NORD Drivesystems BU0570 User Manual
Page 13
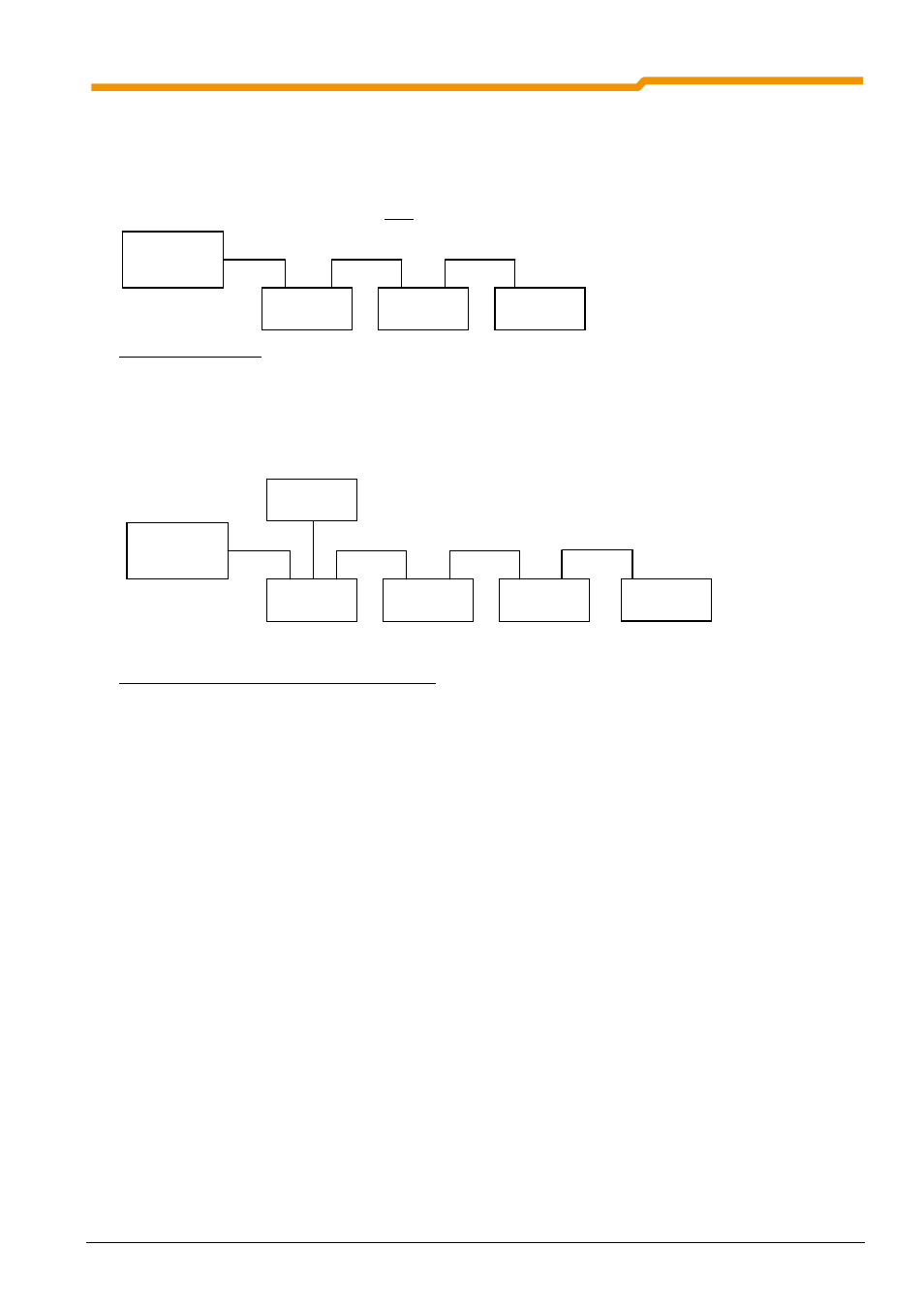
3 Commissioning
BU 0570 GB-0312
Subject to technical amendments
13
3 Commissioning
3.1 Cabling
3.1.1
Topology
The TU3-ECT EtherCAT modules can only be interconnected in a linear structure.
Fig. 5 EtherCAT topology
The EtherCAT cable from the master must be connected to the RJ45 "IN" socket of the TU3-ECT. The
EtherCAT connection from the TU3-ECT must be made via the "OUT" socket. With the last device, the
"OUT" socket remains free, a cable termination is not necessary.
The integration of a normal Ethernet switch for the connection of normal EtherCAT devices must be made
between the EtherCAT master and the first EtherCAT module; see the following diagram.
Fig. 6 EtherCAT topology with integrated standard switch
3.1.2
EMC
If EMC measures are not in place, high-frequency interference which is mainly caused by switching
processes or lightning often causes electronic components in the bus participants to be faulty and error-free
operation can no longer be ensured.
Correct laying of the bus cable dampens the electrical influences which may occur in an industrial
environment. The following points must be observed:
Implement long connections between bus participants by the shortest possible distances.
Only use plugs with a metal housing.
For the production of bus cables lay the shielding on as wide an area of the plug as possible.
With the parallel installation of bus cables, a minimum distance of 20 cm should be maintained from
other cables carrying a voltage greater than 60V. In particular, this must be observed for cables to
motors or chopper resistors. This applies to lines laid both inside and outside of control cabinets.
The minimum distances for parallel installation may be reduced by shielding cables carrying voltage or
by means of earthed metal dividers in the cable ducts.
Connect SK TU3- Ethernet module to the PE (Connection via the plug pin next to the 24V supply).
EtherCAT
Master
TU3-ECT
TU3-ECT
TU3-ECT
EtherCAT
Master
Switch
TU3-ECT
TU3-ECT
TU3-ECT
Printer