Lenze MCH Series User Manual
Page 73
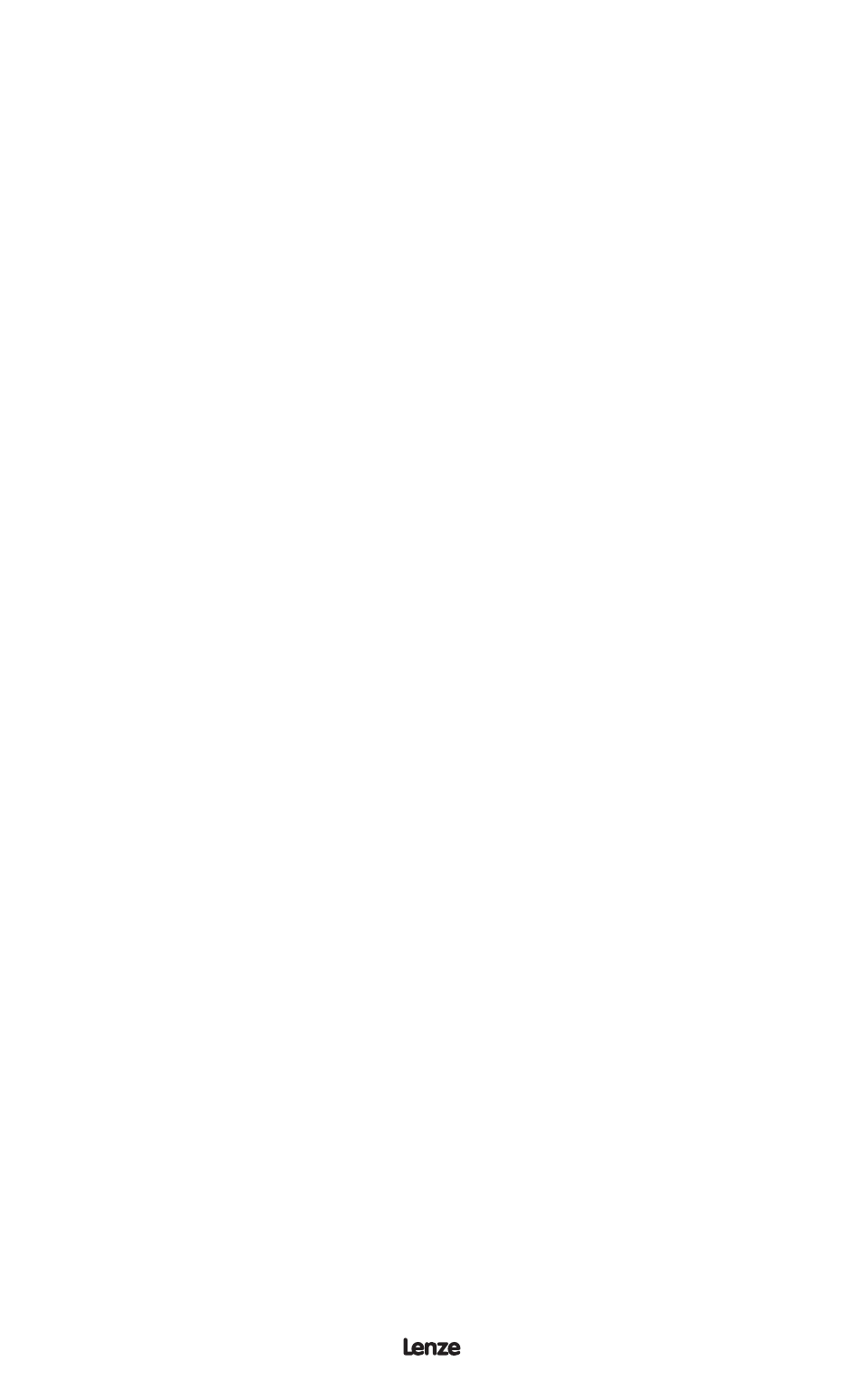
13435744_EDBMH01_v13
69
76
FEEDBACK @ MAX
This parameter should be set to the value of the process variable that corresponds to
the maximum transducer feedback signal (10 VDC or 20 mA).
Example:
A 0-100 psi transducer outputs 4 mA at 0 psi and 20 mA at 100 psi. Set
FEEDBACK @ MIN to 0.0 PSI and set FEEDBACK @ MAX to 100.0 PSI
(this assumes that Parameter 31 - UNITS is set to pid: PSI, and Parameter
33 - UNITS DECIMAL is set to XXX.X).
NOTE:
If a reverse-acting feedback device is being used, FEEDBACK @ MIN
should be set to the maximum process variable value, and FEEDBACK @
MAX should be set to the minimum process variable value.
77
PROPOR. GAIN (PROPORTIONAL GAIN)
The Proportional Gain setting represents the speed command output (in % of maximum
speed) that results from each 1% of error (1% of Parameter 75 - FEEDBACK @ MIN or
76 - FEEDBACK @ MAX, whichever is larger).
Example: If PROPOR. GAIN is programmed for 5%, and the error (difference
between setpoint and feedback) is 10%, the speed command output of the
Proportional term is 50% (10 x 5 = 50) of maximum speed.
78
INTEGRAL GAIN
The Integral Gain setting represents the ramp rate of the speed command output (in %
of maximum speed per second) that results from each 1% of error.
Example:
If INTEGRAL GAIN is programmed for 0.5 seconds, and the error is 5%,
the rate of rise of the speed command output from the Integral term is 2.5%
(0.5 x 5 = 2.5) of maximum speed per second.
79
DIFF. GAIN (DIFFERENTIAL GAIN)
The Differential Gain setting represents the speed command output (in % of maximum
speed) that results from each 1% per second change in the error.
Example:
If DIFF. GAIN is programmed for 5 seconds, and the error is increasing at
2% per second, the speed command output of the Differential term is 10%
(5 x 2 = 10) of maximum speed.
NOTE:
Differential gain is used as a “shock-absorber” to dampen overshoots in
fast-acting systems. However, it can be very sensitive to “noise” on the
feedback signal and to digitizing errors, so it must be used with caution.
80
PID ACCEL (PID ACCEL/DECEL)
This parameter sets the acceleration and deceleration rate of the setpoint reference into
the PID unit. When the setpoint changes, this function will “filter” the input to the PID
unit by ramping the setpoint reference from the previous value to the new value. This
will help prevent overshoots that can occur when the PID control attempts to respond
to step changes in setpoint, resulting in smoother operation. If PID ACCEL is set to 0.0
seconds, it is effectively disabled.