Basic operation – Yokogawa In-Situ Gas Analyzer TDLS200 User Manual
Page 88
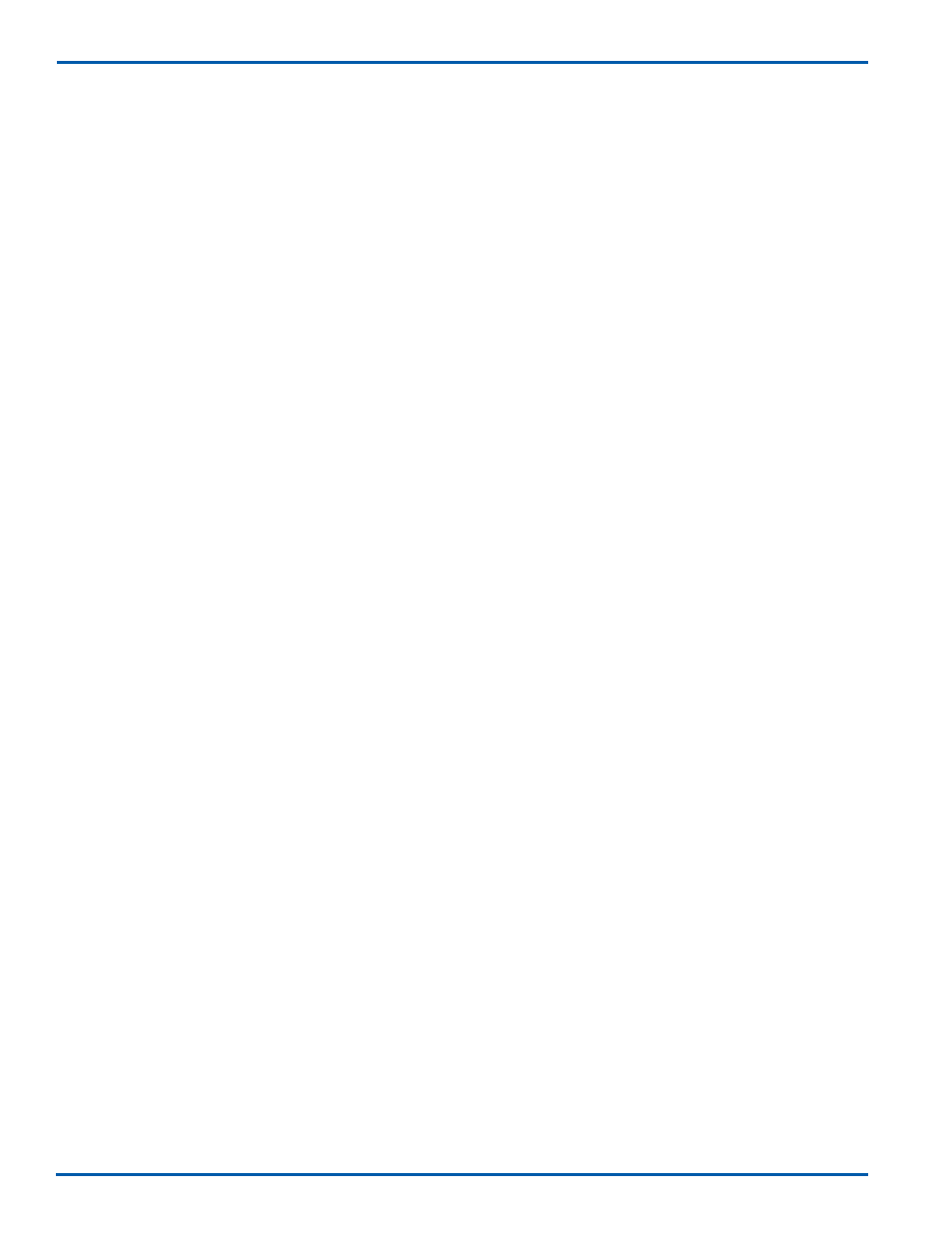
6-32
IM 11Y01B01-01E-A 6th Edition :Feb 13, 2013-00
<6. BASIC OPERATION>
AUTO ONLINE VALIDATION – see separate section of User Guide for details
1. Remember the current valve status.
2. Turn on the assigned valve(s), turn off other valves. Two valves could be
open for auto online validation with blocked line lock gas in validation cell.
