Modbus - using programmable memory blocks, Cip - communications capabilities, Modbus – Watlow EZ-ZONE ST User Manual
Page 77: User programmable memory blocks
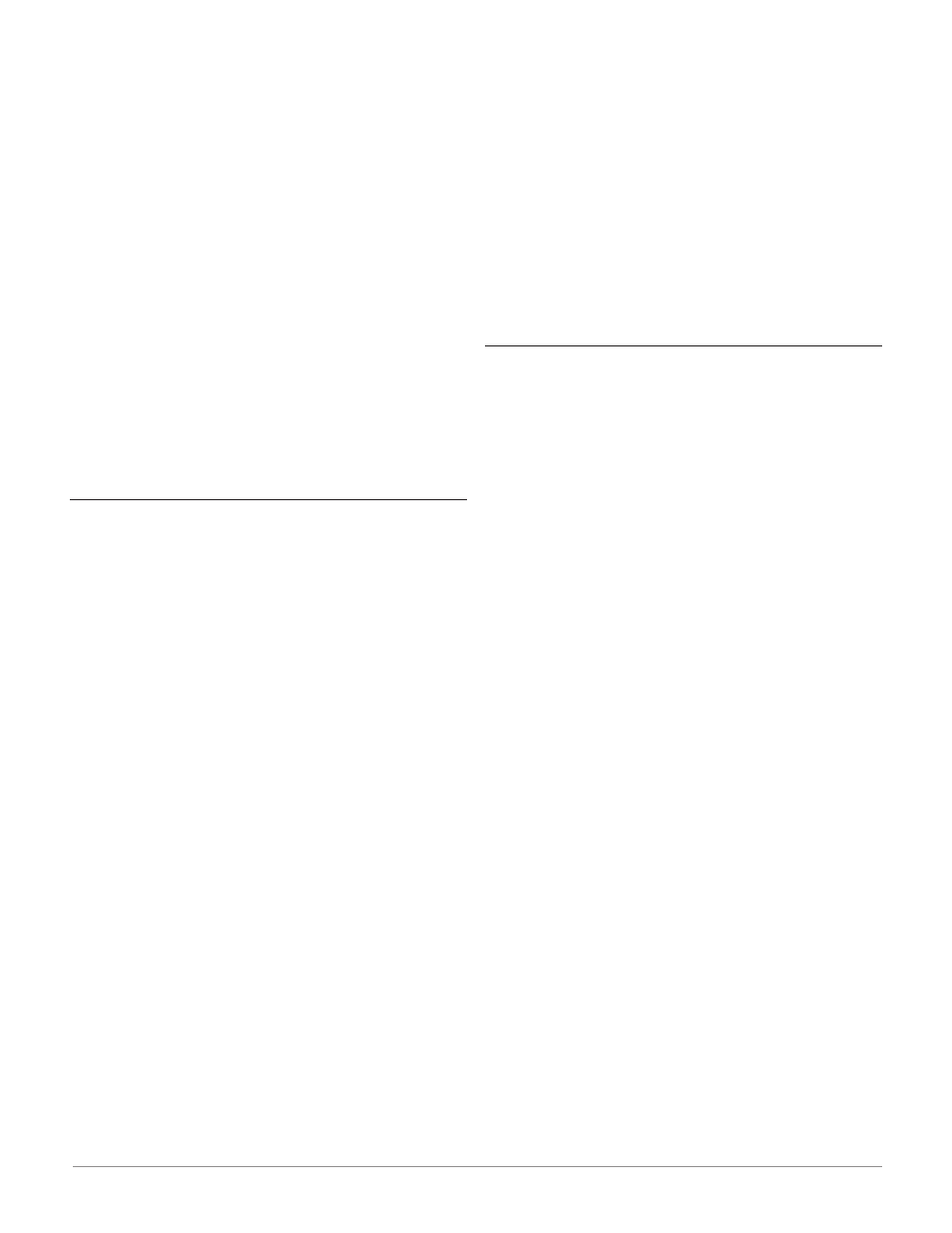
Watlow EZ-ZONE
®
ST
•
75
•
Chapter 7 Features
b. If Rolling Password [roll] is On, Password
[pass] equals:
([pas;u] x code) Mod 929 + 70
8. Administrator
a. If Rolling Password [roll] is Off, Password
[pass] equals User Password [pas;a].
b. If Rolling Password [roll] is On, Password
[pass] equals:
([pas;a] x code) Mod 997 + 1000
Differences Between a User Without Password,
User With Password and Administrator
- User without a password is restricted by the
Locked Access Level [loC;l].
