Dlc register table – Red Lion DLC User Manual
Page 23
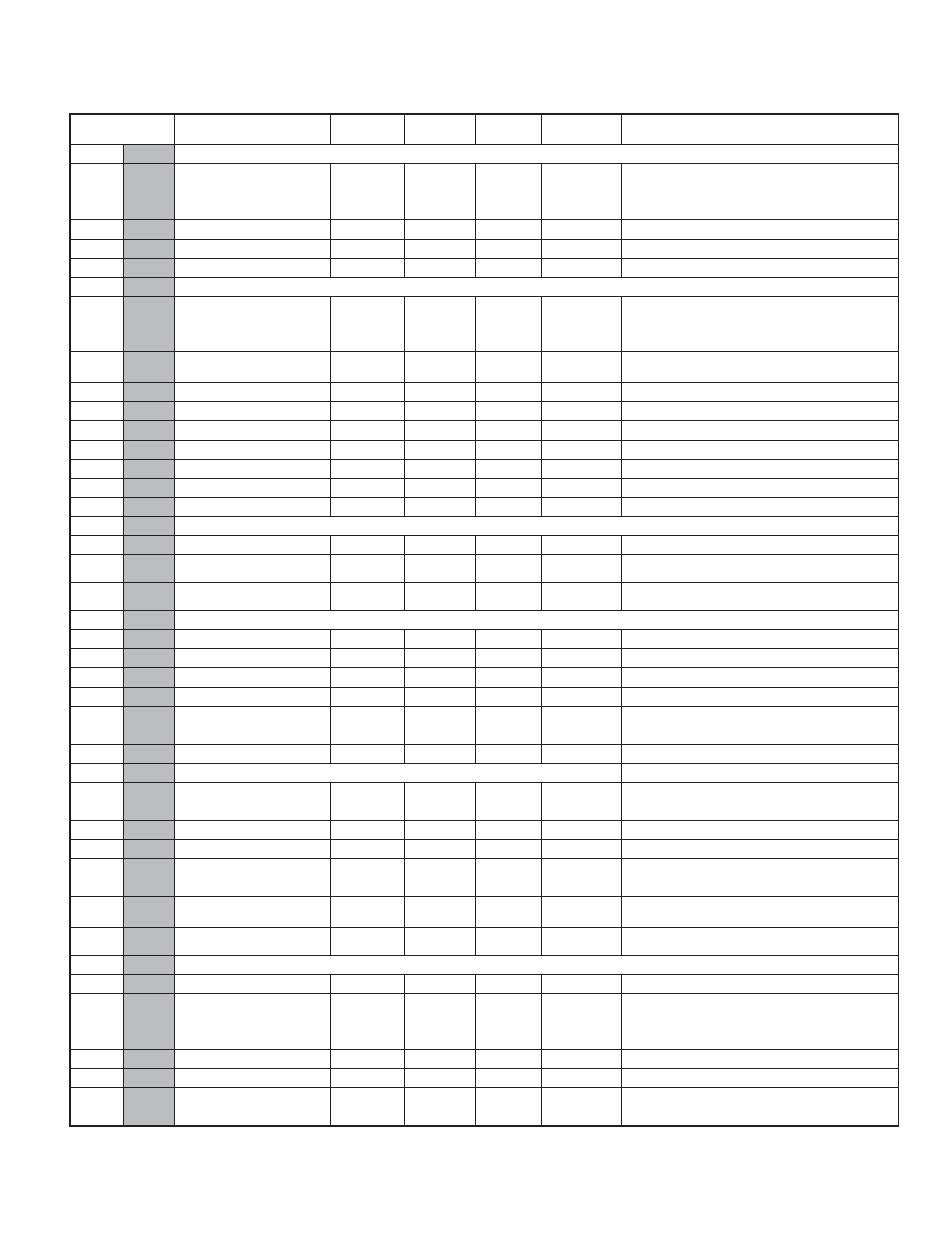
23
DLC REGISTER TABLE
The below limits are shown as Integers or HEX < > values. Read and write functions can be performed in either Integers or Hex as long as the conversion was done
correctly. Negative numbers are represented by two’s complement.
Note 1: The DLC should not be powered down while parameters are being changed. Doing so may corrupt the non-volatile memory resulting in checksum errors.
REGISTER
ADDRESS
1
REGISTER NAME
LOW LIMIT
2
HIGH LIMIT
2
FACTORY
SETTING
3
ACCESS
COMMENTS
CH A
CH B
CONTROLLING VALUES
40001
40017
Process Value
N/A
N/A
N/A
Read Only
40002
40018
Setpoint Value
-32000
32000
0
Read/Write
Limited by Setpoint Limit Low and Setpoint Limit High.
40003
40019
Alarm 1 Value
-32000
32000
0
Read/Write
40004
40020
Alarm 2 Value
-32000
32000
0
Read/Write
PID PARAMETERS
40005
40021
Output Power
0 or -1000
1000
0
Read/Write
40006
40022
Setpoint Deviation
N/A
N/A
N/A
Read Only
40007
40023
Proportional Band
0
9999
40
Read/Write
0 = On/Off Control, 1 = 0.1%
40008
40024
Integral Time
0
9999
120
Read/Write
0 = Off, 1= 1 second
40009
40025
Derivative Time
0
9999
30
Read/Write
0 = Off, 1= 1 second
40010
40026
Offset Power
-1000
1000
0
Read/Write
1 = 0.1%; Applied when Integral Time is 0.
