Modbus information, Manual tuning, Modbus supported function codes – Red Lion DLC User Manual
Page 20
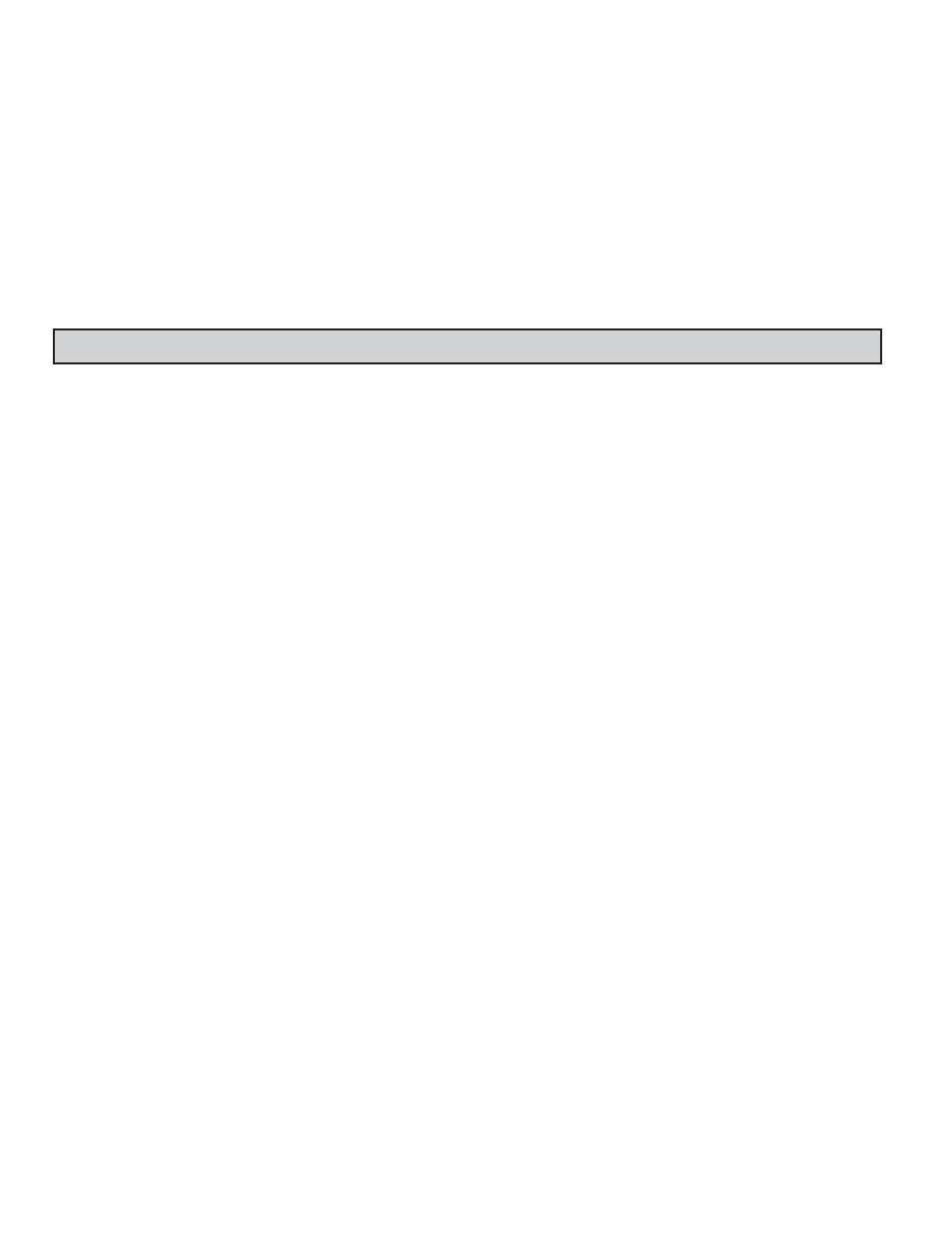
20
MANUAL TUNING
A chart recorder or data logging device is necessary to measure the time
between process cycles. This procedure is an alternative to the controller’s
Auto-Tune function. It will not provide acceptable results if system problems
exist. This procedure should be performed by directly accessing the controller’s
registers. The register numbers correspond to (Channel A/Channel B).
1. Set the Proportional Band (40007/40023) to 10.0% for temperature inputs
and 100.0% for process inputs.
2. Set both the Integral Time (40008/40024) and Derivative Time (40009/40025)
to 0 seconds.
3. Set the Output Dampening Time (40121/40221) to 0 seconds.
4. Set the Output Cycle Time (40116/40216) to no higher than one-tenth of the
process time constant (when applicable).
5. Place the controller in Manual Control Mode (40041/40049) and adjust the
Output Power (40005/40021) to drive the process value to the Setpoint value.
Allow the process to stabilize after setting the Output Power.
