Trouble shooting, Weak or no laser output, Danger – Yokogawa In-Situ Gas Analyzer TDLS200 User Manual
Page 133: Warning, Caution
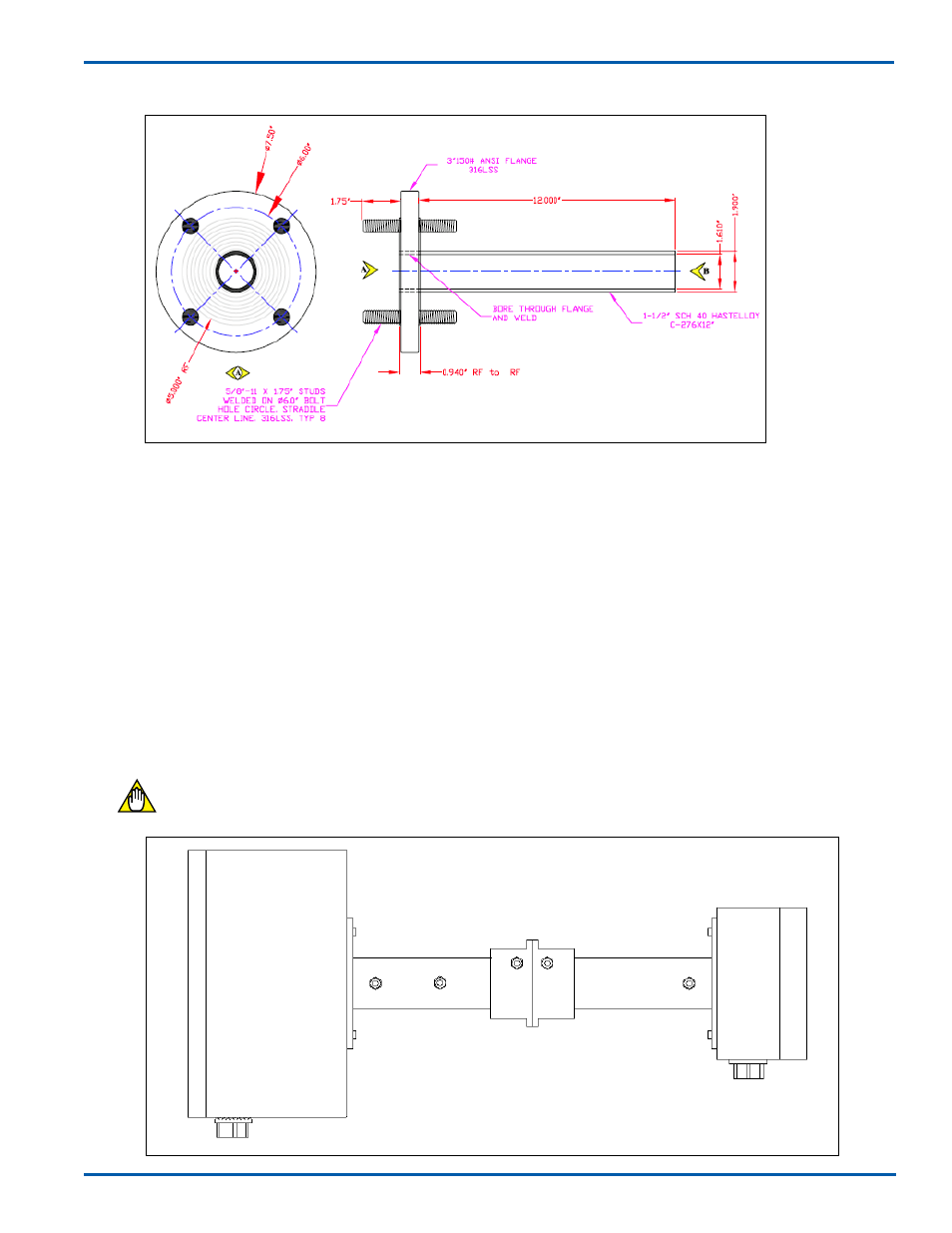
9-7
9-8
IM 11Y01B01-01E-A 6th Edition :Feb 13, 2013-00
<9. TROUBLE SHOOTING>
Please consult
Yokogawa with specific information about the dust loadings within the process such that
a proper evaluation can be made. If it is then determined that a reduction in optical path length will have
a significant improvement on the transmission level (or at least improve it to the point whereby analyzer
performance is acceptable) then Analytical Specialties will advise further detail on the project specific insertion
tube requirements. Often, the insertion tubes have to be constructed of materials that are compatible with the
process media e.g. acidic, corrosive, gases may require insertion tubes of Hastelloy C-276 or Monel A-400.
