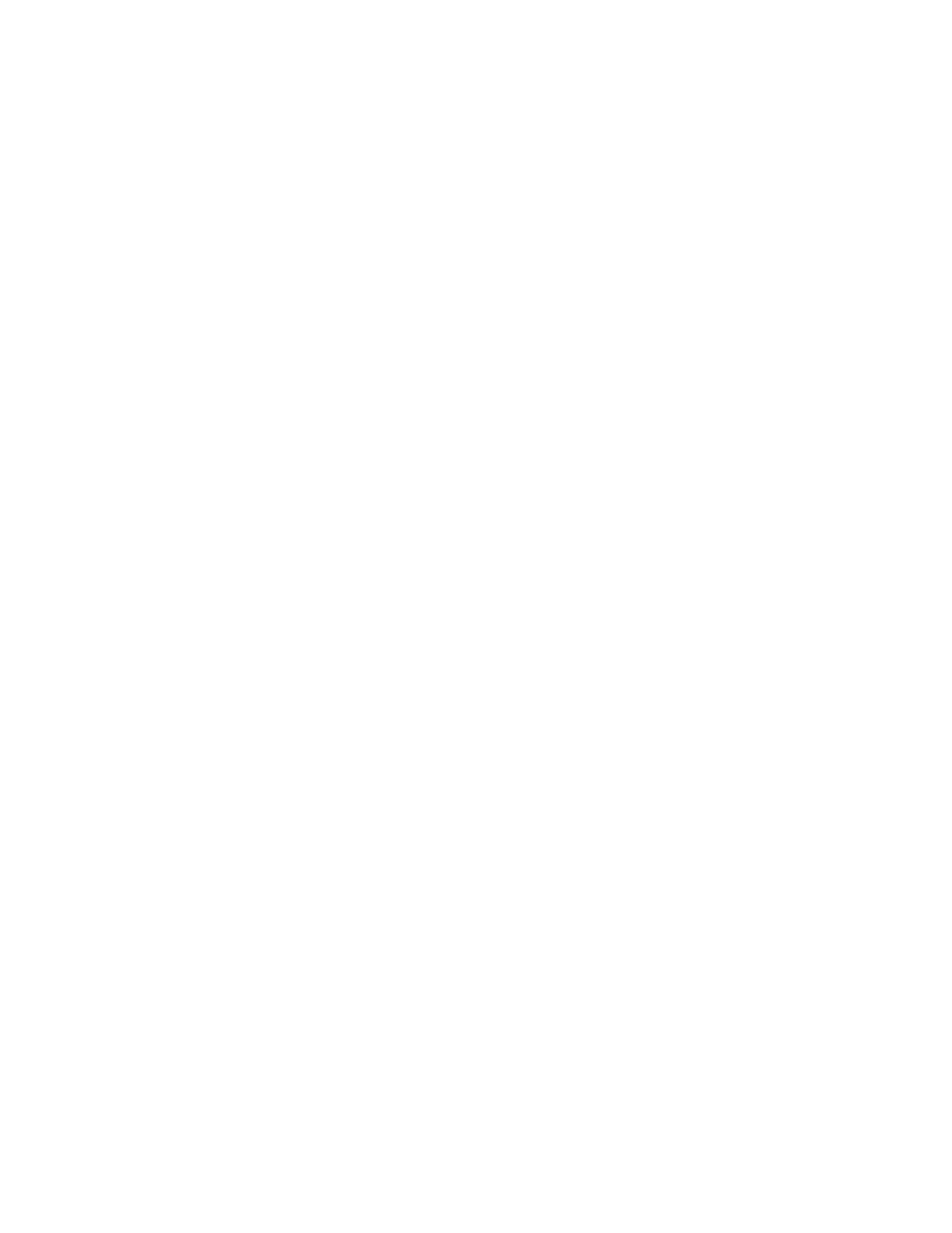
33
Pressure Type
Pressure type flow switches can be installed on wet systems that have an alarm check valve. They must be
installed on dry sprinkler systems. Pressure switches should only be installed with the threaded connection down.
On wet systems, the flow switch should have a retard. This can be accomplished one of two ways:
One is to install a pressure switch on top of a retard chamber. A retard chamber is a metal container capable
of holding a few gallons of water. When a water surge happens, the chamber fills with water and absorbs the
pressure before the pressure switch trips. There is a small drip valve at the bottom of the chamber to allow the
water to drain out before the next surge. Retard chambers require periodic maintenance to prevent the drip valve
from becoming clogged with rust or scale and causing false alarms. The time delay also varies depending on
how fast the water fills the chamber.
The other way is to install a pressure switch that has a retard built into it. It is installed in place of the retard
chamber. This eliminates the cost of the retard chamber and the time consuming maintenance associated with it.
This type of switch also provides a much more accurate retard time.
Dry sprinkler systems must use a pressure type flow switch. Vane type flow switches are not permitted on dry
systems per NFPA13 6.9.2.4. Since dry systems are not subject to water surges, they do not require the use of a
retard. A pressure type flow switch would be installed in the alarm port of the dry pipe valve.
Since pressure type flow switches are installed on the alarm port of the valves, where there is no water or air
pressure under normal conditions, they can be installed or replaced without disabling the sprinkler system.
Air Pressure Supervisory Switches
Dry sprinkler systems should have an air pressure supervisory switch installed. Per NFPA72 5.15.2.2, this
switch would trip if the air pressure dropped 10 psi below the normal system pressure, or increased 10 psi above
normal. The purpose of low air supervision is to prevent accidental tripping of the system due to compressor
failure. High pressure supervision prevents the system from having too much air which would increase the time
it takes to bleed enough pressure off the system to allow the dry pipe valve to trip.
Supervisory air pressure is typically about 40 psi. The supervisory pressure switch should be set to operate at
10 psi below or above the normal system pressure. The Potter PS40-2 is factory set to trip at 30 psi for low
pressure and 50 psi for high pressure.
Low pressure switches should be installed in line with a bleeder valve and a pressure gauge. A bleeder valve
is a valve with a small orifice in it. The purpose of the valve is to exhaust the pressure between the bleeder
valve and the pressure switch. This allows testing of the switch without any possibility of an accidental tripping
of the dry pipe valve. It also speeds up the testing process since such a small amount of air is being released.