6. Place the controller in Automatic Control Mode (40041/40049). If the process
will not stabilize and starts to oscillate, set the Proportional Band two times
higher and go back to Step 5.
7. If the process is stable, decrease Proportional Band setting by two times and
change the setpoint value a small amount to excite the process. Continue with
this step until the process oscillates in a continuous nature.
8. Fix the Proportional Band to three times the setting that caused the oscillation
in Step 7.
9. Set the Integral Time to two times the period of the oscillation.
10. Set the Derivative Time to one-eighth (0.125) of the Integral Time.
11. Set the Output Dampening Time to one-fortieth (0.025) the period of the
oscillation.
MODBUS INFORMATION
The remaining sections of this bulletin list information for MODBUS conformity with DLC registers and coils data.
MODBUS SUPPORTED FUNCTION CODES
FC01: Read Coils
1. Valid coil addresses are 1-33.
2. All coils can be requested.
3. Block starting point can not exceed coil 33.
FC05: Force Single Coil
1. Valid write (force) coil addresses are 1-4, 10-13, 15-16, 22-25, 27-33.
2. HEX <8001> is echoed back for a request to write to a read only coil, to
indicate that the coil did not change.
FC15: Force Multiple Coils
1. Valid write (force) coil addresses are 1-4, 10-13, 15-16, 22-25, 27-33.
2. Block starting point can not exceed coil 33.
3. If a multiple write includes read only coils, then only the write coils will
change.
FC03: Read Holding Registers
1. Valid register addresses are 40001-40032, 40041-40046, 40049-40053,
40065-40070, 40073-40078, 40100-40122, 40131-40143, 40198-40222,
40231-40243, 40301-40308, 40309-40316, 40321-40327, 40401-40407,
40421-40427, 40501-40505, 40601-40660, 40701-40760, 41001-41010,
41101-41116.
2. Up to 32 registers can be requested at one time.
3. Block starting point can not exceed the register boundaries.
4. HEX <8000> is returned in registers beyond the boundaries.
5. Holding registers are a mirror of Input registers.
FC06: Preset Single Register
1. Valid write (preset) register addresses are 40002-40005, 40007-40011, 40013,
40015-40016, 40018-40021, 40023-40027, 40029, 40031-40032, 40041-
40042, 40044, 40046, 40049-40050, 40052-40053, 40065, 40068-40070,
40073, 40076-40078, 40100-40122, 40131-40143, 40198-40222, 40231-
40243, 40301-40316, 40321-40327, 40401-40407, 40421-40427, 40501-
40505, 40601-40660, 40701-40760, 41101-41116.
2. HEX <8001> is echoed back that the register did not change during the
request to write to a read only register.
3. If the write value exceeds the register limit (see Register Table), then that
register value changes to its high or low limit. It is also returned in the
response.
FC16: Preset Multiple Registers
1. Valid write (preset) register addresses are are 40002-40005, 40007-40011,
40013, 40015-40016, 40018-40021, 40023-40027, 40029, 40031-40032,
40041-40042, 40044, 40046, 40049-40050, 40052-40053, 40065, 40068-
40070, 40073, 40076-40078, 40100-40122, 40131-40143, 40198-40222,
40231-40243, 40301-40316, 40321-40327, 40401-40407, 40421-40427,
40501-40505, 40601-40660, 40701-40760, 41101-41116.
2. No response is given with an attempt to write to more than 32 registers at a
time.
3. Block starting point can not exceed the read and write boundaries.
4. If a multiple write includes read only registers, then only the write registers
will change.
5. If the write value exceeds the register limit (see Register Table), then that
register value changes to its high or low limit.
FC04: Read Input Registers
1. Valid register addresses are 30001-30032, 30041-30046, 30049-30053,
30065-30070, 30073-30078, 30100-30122, 30131-30143, 30198-30222,
30231-30243, 30301-30308, 30309-30316, 30321-30327, 30401-30407,
30421-30427, 30501-30505, 30601-30660, 30701-30760, 31001-31010,
31101-31116.
2. Up to 32 registers can be requested at one time.
3. Block starting point can not exceed register boundaries.
4. HEX <8000> is returned in registers beyond the boundaries.
5. Input registers are a mirror of Holding registers.
FC08: Diagnostics
The following is sent upon FC08 request:
Module Address, 08 (FC code), 04 (byte count), “Total Comms” count,
“Total Good Comms” count, checksum of the string
“Total Comms” is the total number of messages received that were addressed to
the DLC. “Total Good Comms” is the total messages received by the DLC
with good address, parity and checksum. Both counters are reset to 0 upon
response to FC08, on power-up, and when Total Comms register rolls over.
FC17: Report Slave ID
The following is sent upon FC17 request:
Unit Address, 17 (FC code), RLC-DLCxx000 (model number), 0200 (for code
version 2.00), 32 (number of read supported registers), 32 (number of writes
supported registers), 16 (number of registers available for GUID/Scratch pad
memory), checksum of the string.