Validation and calibration, Danger, Warning – Yokogawa In-Situ Gas Analyzer TDLS200 User Manual
Page 114: Caution
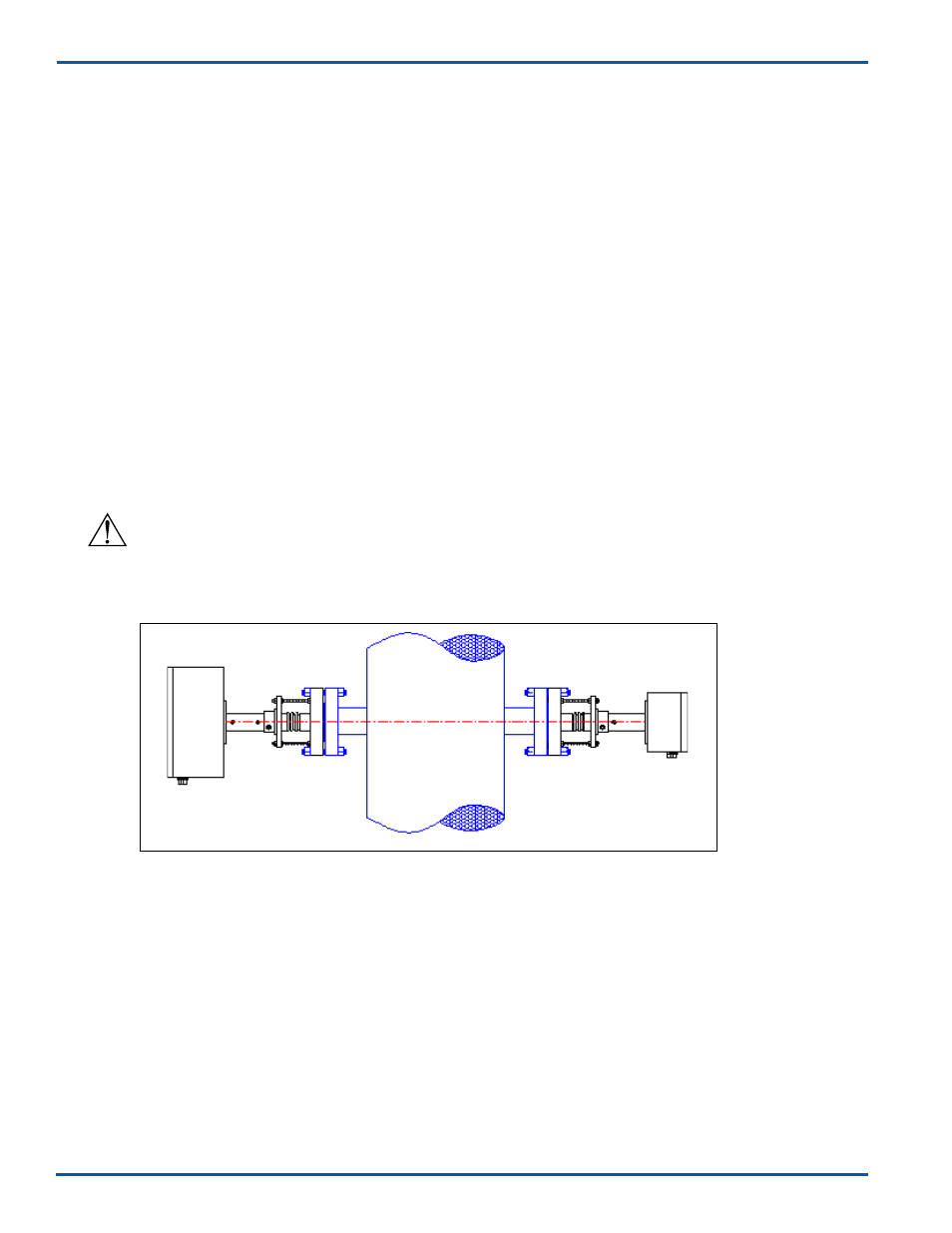
8-14
IM 11Y01B01-01E-A 6th Edition :Feb 13, 2013-00
<8. VALIDATION AND CALIBRATION>
8.3 On-Line Validation
The basic concept of on-line validation is to add a known gas concentration via an integral check gas flow cell
while still measuring the process gas concentration under relatively controlled conditions.
