Flintec MCS-64 CANbus User Manual
Page 31
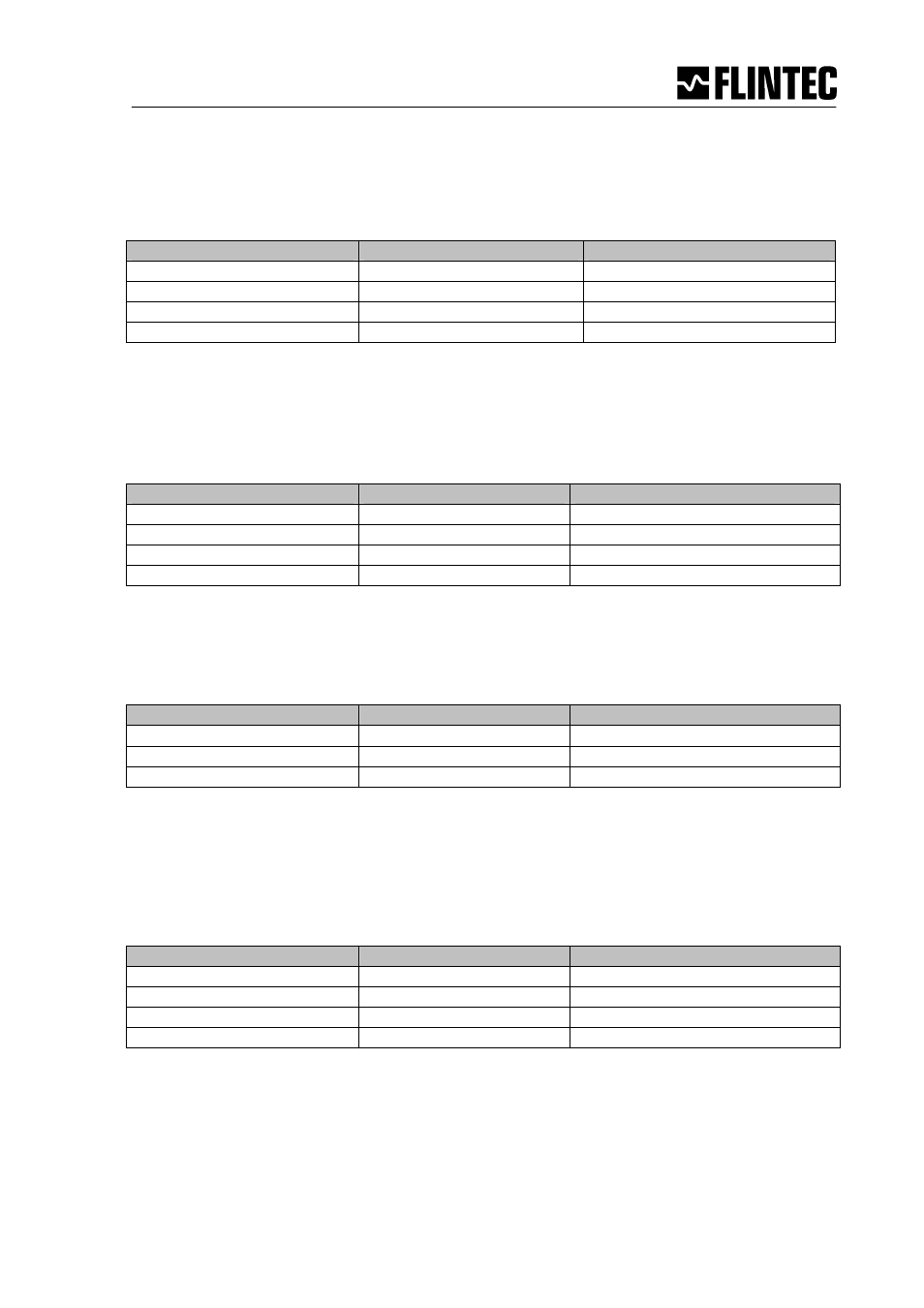
Manual MCS-64 Page 31
DS
Display step size
[ 2300sub0C ]
This command allows the output to step up or down by a unit other than 1. Permitted
values are 1, 2, 5, 10, 20, 50, 100 and 200.
Master (PC / PLC) sends
Device responds
Result
DS S+00002
Request : display step size 2
CE
E+00017
(example)
Request: TAC-counter CE 17
CE_17 OK
Calibration sequence active
DS_50 OK
Setting: DS = 50
DP
Set decimal point position
[ 2300sub0B ]
This command allows the decimal point to be positioned anywhere between leftmost and
rightmost digits of the 5-digit output result. Position 0 means no decimal point.
Master (PC / PLC) sends
Device responds
Result
DP P+00002
Request : position of dec. point
CE
E+00017
(example)
Request: TAC-counter CE 17
CE_17 OK
Calibration sequence active
DP_0 OK
Setting: no decimal point
CZ
Set calibration zero point
[ 2300sub0A ]
This is the reference point for all weight calculations, and is subject to TAC control.
Master (PC / PLC) sends
Device responds
Result
CE
E+00017
(example)
Request: TAC-counter CE 17
CE_17 OK
Calibration sequence active
CZ OK
Zero point set
Factory default: approx. 0 mV/V input signal
CG
Set calibration gain (span) value
[ 2300sub04 ]
This is the reference point for calibration under load, and is subject to TAC control.
Permitted values are 1…262143.
Master (PC / PLC) sends
Device responds
Result
CG G+20000
Request : span 20000d
CE
E+00017
(example)
Request: TAC-counter CE 17
CE_17 OK
Calibration sequence active
CG_50000 OK
Setting: span 50000d
For calibration an input signal near the display maximum (CM) will give the best system
performance. The minimum calibration load of at least 20% is recommended.
Factory default: 200000 d = 2.000 mV/V input signal = 20 kg