4. Weak or No Laser Output
a. If it has been determined that the process aperture is clear, the gas is clean and the system has been fully
aligned in all directions and yet there is still little or no transmission, then the laser output power may be
weak or even dead.
b. There is only one certain method to determine if a laser has lost output power and that is to directly place
the detect unit in front of the launch unit (as per diagram below). Before doing so, ensure that both
process windows are clean.
CAUTION: The laser diode light source will be exposed when the launch unit is accessible in this
way so ensure precautions are taken to avoid direct eye exposure to the laser light!
TDLS200 TDL Analyzer Instruction Manual V2.1
Page 116 of 131
- 116 -
4.
Weak or No Laser Output
a.
If it has been determined that the process aperture is clear, the gas is clean and the
system has been fully aligned in all directions and yet there is still little or no transmission,
then the laser output power may be weak or even dead.
b.
There is only one certain method to determine if a laser has lost output power and
that is to directly place the detect unit in front of the launch unit (as per diagram below).
Before doing so, ensure that both process windows are clean.
CAUTION: The laser diode light source will be exposed when the launch unit is
accessible in this way so ensure precautions are taken to avoid direct eye exposure
to the laser light!
If there is any sign of a transmission signal then try adjusting the angles very slightly to see if any
stronger signal can be obtained. If, after adjusting the direct angle between the two units there is
still no transmission then the laser diode (and or detector) has failed. Please contact Yokogawa
Laser Analysis Division for further assistance and information pertaining to Laser Module
replacement. If a weak signal is achieved then this is an indication that the laser module has weak
output power. Please contact Yokogawa Laser Analysis Division as this may be caused by
dirt/contamination on one of the internal optical surfaces (usually caused by contaminated purge
gas).
6.1.3 Off Process (or Off-Line)
Clean Process Windows
. Visually inspect and clean analyzer windows.
Check Analyzer with Validation Standard
. Mount the analyzer on a calibration or flow
cell and perform Basic Menu zero and span check – capture spectrum for each condition.
Record Results
. Download data files from the analyzer for e-mail to Yokogawa Laser
Analysis Division
2
All Rights Reserved. Copyright © 2011, Yokogawa Electric Corporation. Subject to change without notice.
January 2011
IM 11A00V01-01E-A
Operating and Maintenance Manual
1. Introduction ...................................................................................................4
1.1 Features ................................................................................................ 4
2. General Specifications .................................................................................5
3. Theory of Operation......................................................................................6
3.1 Brief History of Reflux Samplers ......................................................6
3.2 Filter Section .....................................................................................6
3.3 Steam Supplement ...........................................................................6
3.3 Inlet Temperature Section ................................................................6
3.4 Heat Exchanger Section ...............................................................6-7
3.5 Outlet Temperature Section .............................................................7
3.6 Self Acting Temperature Controller ..................................................7
3.7 Instrument Air for the Vortex Tube ...................................................7
3.8 Vortex Theory of Operation ..............................................................7
4. Utility Requirements .....................................................................................8
4.1 Instrument Air ...................................................................................8
4.2 Low Pressure Steam ........................................................................8
5. Installation .....................................................................................................9
5.1 Mechanical Considerations ..............................................................9
5.2 Fast Loop Line Size and Response Times .....................................9
5.3 Insulation ..........................................................................................9
6. Start-Up .......................................................................................................10
7. Operation .................................................................................................... 11
7.1 Vortex Tubes ................................................................................... 11
7.2 Steam Injection ............................................................................... 11
7.3 Controller ........................................................................................ 11
8. Maintenance ...............................................................................................12
8.1 Filter Section and/or Heat Exchanger Cleaning .......................12-13
9. Trouble Shooting ........................................................................................14
9.1 Vortex Tubes ...................................................................................14
10. Sub-Component Documentation .............................................................15
10.1 Vortex Tube Installation and Maintenance .............................15-17
10.2 Installation and Maintenance for SA Control Valve ...............18-24
11.2.1 General Safety ................................................................19
11.2.2 Tech. Details ...................................................................19
11.2.3 Install and Commiss ..................................................20-22
11.2.4 Maintenance ..............................................................23-24
10.3 Supplement Safety Information ...................................................25
10.3.1 Intended Use ..................................................................25
The following safety symbols are used on
the product as well as in this manual.
DANGER
This symbol indicates that an operator
must follow the instructions laid out in
this manual in order to avoid the risks, for
the human body, of injury, electric shock
or fatalities. The manual describes what
special care the operator must take to
avoid such risks.
WARNING
This symbol indicates that an operator must
refer to the instructions in this manual in
order to prevent the instrument (hardware)
or software from being damaged, or a
system failure from occurring.
CAUTION
This symbol gives information essential
for understanding the operations and
functions.
Note!
This symbol indicates information that
complements the present topic.
Figure 68
Figure 69