General specifications – Yokogawa In-Situ Gas Analyzer TDLS200 User Manual
Page 17
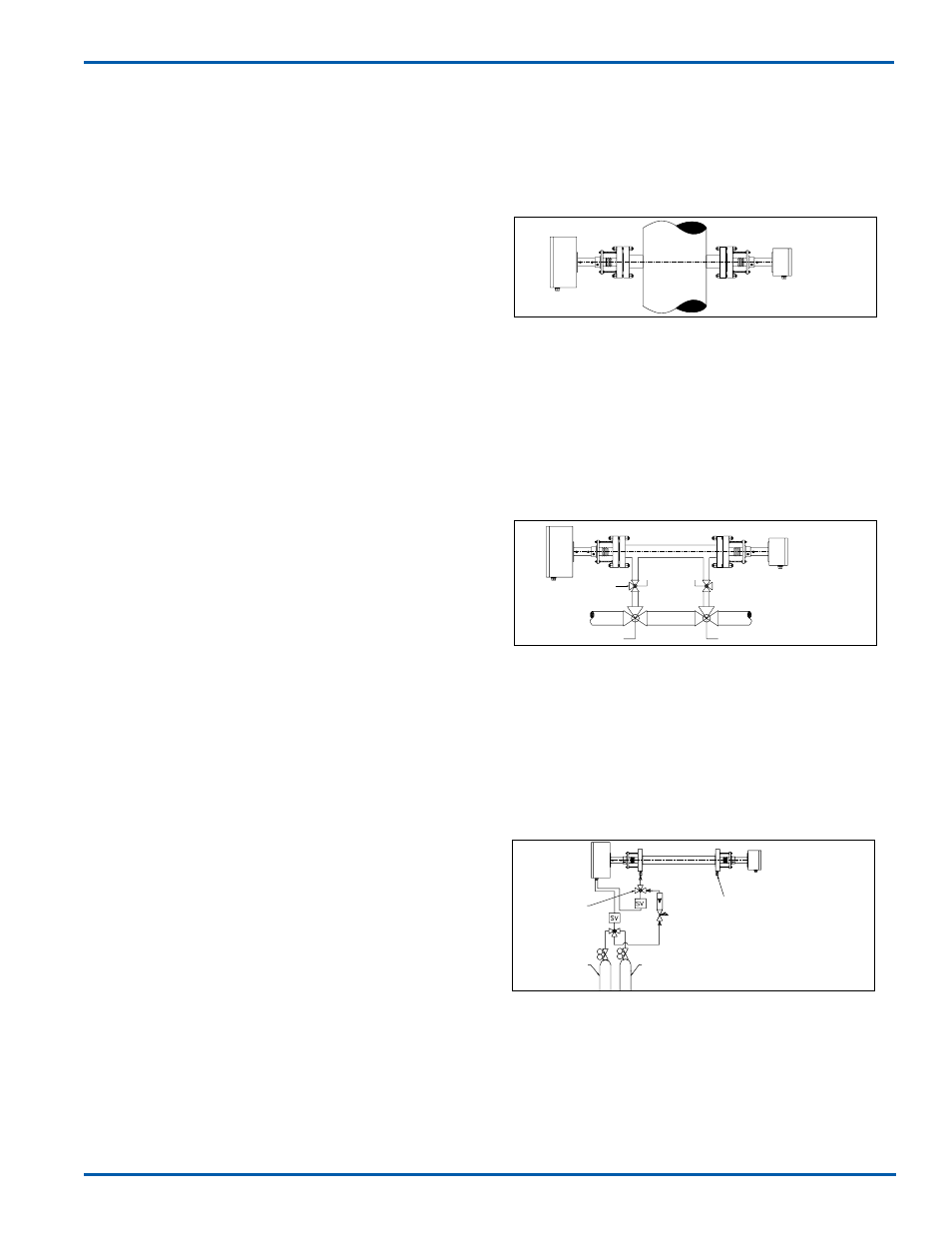
Performance Specification
Repeatability:
Application Dependent
Linearity:
+/- 1% of FS
Response time:
2-20 seconds, plus transport time for
extractive systems when applicable
Drift:
Application Dependant
Installation Specifications
Hazardous Area:
Zone 1: Contact Yokogawa
Zone 2: ATEX group II Cat. 3G with purge
system EEx pz II T5 (-20< Ta <50C)
By Design:
Non-Hazardous Area; Purge required for
ATEX zone 1&2 and NEC Class 1
Division 1&2
Maximum Distance between Launch and Detect:
30 m (±90ft)
Maximum interconnecting cable 50m
Wetted Parts:
Analyzer & standard Alignment Flange - 316
SS, BK-7 Glass, Teflon encapsulated Viton
and Silicone RTV sealant.
Optional:
Isolation Flanges and Flow Cells - 316 SS,
Sapphire, Kalrez -
Also available in Monel A400, Hastelloy
C-276, Carpenter 20, Titanium Grade 2 and
others on request.
Utilities:
Instrument Air may be used as a purge gas in principle for all of the
below applications, but this will depend on the application type and the
required precision of the measurement.
Oxygen Analyzer
N
2
CO Analyzer
N
2
or Instrument Air
CO
2
Analyzer
N
2
or other non-CO
2
containing inert gas
H
2
O ppm Analyzer
N
2
with <20ppm levels H
2
O for feed to
optional Dryer Package
H
2
O % Analyzer
N
2
Flow Rate:
• 5-30 L/min for window purge
• 2 L/min for validation, calibration and optical
purge
SIL Assessment:
The TDLS200 has a FMEDA assessment by exida and is
classified as a Type B1 device in compliance with the following
standards; IEC 61508 or EN 954-1. Functional Safety of Electrical/
electronic/programmable electronic related systems; SIL 1
capability for single device.
* The TDLS200 is not SIL certified as standard; to be certified the unit
must be specified and designed from the beginning to meet all SIL
specifications.
Basic System Configuration
The TruePeak can be installed in a number of ways depending on
process requirements. The most typical installation types are shown
below, however other installation methods are possible, please contact
Yokogawa with your application details.
Cross Stack/Pipe Configuration
• Measures directly across process pipe or vessel
• Typically has nitrogen or other purge gas protecting
process windows
• Span Validation via serial flow cell (see Operation Specifications).
• Full calibration requires removal from process
• May require pressure and temperature inputs
(Application Dependant)
• Multiple methods to increase Optical Path Length (OPL) if needed
• 5 meter interconnection cable standard
Close Coupled Extractive / Bypass Configuration*
• Measures across a section of pipe where process flow
is directed
• The measurement section can be isolated from process flow for full
calibration/validation, zero and span
• Process pressure and temperature can be controlled
or the analyzer may require pressure and temperature inputs
(Application Dependant)
• Length of measurement section dependant on accuracy requirements
and process conditions
Extractive Configuration*
• Sample is fully extracted from process
(and may be conditioned before measurement).
• Flow cells are available with ability to purge in front of windows
(balanced flow cell) if required.
• Process pressure and temperature can be controlled
or the analyzer may require pressure and temperature inputs
(Application Dependant)
• Length of flow cell dependant on accuracy requirements
and process conditions
* Contact Yokogawa for further details
Zero check gas,
at grade
Span check gas.
at grade
Flow-Cell-Outlet
process
sample
inlet
Cal
inlet
PROCESS
3-1
3-2
IM 11Y01B01-01E-A 6th Edition :Feb 13, 2013-00
<3. GENERAL SPECIFICATIONS>