6 theory, 1 description of ac motor operation – Lenze MCH Series User Manual
Page 20
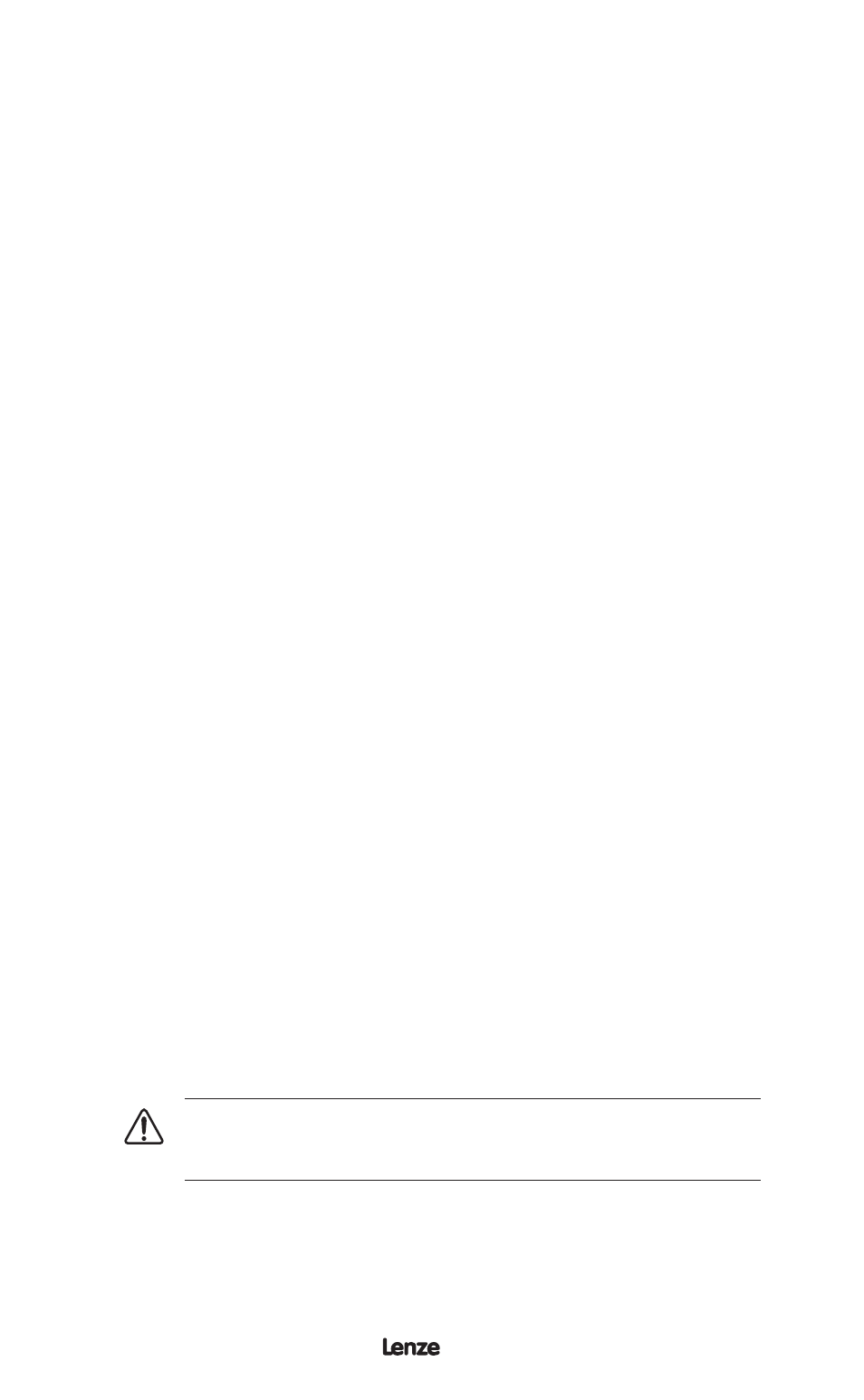
16
13435744_EDBMH01_v13
6 THEORY
6.1
DESCRIPTION OF AC MOTOR OPERATION
Three phase AC motors are comprised of two major components, the stator and the
rotor. The stator is a set of three electrical windings held stationary in the motor housing.
The rotor is a metal cylinder, fixed to the motor drive shaft, that rotates within the stator.
The arrangement of the stator coils and the presence of three phase AC voltage give
rise to a rotating magnetic field that drives the rotor. The speed at which the magnetic
field rotates is known as the synchronous speed of the motor. Synchronous speed is a
function of the frequency at which the voltage is alternating and the number of poles in
the stator windings.
The following equation gives the relation between synchronous speed, frequency, and
the number of poles:
Ss = 120 f/p
Where:
Ss = Synchronous speed (rpm ),
f = frequency (Hz),
p = number of poles
In three phase induction motors the actual shaft speed differs from the synchronous
speed as load is applied. This difference is known as “slip”. Slip is commonly expressed
as a percentage of synchronous speed. A typical value is three percent at full load.
The strength of the magnetic field in the gap between the rotor and stator is proportional
to the amplitude of the voltage at a given frequency. The output torque capability of the
motor is, therefore, a function of the applied voltage amplitude at a given frequency.
When operated below base (rated) speed, AC motors run in the range of “constant
torque”. Constant torque output is obtained by maintaining a constant ratio between
voltage amplitude (Volts) and frequency (Hertz). For 60 Hz motors rated at 230, 460,
and 575 Vac, common values for this V/Hz ratio are 3.83, 7.66, and 9.58 respectively.
Operating with these V/Hz ratios generally yields optimum torque capability. Operating
at lower ratio values results in lower torque and power capability. Operating at higher
ratio values will cause the motor to overheat. Most standard motors are capable of
providing full torque output from 3 to 60 Hz. However, at lower speeds, where motor
cooling fans become less effective, supplemental cooling may be needed to operate at
full torque output continuously.
If the frequency applied to the motor is increased while the voltage remains constant,
torque capability will decrease as speed increases. This will cause the horsepower
capability of the motor to remain approximately constant. Motors run in this mode when
operated above base speed, where drive output voltage is limited by the input line
voltage. This operating range is known as the “constant horsepower” range. The typical
maximum range for constant horsepower is about 2.3 to 1 (60 to 140 Hz). The following
torque vs. frequency diagram depicts the characteristics of a typical AC induction motor
with a 60 Hz base speed.
WARNING!
Consult motor manufacturer before operating motor and/or driven
equipment above base speed.