Operation (survey) – West Control Solutions KS 94 User Manual
Page 11
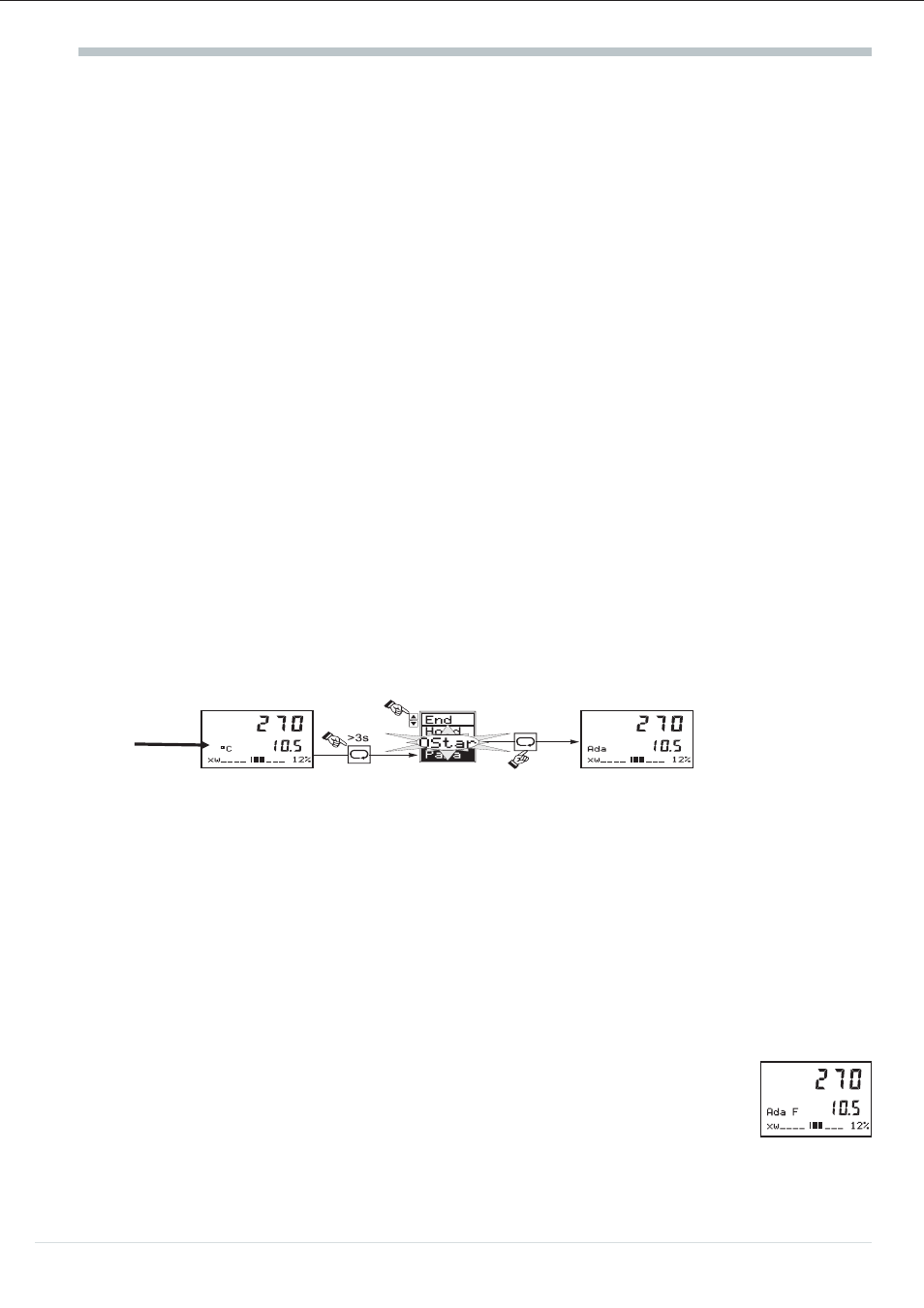
9.5
9.5
DAC – motor actuator monitoring (Digital Actor Control DAC®)
With all controllers with position feedback Yp, the motor actuator can be monitored for functional
troubles.
CFunc = 08 = 3-point stepping controller with position feedback as a potentiometer
CFunc = 09 = continuous with position feedback as a potentiometer
CFunc = 12 = continuous with current feedback via Yp (INP6)
The system detects the following stepping controller errors:
w
defective motor
w
defective capacitor (wrong rotating direction),
w
wrong phase followers
w
defective force transmission at spindle or drive,
w
excessive backlash due to wear
w
jamming of the control valve e.g. due to foreign body
With the continuous controllers, monitoring if output signal and position feedback exceed a
difference of 10 % after elapse of a 20 s filter time is provided. The DAC® function can be switched
on or off at parameter setting level (DAC = 0/1). A detected trouble is indicated, the controller
switches to manual mode and no pulses are output any more.
a
During Yp calibration, the DAC® function is activated! Otherwise, disabling would be
detected when reaching the limits and the controller would be switched to “off” (r
calibration).
9.6
Self-tuning
(automatic optimization of control parameters)
After starting by the operator, the controller makes an attempt for optimization by determining the
parameters for fast line-out at the set-point without overshoot from the process characteristics.
Optimization start:the operator can start the optimization attempt at any time (see opposite drawing).
Preparation for self-tuning:
•
PID, PI, PD or P control behaviour can
be selected by the user by switching off
Tn=0 or Tv=0 before self-tuning start.
•
Determine the output step change (dYopt).
•
Determine the stable correcting variable (YOptm).
•
Determine the `process-at-rest’ mode ( C.700 ; OCond)
•
Determine which parameter set shall be
optimized (POpt).
•
Is the set-point reserve (x-w) > 10% of W100-W0?
Self-tuning cancelation:
The operator can cancel the optimization attempt at any time. This is possible by pressing key H
(Äcontroller switches to ‘manual’) or via OStop in menu1 (Ä controller switches to `automatic’).
The controller continues operating with the old parameter values.
Optimization problems:
With process conditions which prevent successful optimization, the controller cancels
the attempt for optimization (Ada F is displayed). The controller outputs are
switched off to prevent the set-point from being exceeded. Afer self-tuning
cancelation, controlling is continued with the old parameter values.
Operation (survey)
13
Operating instruction KS94