Step 1 setting the jumpers and dip switches, Analog dc outputs (optional), Inputs – Red Lion DLC User Manual
Page 4: Analog output 2 jumpers analog output 1 jumpers, Emc installation guidelines, Serial dip switch settings
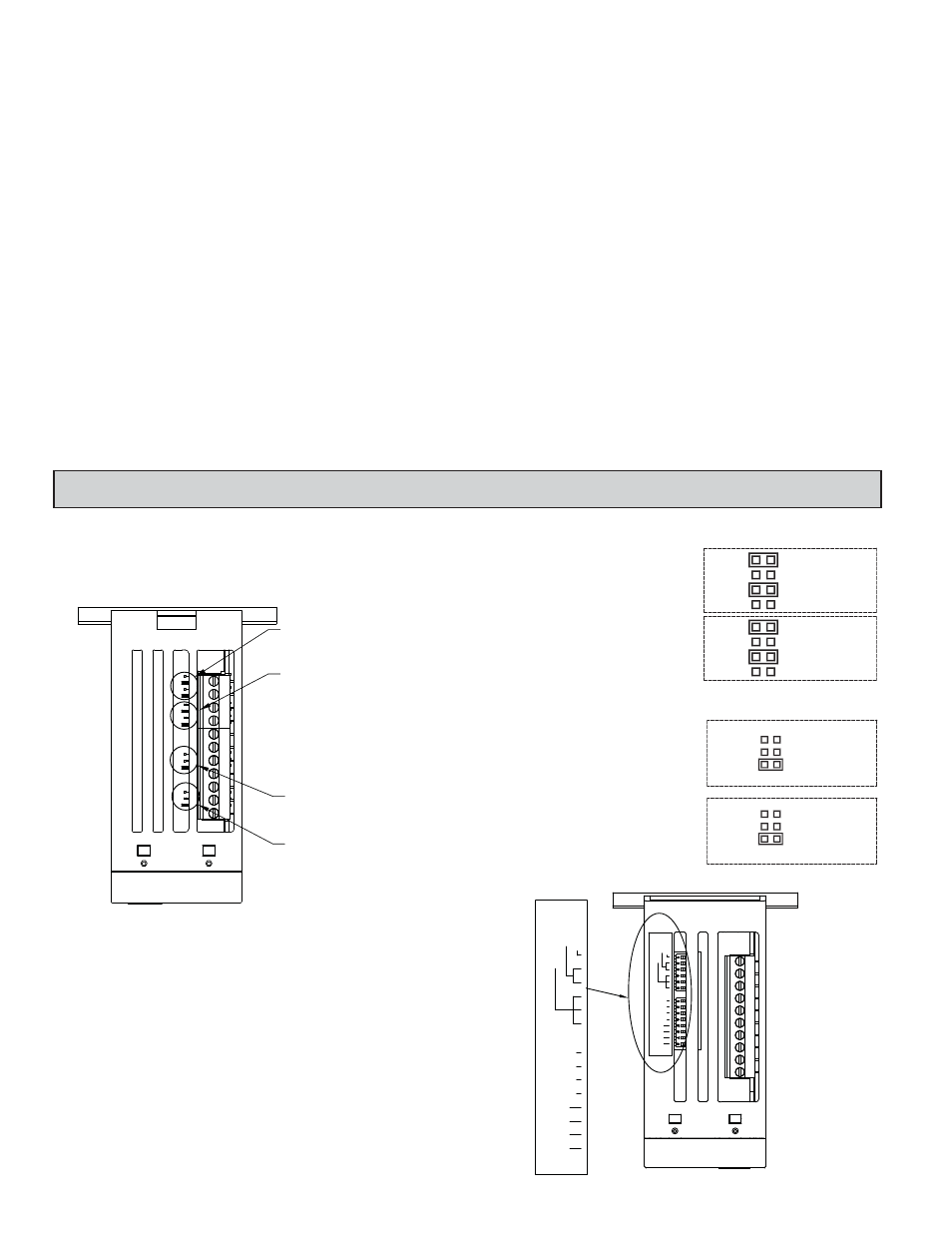
4
STEP 1 SETTING THE JUMPERS AND DIP SWITCHES
The jumpers are accessible from the bottom of the controller. Needle-nose
pliers are needed to remove the jumpers. They should be set prior to installation.