3. If only one valve is used, turn off the assigned valve. If two valves are used, turn off the first valve.
4. If two valves are used, turn off the second valve.
6.7 Introduction for H
2
Oppm Measurements in Methane Gas
The measurement of H
2
Oppm in methane gas (LNG/NG) is specifically outlined in this section. Items contained
within this section will supersede any prior information within the User’s Guide, particularly items pertaining to
calibration methods. Please also note the special requirements needed for the flow cell measuring conditions as
these can affect the measured H
2
Oppm concentration values.
Spectroscopic detection of moisture in natural gas presents a specific challenge for traditional TDLS methods,
because a weak (at low ppm moisture content) absorption line of water must be detected on a high absorption
background of methane and other components (C2/C3) of the natural gas. This challenge has been successfully
overcome with TDLS200 by using a special (previously proven) approach to spectroscopic data processing.
However, reliability of results relies on stable and well defined conditions in the flow cell of the TDLS200 analyzer.
Note that typically temperature of the process/calibration gases within the flow cells is to be maintained
at 50.0±0.5 ºC and the gas pressure controlled at 30±0.25 psig. Maintaining these conditions ensures well-
defined absorption of methane and reliable ppm moisture concentration readings.
At the same time, this method eliminates the need for routine analyzer calibrations (zero or span). This is due
to the fact that the strength of molecular absorption is an intrinsic property of the chemical species. When the
gas temperature, pressure, and its bulk composition are defined, absorption spectrum depends only on the
absorption path length, which is also fixed in the supplied analyzers. These analyzers are factory calibrated and
Therefore, the H
2
Oppm in Natural Gas analyzers DO NOT require actual field calibration by end users
– they can however be Validated. Calibration procedure described in the standard TDLS200 User Guide is
intended for the different measurements/techniques of data processing and
must not be used in these units. If
applied to these H
2
O-NGas analyzers, it will disrupt the file system with unpredictable/erroneous results requiring
factory assistance to restore proper functionality.
At all times, the analyzer internal optics must be purged with dry nitrogen (<0.25 ppm H
2
O content). Any moisture
present within the analyzer internal optics purge gas (or on-validation cell purge gas) will be added to the actual
process gas measurement of H
2
Oppm.
DO NOT ZERO or SPAN CALIBRATE THE ANALYZER without prior written approval from the Yokogawa
Laser Analysis Division factory!
Validation (response check) of the analyzer can be performed in two possible ways:
(1) Off-Line Method (interrupting process flow through the cell): A pure dry (<5 ppm H
2
O) methane (100%
CH
4
) validation gas can be supplied to the flow cell (at same flow conditions 50ºC and 30 psig); analyzer
readings for CH
4
% must be 100±2%. Note, at this time the analyzer will also indicate any value of
residual moisture in the pure dry methane validation gas standard.
(2) On-Line Method (no interruption of process flow through the cell) to observe a step change in the
H
2
O ppm output value: Nitrogen gas with typical 100-120 ppm H
2
O (+/-10 ppm) content can be switched
through the on-line validation cell at 10psig (for example, equipped with a 10 psig pressure relief valve
on validation cell outlet). The analyzer readings for H
2
O will be increased by approximately 10-12 ppm
(based on 110 ppm*pathval.cell/pathflow cell) or roughly equivalent to 10% of the cylinder certified
H
2
O ppm value. This is an observation only of step change to the introduction of H
2
O into the optical
path, sometimes considered a “response check” or “analyte spiking”.