40011
40027
Auto-Tune Start
0
1
0
Read/Write
0 = Stop, 1 = Start; Mirror of Coil 16/28.
40012
40028
Auto-Tune Phase
N/A
N/A
N/A
Read Only
0 = Off, 4 = Last phase during Auto-Tune
40013
40029
Auto-Tune Code
0
2
0
Read/Write
0 = Fastest response, 2 = Slowest response
OUTPUT STATUS
40014
40030
Control Output OP1
N/A
N/A
N/A
Read Only
0 = Off, 1 = On; Mirror of Coil 9/21.
40015
40031
Alarm Output AL1
0
1
0
Read/Write
40016
40032
Alarm Output AL2 / OP2
0
1
0
Read/Write
CONTROL STATUS
40041
40049
Control Mode
0
1
0
Read/Write
0 = Automatic, 1 = Manual; Mirror of Coil 12/24.
40042
40050
Disable Setpoint Ramping
0
1
0
Read/Write
0 = Enabled, 1 = Disabled; Mirror of Coil 13/25.
40043
40051
Setpoint Ramping In Process
N/A
N/A
N/A
Read Only
0 = No, 1 = Yes; Mirror of Coil 14/26.
40044
40052
Disable Integral Action
0
1
0
Read/Write
0 = Enabled, 1 = Disabled; Mirror of Coil 15/27
40046
40045
40053
Remote / Local Setpoint Select
Ramping Setpoint Value
0
N/A
1
N/A
0
N/A
Read/Write
Read/Write
SETPOINT CONTROLLER MODEL ONLY
PROFILE OPERATION
40065
Profile Operating Status
0
3
0
0 = Off; 1 = Abort; 2 = Run/Start, 3 = Pause, 4 = Error
Delay (status only - writing a “4” will revert unit to mode
“3” Pause)
40066
40074
Profile Phase
N/A
N/A
N/A
Read Only
0 = Ramp; 1 = Hold
40067
40075
Profile Segment
N/A
N/A
N/A
Read Only
40068
40076
Profile Phase Time Remaining
1
9999
N/A
Read/Write
40069
40077
Profile Cycle Count Remaining
1
250
0
Read/Write
40070
40078
Advance Profile Phase
0
1
0
Read/Write
INPUT PARAMETERS
40198
Ch B Assignment
0
1
0
Read/Write
0 = PID, 1 = Remote Setpoint
40199
0
2
0
Read/Write
40103
40102
40101
40203
40202
40201
Resolution
Temperature Scale
Input Type
0
0
0
1
1
17
0
0
2
Read/Write
Read/Write
Read/Write
0 = °F, 1 = °C, For Input Types 0-11.
See Input Listing
1 = 0.1%, 0.0 = Off; Limited by Power Low Limit and
Power High Limit in Automatic Control Mode. Negative
percent is cooling (direct) available when AL2 is
Cooling. Write only possible during Manual mode.
Deviation = Process Value - Setpoint Value; During
Auto-Tune: Process Value - Auto-Tune Setpoint Value
0 = Off, 1 = On; A write of 1 is only possible when
alarm is set for Manual. Mirror of Coil 10/22.
0 = Off, 1 = On; A write of 1 is only possible when
alarm is set for Manual. Mirror of Coil 11/23.
(0 = Stop, 1-20 = Current Segment)
1
For Input Registers, replace the 4xxxx with a 3xxxx in the above register address. The 3xxxx are a mirror of the 4xxxx Holding Registers.
2
An attempt to exceed a limit will set the register to its high or low limit value.
3
See MODBUS Calibration for procedure on restoring Factory Settings.
1 = Advances “running” Profile to next ramp or hold
phase
0 = Local Setpoint, 1= Remote Setpoint
Actual Setpoint Value used for control (ramps when
ramping enabled.) Limited by Setpoint Limit Low and
Setpoint Limit High.
40073
Read/Write
(0-3 only)
1= 0.1 Minute; Can make temporary change on the fly
Value Over-range = 32003 (may occur on extremely
slow ramp; Ramp will function properly)
0-250; If Cycle Count (40326/40426) is 250
(Continuous operation), value will reset to 250 at 0.
Local / Remote Setpoint
Transfer Mode
0 = Normal (Output may bump)
1 = Auto (Output may bump)
2 = Track (Local Setpoint assumes value of Remote SP
for Remote to Local Transfer)
Input Types 0-12 0=Low (x1) whole input units, 1
= High (x10) tenth of input units, Input Type 13 0 = 0.1
mV, 1 = 0.01 mV, Input Types 14-15, N/A
Process value of present input level. This value is
affected by Input Type, Resolution, & Scaling. In
Square Root Extraction Modes, the Process Value will
read zero for inputs below 0.1% of full scale.