Introduction and general description> 2-4 – Yokogawa In-Situ Gas Analyzer TDLS200 User Manual
Page 14
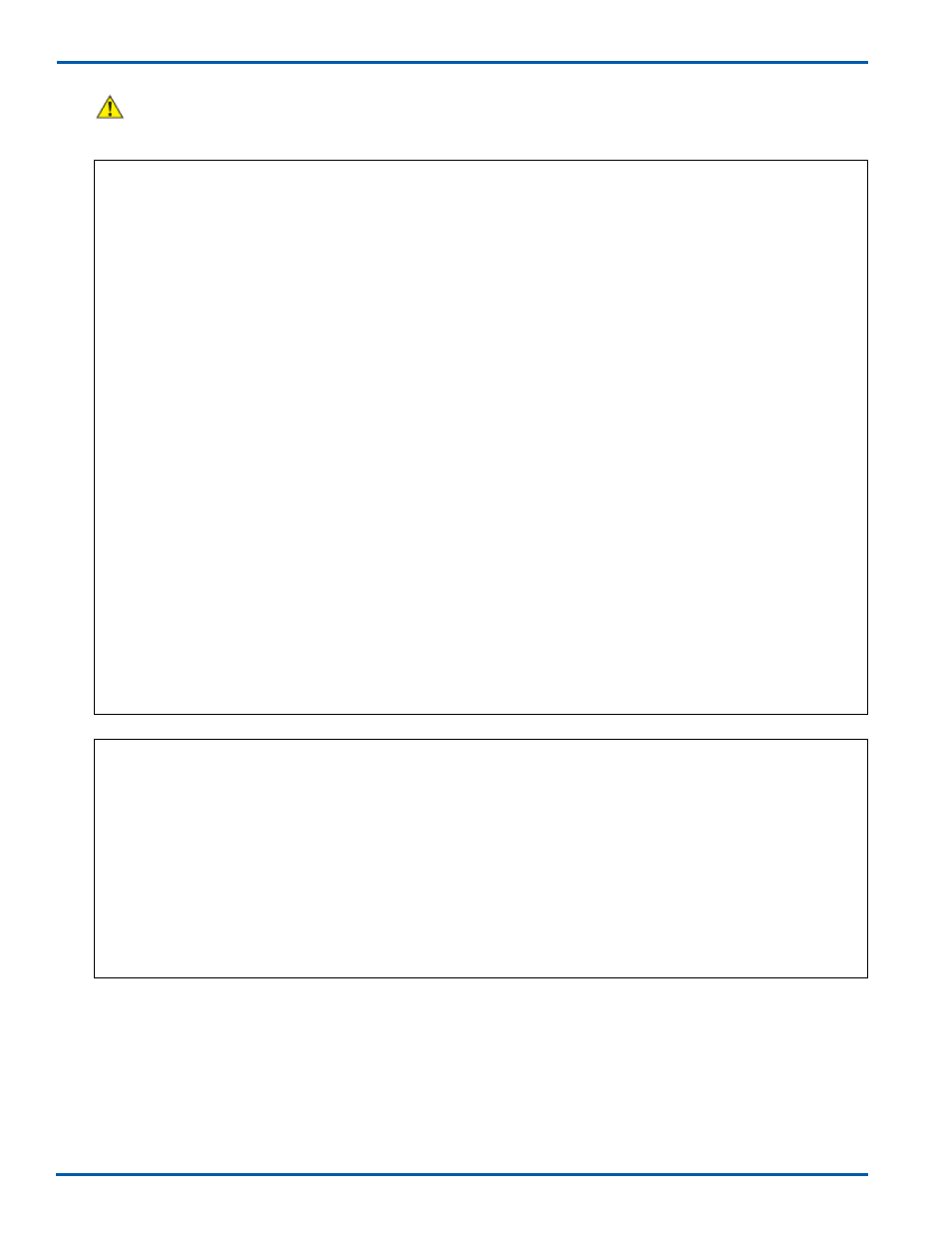
<2. INTRODUCTION AND GENERAL DESCRIPTION> 2-4
IM 11Y01B01-01E-A 6th Edition :Feb 13, 2013-00
Materials of Construction
NOTE - ATEX Hazardous Area Operation:
Product MUST NOT be used in Zone 0 (CAT 1) locations
Product MUST NOT be used in Group I (Dust/Grain) locations
Product MUST NOT be used in Group III (Fibers) locations
Conditions of Certification
On loss off purge an alarm shell be made to inform the user, action shall then be taken by the user to
ensure continued use is safe.
A functional test shall be carried out in accordance with clause 17.1 of EN 60079-2:2007 to verify the
parameters of the Purge Control Unit when fitted.
A leakage test shall be carried out in accordance with clause 17.2 of EN 60079-2:2007. The
manufacturer shall record and retain these results.
Only Lithium batteries specified in manual are to be used in this enclosure.
Special Conditions of Certification:
A suitability certified Purge Control Unit must be sued with the TDLS Analyzer that is capable providing
the requirements listed on label/certificate and that either provides a suitable exhaust through a particle
barrier of to a safe area.
When installed there shall be a minimum of two pressure regulators in the air/nitrogen supply line.
The analyzer incorporates a variety of materials in its construction and they should therefore be
used in an appropriate manner. Any chemicals (liquid or gas) that may have a detrimental effect on
the product’s structural integrity should not be allowed come in contact.
The electronic enclosures are constructed from Aluminum Alloy AL Si 12 (ASTM A413) and have a
protective epoxy powder coated surface finish.
The welded bodies are constructed of stainless steel grade 316
The fasteners are constructed of stainless steel grade 18-8
The windows (when fitted) are constructed of laminated safety glass
CAUTION - For Cleaning of the labels and LCD window, please use wet cloth to avoid electrostatic
condition.
• Process/environmental conditions that may be related to the failure of the device.
• A statement whether warranty or nonwarranty service is requested
•
Complete shipping and billing instructions for return of material, plus the name and phone number of a
contact person who can be reached for further information.
Returned goods that have been in contact with process fluids must be decontaminated/ disinfected before shipment.
Goods should carry a certificate to this effect, for the health and safety of our employees. Material safety data sheets
should also be included for all components of the processes to which the equipment has been exposed.