To insure proper operation, the jumpers must match the controller software
configuration.
ANALOG DC OUTPUTS (OPTIONAL)
Analog Output 1 and Analog Output
2 can be configured for voltage (V) or
current (I), independent of each other.
Both V/I + and V/I - jumpers of the
same channel must be set for the same
type of output signal.
INPUTS
Channel A and Channel B can be
configured independent of each other.
Jumper position can be ignored for
thermocouple and millivolt inputs.
I2-
V2+
I2-
V2+
I1-
V1+
I1-
V1+
Analog
Output 2
Jumpers
Analog
Output 1
Jumpers
10V
20mA
RTD
10V
20mA
RTD
Channel A
Input
Channel B
Input
Channel B
Input Jumpers
Channel A
Input Jumpers
Analog Output 2
Jumpers (current)
Analog Output 1
Jumpers (current)
(RTD)
(As set from factory)
EMC INSTALLATION GUIDELINES
Although this controller is designed with a high degree of immunity to
Electromagnetic Interference (EMI), proper installation and wiring methods
must be followed to ensure compatibility in each application. The type of the
electrical noise, source or coupling method into the controller may be different
for various installations. The controller becomes more immune to EMI with
fewer I/O connections. Cable length, routing, and shield termination are very
important and can mean the difference between a successful or troublesome
installation. Listed are some EMC guidelines for successful installation in an
industrial environment.
1. Use shielded (screened) cables for all Signal and Control inputs. The shield
(screen) pigtail connection should be made as short as possible. The
connection point for the shield depends somewhat upon the application.
Listed below are the recommended methods of connecting the shield, in order
of their effectiveness.
a. Connect the shield only at the DIN rail where the controller is mounted to
earth ground (protective earth).
b. Connect the shield to earth ground at both ends of the cable, usually when
the noise source frequency is over 1 MHz.
c. Connect the shield to common of the controller and leave the other end of
the shield unconnected and insulated from earth ground.
2. Never run Signal or Control cables in the same conduit or raceway with AC
power lines, conductors feeding motors, solenoids, SCR controls, and
heaters, etc. The cables should be run through metal conduit that is properly
grounded. This is especially useful in applications where cable runs are long
and portable two-way radios are used in close proximity or if the installation
is near a commercial radio transmitter.
3. Signal or Control cables within an enclosure should be routed as far away as
possible from contactors, control relays, transformers, and other noisy
components.
4. In extremely high EMI environments, the use of external EMI suppression
devices, such as ferrite suppression cores, is effective. Install them on Signal
and Control cables as close to the controller as possible. Loop the cable
through the core several times or use multiple cores on each cable for
additional protection. Install line filters on the power input cable to the
controller to suppress power line interference. The following EMI suppression
devices (or equivalent) are recommended:
Ferrite Suppression Cores for signal and control cables:
Fair-Rite # 0443167251 (Red Lion Controls # FCOR0000)
TDK # ZCAT3035-1330A
Steward # 28B2029-0A0
Line Filters for input power cables:
Schaffner # FN2010-1/07 (Red Lion Controls # LFIL0000)
Schaffner # FN670-1.8/07
Corcom # 1 VR3
Note: Reference manufacturer’s instructions when installing a line filter.
5. Long cable runs are more susceptible to EMI pickup than short cable runs.
Therefore, keep cable runs as short as possible.
6. Switching of inductive loads produces high EMI. Use of snubbers across
inductive loads suppresses EMI.
Snubber: Red Lion Controls # SNUB0000.
SERIAL DIP SWITCH SETTINGS
The DLC Serial Communications Settings can be set via DIP Switches or
through the serial communications port (software selectable). The software
selectable serial settings method using the serial communications port must be
set using “RLCPRO” or another software program to write to the DLC Modbus
registers (40401-40407). When using the DIP switches to configure the serial
settings, the Modbus mode is limited to “RTU” mode only.
SW
A
BAUD RA
TE
P
ARITY
DEF
AUL
T
M2802X
SWB: ADDRESS
X32
X128
X64
X4
X16
X8
X1
X2
M2802X
X64
X32
SWB: ADDRESS
X4
X1
X2
X16
X8
X128
SW
A
DEF
A
UL
T
P
A
RITY
BAUD RA
TE