Dwyer 2600 User Manual
Page 33
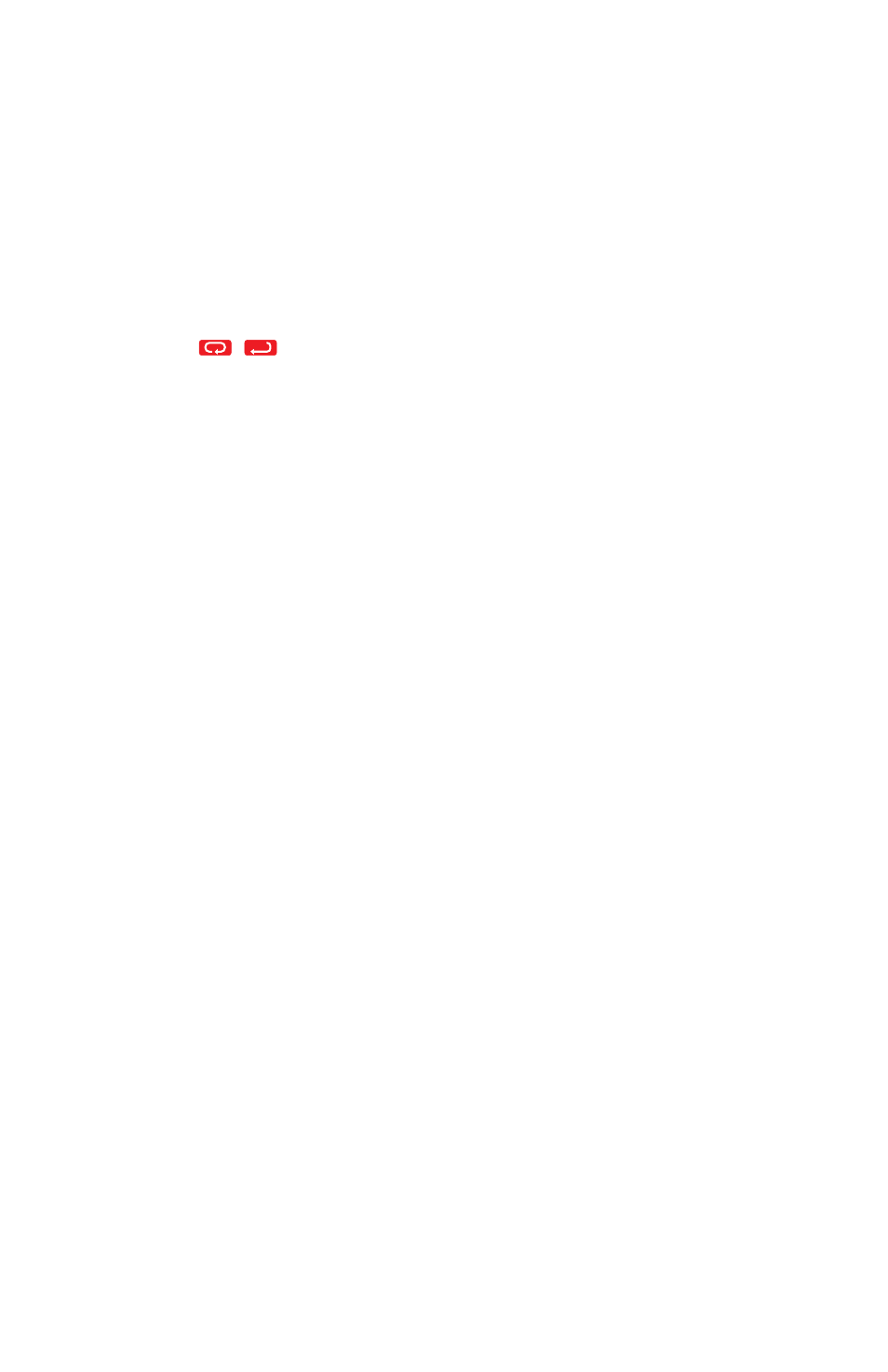
I n P t
Input Fault Timer: Select O F F , 0 . 1 to 5 4 0 . 0 minutes. Whenever an Input is out of
range (U F L or O F L displayed), shorted, or open, the timer will start. When the
time has elapsed, the controller will revert to the output condition selected by
I n P b below. If O F F is selected, the Input Fault Timer will not be recognized (time
= infinite).
S E n C
Sensor Rate of Change: Select O F F , 1 to 4 0 0 0 °F, °C, or counts per 1 second
period. This value is usually set to be slightly greater than the fastest process
response expected during a 1 second period, but measured for at least 2
seconds. If the process is faster than this setting, the S E n C b A d error message
will appear. The outputs will then be turned off. This function can be used to
detect a runaway condition, or speed up detection of an open thermocouple.
Use the INDEX & ENTER keys to reset.
S C A L
Scale Low: Select 100 to 11998 counts below S C A H . The total span between
S C A L and S C A H must be within 11998 counts. Maximum setting range is -1999
to +9999 counts. For Current and Voltage inputs, this will set the low range end.
Value not adjustable for Thermocouple and RTD ranges.
S C A H
Scale High: Select 100 to 11998 counts above S C A L . The total span between
S C A L and S C A H must be within 11998 counts. Maximum setting range is -1999
to +9999 counts. For Current and Voltage inputs, this will set the high range end.
Value not adjustable for Thermocouple and RTD ranges.
S P L
Set Point Low: Select from the lowest input range value to S P H value. This will
set the minimum SP1 or SP2 value that can be entered. The value for SP1 or
SP2 will stop moving when this value is reached.
S P H
Set Point High: Select from the highest input range value to S P L value. This will
set the maximum SP1 or SP2 value that can be entered. The value for SP1 or
SP2 will stop moving when this value is reached.
S 1 S t
Set Point 1 State: Select d i r or r E .
d i r
Direct Action. As the input increases the output will increase. Most
commonly used in cooling processes.
r E
Reverse Action. As the input increases the output will decrease. Most
commonly used in heating processes.
May, 2013
Page 33 of 52
949-1194 Rev. 7