- A User with a password is restricted by the
Read Lockout Security [rloC] never having ac-
cess to the Lock Menu [`loC].
- An Administrator is restricted according to the
Read Lockout Security [rloC] however, the Ad-
ministrator has access to the Lock Menu where
the Read Lockout can be changed.
Modbus - Using Programmable Memory
Blocks
When using the Modbus protocol, the ST control fea-
tures a block of addresses that can be configured by
the user to provide direct access to a list of 40 user
configured parameters. This allows the user easy ac-
cess to this customized list by reading from or writing
to a contiguous block of registers.
Note:
To use the User Programmable Memory Blocks fea-
ture, Map 2 must be selected. Change the mapping
[map]
via the Setup Page under the [Com] Menu.
To acquire a better understanding of the tables found
in the back of this manual (
See Appendix:
) please read through
the text below which defines the column headers used.
Assembly Definition Addresses
- Fixed addresses used to define the parameter
that will be stored in the "Working Addresses",
which may also be referred to as a pointer. The
value stored in these addresses will reflect (point
to) the Modbus address of a parameter within the
ST control.
Assembly Working Addresses
- Fixed addresses directly related to their associ-
ated "Assembly Definition Addresses" (i.e., As-
sembly Working Addresses 200 & 201 will assume
the parameter pointed to by Assembly Definition
Addresses 40 & 41).
When the Modbus address of a target parameter is
stored in an "Assembly Definition Address" its cor-
responding working address will return that param-
eter’s actual value. If it’s a writable parameter, writing
to its working register will change the parameter’s
actual value.
As an example, Modbus register 360 contains the
Analog Input 1 Process Value (See Operations Page,
Analog Input Menu). If the value 360 is loaded into
Assembly Definition Address 91, the process value
sensed by analog input 1 will also be stored in Mod-
bus registers 250 and 251. Note that by default this
parameter is also stored in working registers 240 and
241 as well.
The table (See Appendix: Modbus Programmable
Memory Blocks) identified as "Assembly Definition
Addresses and Assembly Working Addresses" reflects
the assemblies and their associated addresses.
CIP - Communications Capabilities
CIP Communications Methodology
To communicate with the ST using CIP an RUI/GTW
must be used. Reading or writing when using CIP can
be accomplished via explicit and or implicit communi-
cations. Explicit communications usually requires the
use of a message instruction but there are other ways
to do this as well. Implicit communications is also
commonly referred to as polled communications. When
using implicit communications there is an I/O assem-
bly that would be read or written to; the assemblies
are embedded into the ST firmware. Watlow refers
to these assemblies as the T to O (Target to Origina-
tor) and the O to T (Originator to Target) assemblies
where the Target is always the ST and the Origina-
tor is the PLC or master on the network. The O to T
assembly is made up of 20 (32 bit) members that are
user configurable where the T to O assembly consists
of 21 (32 bit) members. The first member of the T to
O assembly is called the Device Status and cannot be
changed. However, the 20 members that follow it are
user configurable (
See
Appendix:
(Originator to Target) Assembly Structure
and
(Target to Originator) Assembly Struc-
ture).
To change any given member of either assembly
simply write the new class, instance and attribute to
the member location of choice. As an example, if it
were desired to change the 14
th
member of the O to T
assembly from the default parameter (Heat Propor-
tional Band) to Limit Clear Request (see Operations
Page, Limit Menu) write the value of 0x70, 0x01 and
0x01 (Class, Instance and Attribute respectively
)
to
0x77, 0x01 and 0x0E. Once executed, writing a value
of zero to this member will reset a limit assuming the
condition that caused it is no longer present.