The controlled (or known) conditions for the addition of the validation (or check) gas are:
• Pressure of the check gas being introduced (typically atmospheric)
• Temperature of the check gas being introduced (typically ambient)
• Length of the cell in which the check gas being introduced (typically 3.7-4.0”)
• Concentration of the check gas being introduced (application specific)
The fundamental procedure performed is:
• Introduce the known check gas
• Enter the know validation parameters via software
• After purging the check gas flow cell for a period, take measurement
• Re-Introduce the original purge gas (typically Nitrogen or I/A)
• After purging the gas flow cell for a period, take a third reading Second measurement
• The analyzer then calculates what the expected ‘addition’ should be from the known parameters and
compares the ‘Expected Value’ to the ‘Actual Value’ and determines a PASS or FAIL situation
NOTE: It is better to perform on-line validations when the process is relatively stable. Some processes
are very dynamic so it at all possible, try to perform the validation during a more stable process operating
period. This will help ensure the validation is meaningful.
8.4
ON-LINE VALIDATION OVERVIEW:
A tunable diode laser emits light energy within a very narrow wavelength range which is controlled by the
analyzer itself, typically no more than 0.1nm across the entire scan region. This therefore allows laser scanning
across just one absorption peak and baseline (zero absorption) regions on either side. The analyzer scans this
region approximately 1,000 times per second while accumulating the spectra in memory. The scanning (i.e.
wavelength adjustment) is controlled by rapid adjustment of the electrical drive current on the diode itself.
2
All Rights Reserved. Copyright © 2011, Yokogawa Electric Corporation. Subject to change without notice.
January 2011
IM 11A00V01-01E-A
Operating and Maintenance Manual
1. Introduction ...................................................................................................4
1.1 Features ................................................................................................ 4
2. General Specifications .................................................................................5
3. Theory of Operation......................................................................................6
3.1 Brief History of Reflux Samplers ......................................................6
3.2 Filter Section .....................................................................................6
3.3 Steam Supplement ...........................................................................6
3.3 Inlet Temperature Section ................................................................6
3.4 Heat Exchanger Section ...............................................................6-7
3.5 Outlet Temperature Section .............................................................7
3.6 Self Acting Temperature Controller ..................................................7
3.7 Instrument Air for the Vortex Tube ...................................................7
3.8 Vortex Theory of Operation ..............................................................7
4. Utility Requirements .....................................................................................8
4.1 Instrument Air ...................................................................................8
4.2 Low Pressure Steam ........................................................................8
5. Installation .....................................................................................................9
5.1 Mechanical Considerations ..............................................................9
5.2 Fast Loop Line Size and Response Times .....................................9
5.3 Insulation ..........................................................................................9
6. Start-Up .......................................................................................................10
7. Operation .................................................................................................... 11
7.1 Vortex Tubes ................................................................................... 11
7.2 Steam Injection ............................................................................... 11
7.3 Controller ........................................................................................ 11
8. Maintenance ...............................................................................................12
8.1 Filter Section and/or Heat Exchanger Cleaning .......................12-13
9. Trouble Shooting ........................................................................................14
9.1 Vortex Tubes ...................................................................................14
10. Sub-Component Documentation .............................................................15
10.1 Vortex Tube Installation and Maintenance .............................15-17
10.2 Installation and Maintenance for SA Control Valve ...............18-24
11.2.1 General Safety ................................................................19
11.2.2 Tech. Details ...................................................................19
11.2.3 Install and Commiss ..................................................20-22
11.2.4 Maintenance ..............................................................23-24
10.3 Supplement Safety Information ...................................................25
10.3.1 Intended Use ..................................................................25
The following safety symbols are used on
the product as well as in this manual.
DANGER
This symbol indicates that an operator
must follow the instructions laid out in
this manual in order to avoid the risks, for
the human body, of injury, electric shock
or fatalities. The manual describes what
special care the operator must take to
avoid such risks.
WARNING
This symbol indicates that an operator must
refer to the instructions in this manual in
order to prevent the instrument (hardware)
or software from being damaged, or a
system failure from occurring.
CAUTION
This symbol gives information essential
for understanding the operations and
functions.
Note!
This symbol indicates information that
complements the present topic.
Figure 60