04 hmc-410 setup checklist, 04 hmc-410 setup checklist -12, Hmc-410 – Tweco HMC-410 User Manual
Page 52: 03 system setup
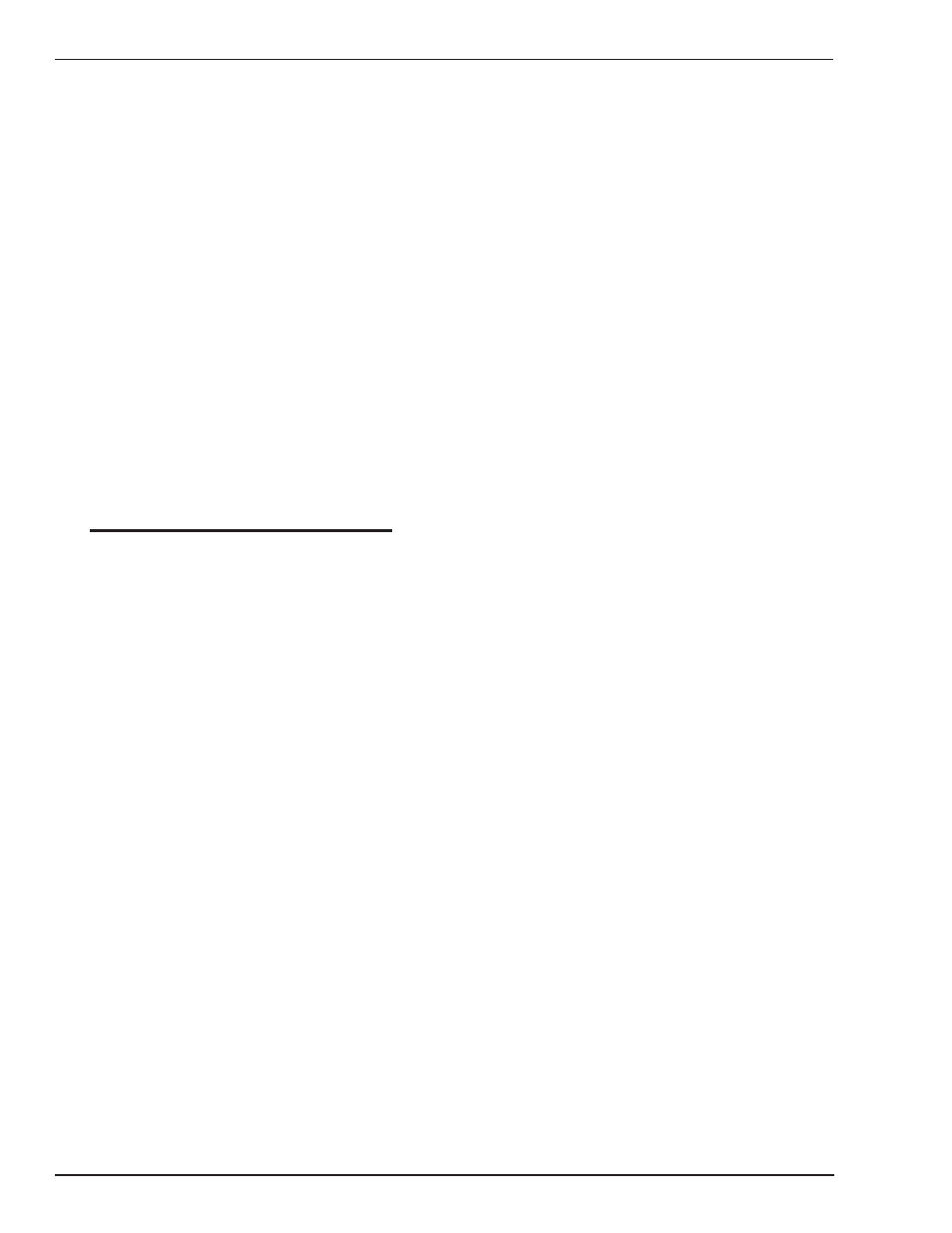
HMC-410
4-10
July 27, 2005
4.03 System Setup
In order to properly utilize the HMC-410 control panel, it
must be configured correctly for the application and the
equipment it is to be used with. There are several items
which need to be considered before the control panel can
be used. They include:
Fixturing... how the control panel should interact?
Power Source... what type of power source is used?
Control Panel Setup... desired configuration?
Process... Semiautomatic or Automatic?
Follow the HMC-410 Setup Checklist found at the end of
this section when initially configuring the panel. Standard
software softswitches are shown on this configuration
table.
Table 4-4 contains the various settings used for the various
power source configurations. Also included is special
setup for semiautomatic operation.
NOTES:
K. The English/Metric Select should be set to user
standards or discretion.
L. The fault abort enable can be a function of many
factors. In many instances, when the panel is
configured to a fixture, that fixture requires that the
weld proceed through completion even if there is an
error in the weld. Alternatively, some situations dictate
that once there is an error, the process should stop
and the error should be rectified. This switch should
be ON to enable the fault abort and will be set to the
discretion of the user for their procedure.
M. The program delay enable can be used if required by
the procedure.
N. Trim Enable is up to the welder. Typically, to get a weld
fine tuned, this would initially be ON to enable the trim
function. Then, depending on the consistency of the
process, this function could be left on or disabled.
O. Since the arc hours should be set to 0 out of the box,
this switch should be OFF as it is not necessary to
clear the arc hours.
P. The weld sub segment enable can depend upon many
factors. If in an automatic application, and there is a
need for various weld segments in a continuous weld,
then it should be ON. Otherwise, it should be OFF. For
semiautomatic applications, and the optional front
panel switches are available, then this function should
also be OPEN, to be disabled by the front panel switch.
If the front panel options are not available, then this
switch will be set to the discretion of the welder.
Q. For automatic applications, this switch should be set
OFF to disable it. This function should be enabled (set
to HAr) for semiautomatic applications used with the
optional front panel switches, to be disabled by the
front panel switch. If the front panel options are not
available, then this switch would be set to the
discretion of the welder.
By following this checklist, the control panel can be set
up for use. Care should be taken to follow static safe
procedures when handling PCBs. Also, when buttoning
up the panel, all hardware should be used since it is critical
for the integrity of the panel.