5 basic mode (except modbus communication type), Basic mode (except modbus communication type) -4 – Yokogawa EJX930A User Manual
Page 12
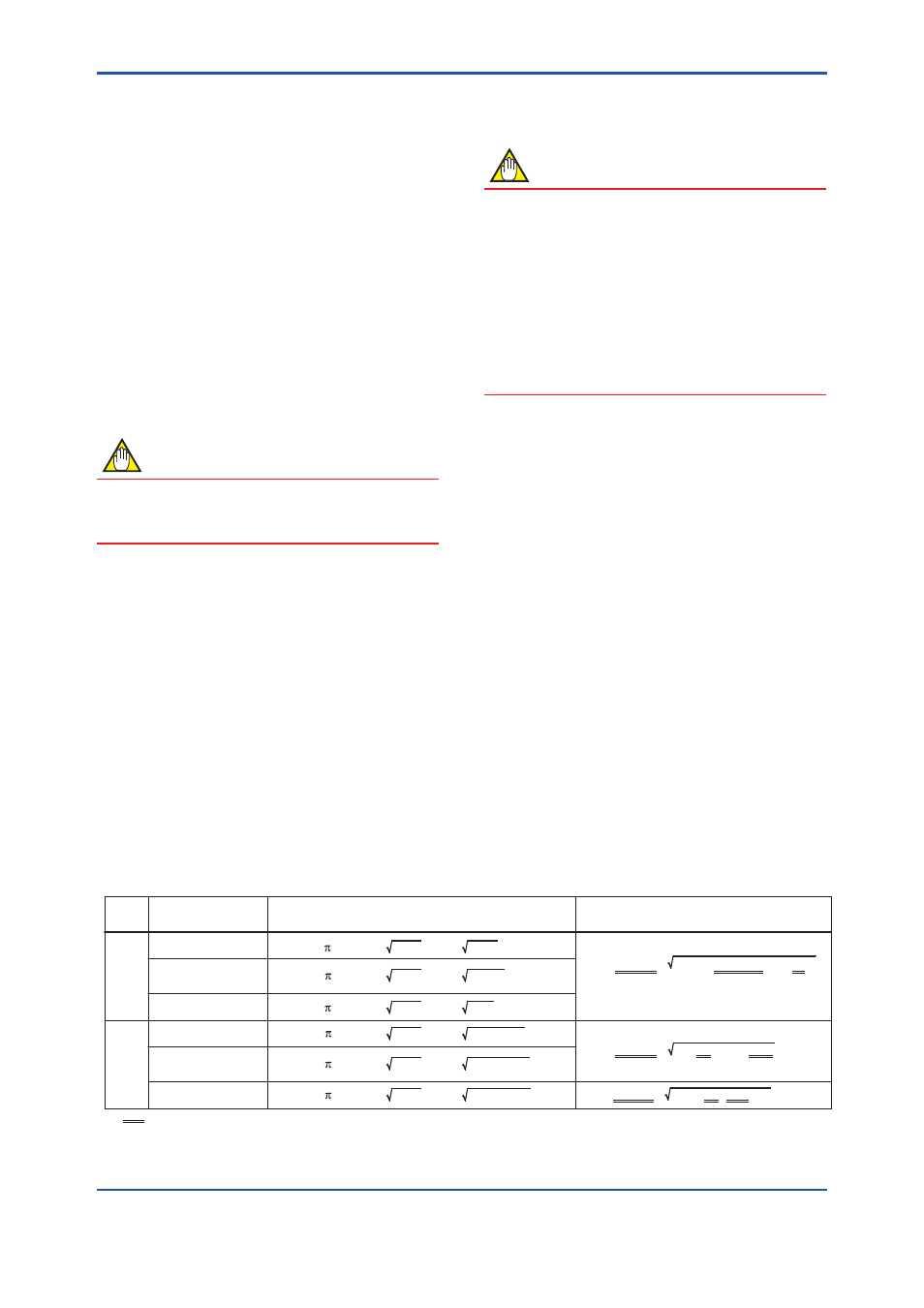
<2. About the EJX Multivariable Transmitter>
2-4
IM 01C25R01-01E
2.4.1 Configuration Procedure for Auto
Compensation Mode
The FlowNavigator is required to configure
auto compensation mode. Following shows the
procedures for HART protocol type.
Before starting the configuration procedure, have
on hand all data on the fluid and the primary
devices.
(1) Have ready a power supply, a personal
computer, a HART modem, and the FSA120
Flow Configuration Software. (FlowNavigator)
(2) Install the mass flow configuration software on
the personal computer.
(3) Connect the EJX multivariable transmitter to the
power supply.
NOTE
Configuration can be done when the RTD is
not connected, but alarm number 03 will be
displayed on the indicator.
(4) Connect the HART modem to the personal
computer and connect its clips to the supply
terminals on the transmitter.
(5) Perform flow configuration.
(6) Execute flow simulation using the HART HHT
or the FlowNavigator to confirm the configured
flow parameters.
When executing the simulation, it is necessary
to connect the RTD or mock resistance (about
100Ω) to the transmitter.
Input the differential pressure, static pressure,
and temperature values and confirm that the
desired flow is obtained.
(7) Remove the HART modem from the transmitter.
(8) Turn off the power supply.
NOTE
(1) Refer to the following instruction manuals for
more detailed explanation.
Setting with the HART HHT:
IM01C25R02-01E.
Setting with the Fieldbus configuration tool:
IM01C25R03-01E.
Setting with the FlowNavigator:
IM01C25R51-01E.
(2) For the flow configuration in the field after
installation, perform only steps 4 to 7.
2.5 Basic Mode (except Modbus
Communication Type)
In the case of Basic mode, flow operation and
density compensation are performed conventionally
with the flow factors manually input.
The flow rate is calculated using the constant flow
factor.
Density is compensated as follows according to the
selection of gas or liquid.
Gas: Compensation as ideal gas by
temperature and pressure.
Liquid: Compensation by temperature.
Select the operational expression according to the
fluid type and unit category, as shown in Table 2.1.
Table 2.1
Flow Operational Expression for Basic Mode
T0201.ai
Flow unit Category
Kfactor
Flow
Fluid
type
Mass Flow
Normal · Standard
Volume Flow
Liquid
Normal · Standard
Volume Flow
Volume Flow
Mass Flow
Volume Flow
Gas
*1
Custom setting Parameter
Kfactor = /4×Nc×C/ 1–β
4
×ε×d
2
× 2×ρb
Kfactor = /4×Nc×C/ 1–β
4
×ε×d
2
× 2×ρb /ρnorm
Kfactor = /4×Nc×C/ 1–β
4
×ε×d
2
× 2/ρb
Kfactor = /4×Nc×C/ 1–β
4
×ε×d
2
× 2×ρb×1/K
Kfactor = /4×Nc×C/ 1–β
4
×ε×d
2
× 2×ρb×1/K /ρnorm
Kfactor = /4×Nc×C/ 1–β
4
×ε×d
2
× 2/(ρb×1/K)
Qm, Qv or Qv_norm
= Kfactor × ∆P×(1+Temp K1×(T–Tb))
Qm or Qv_norm
= Kfactor × ∆P×Tb/T×SP/SPb
Qv = Kfactor × ∆P×T/Tb×SPb/SP
*
1
*
1
*
1